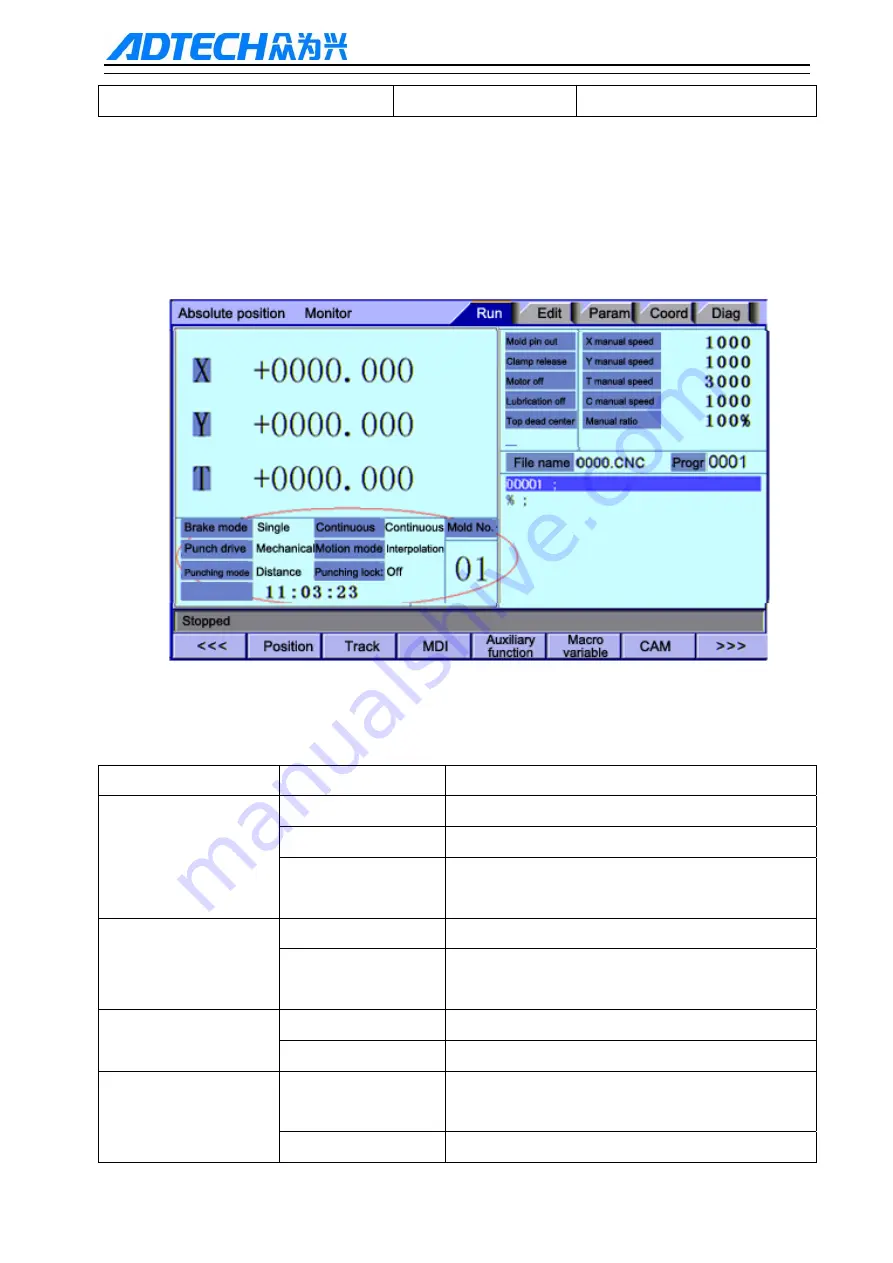
NCT-04/03/02 Punch CNC System (Commissioning Manual)
Relocation clamp forward distance
P1.098
3.6.3
Test Code
Refer to "Programming Manual" 7. Relocation instructions for details
3.7
Punching Status Display Interface
3.7.1
Interface Introduction
The following Fig. 3 - 1 shows the punch status display interface:
Fig. 3-1
Table 3 - 1 is the punch state description:
Table 3-1
Function
Parameter
Introduction
Brake mode
Feeding
Feeding signal as the off clutch signal
Single stop
Single stopping top dead center as off clutch signal
Double stop
Single / continuous punching off clutch is controlled
by a separate switch signal
Single/Continuous
Single
The system will pause after punching a hole
Continuous
Punching process does not stop until the end of the
program
Punch drive
Mechanical
The punch main drive is mechanical
Hydraulic
The punch main drive is mechanical flywheel
Running mode
Point
The starting speed, acceleration and rapid traverse
speed can be set for each feeding axis individually.
Interpolation
Feeding axes arrive simultaneously