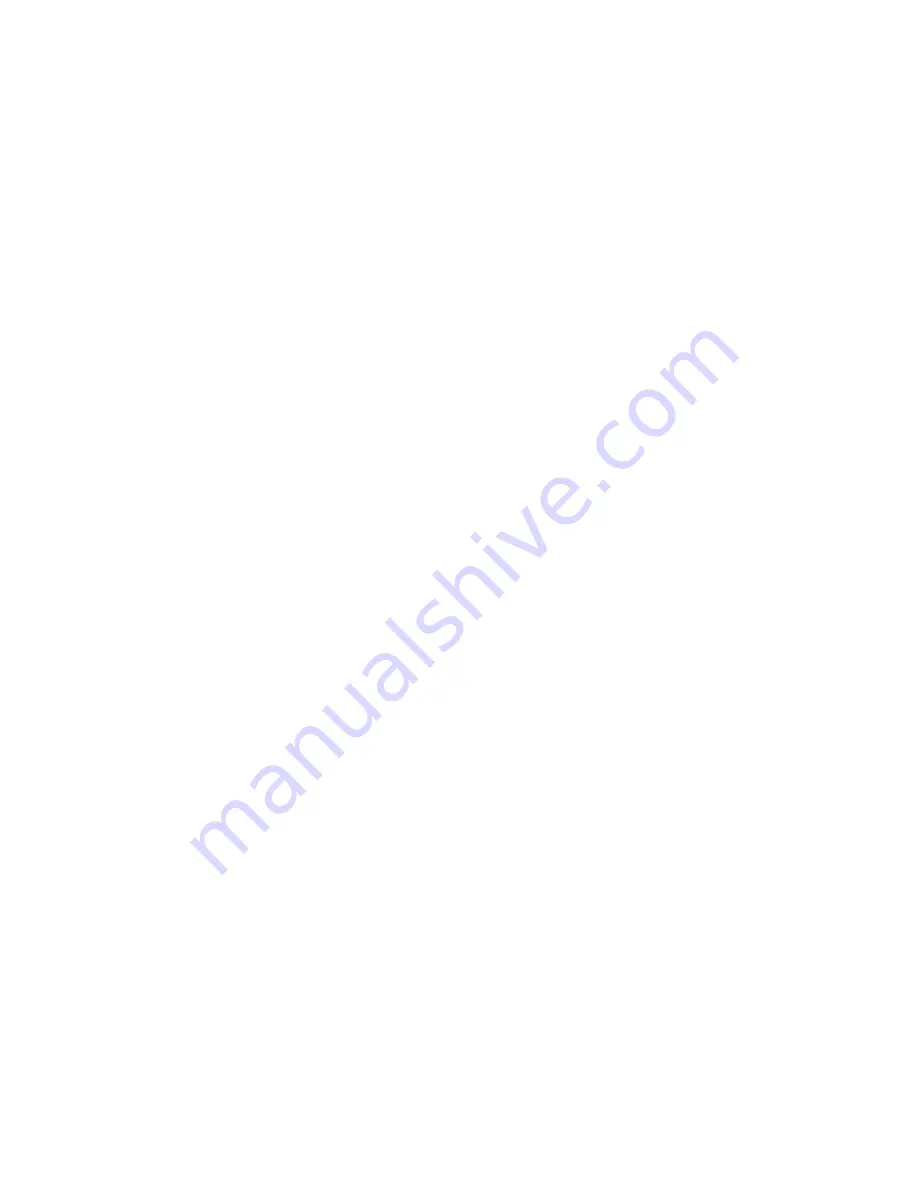
8
50spm x .000167gps x 1440 (minutes per day) = 12.02 gallons per day
Reducing the stroke length will reduce the pump’s output again. If the example pump above had it’s
stroke length reduced to 50% the 12.02 gallons per day output is reduced to 6.01. (Example: 12.02
gpd x 0.50 = 6.01 gpd)
A higher product viscosity will reduce the output. Pressures lower than the pump’s rating can increase
the output.
E. Optional Features
A pump’s output per minute can be determined by dividing the maximum rated gallons per day by 1440
(minutes per day). For example, a 30 gallons per day (gpd) pump at a maximum stroke length and
speed setting of 125 strokes per minute (spm) will pump 0.000167 gallons
1. External Pacing
The external pacing option allows the speed of the pump to be controlled by an external device like a
flow meter that gives dry contact switch closures. The pump sends out a 5 volt D.C. current to read a
switch closure. Each time the pump sees the switch closure it strokes once, up to its maximum strokes
per minute rate.
2. Hall Effect Meter Pacing
This option is like the external pacing only the pump divides the incoming switch closures by 9
before stroking on time. This is a three wire connection: D.C. voltage, signal and ground.
3. External Stop
Pumps with this option are allowed to stroke as long as they see a closed condition from a
dry contact source like a flow switch or drum level wand. When an open condition is seen the
pump is not allowed to stroke.
VI. Maintenance
The Advantage MicroTron™ pump is designed for long service life with minimum maintenance. If for any
reason, maintenance is necessary or desirable, the MicroTron™ pump is easily maintained.
Before any maintenance or service is performed, observe the following precautions:
1. Disconnect the MicroTron™ pump from power source.
2. Drain chemical from discharge tubing.
3. Disconnect discharge tubing from pump.
4. If the MicroTron™ pump is used in a flooded suction application, remove foot valve
from chemical container.
5. Observe relevant safety protocols when handling parts which have been in contact with
hazardous
chemicals.
Summary of Contents for MicroTron O Series
Page 13: ...13 Application Notes ...
Page 14: ...14 Application Notes ...
Page 15: ...15 Application Notes ...