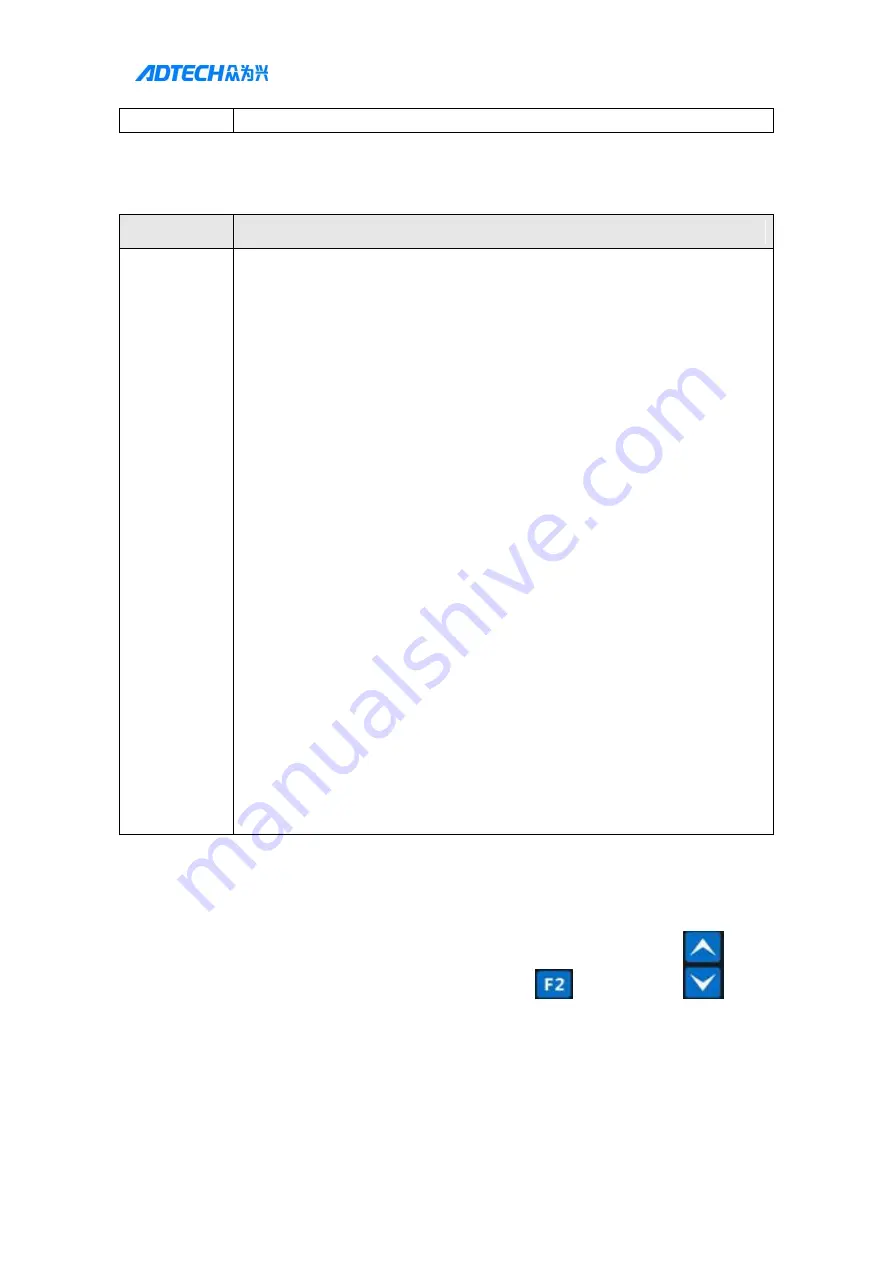
User Manual of TV5600-B01 Series Dispensing Control System
63
6)
Remote network port: Network port number for visual communication
8.02.04 Otherfactory parameters
Description
1.
Vendor parameter password setting
2.
Language selection
3.
Stop button lift reset: Set whether the motor is reset at the same time
when the stop button is lifted. Generally, it refers to the external
emergency stop self-locking button
4.
Start button plus pause function: Press the start button to pause in the
running process
5.
Extended IO settings: Connect to external expansion IO board, external
input and output portscan be added
6.
Jog distance: The distance of manual jog
7.
Corner speed smoothing level: Increasing the corner speed smoothing
level will improve the overall processing efficiency and motion stability,
but will also cause a large single-axis start-stop speed at the corner
8.
Track splitting accuracy: The controller divides all the graphics into small
line segments of equal length0. The track splitting precision is the length
of the small line segments. If the setting is too small, the controller will
calculate too much and affect the motion effect. It is generally
recommended that the value be greater than the distance that the motor
rotates by 1/50 of a turn
9.
Z-axis lift during positioning: Whether Z is raised when positioning
10.
Automatic speed smoothing: Motion smoothing
11.
Vendor service period setting
12.
User service periodsetting
13.
Restore backup system parameters
14.
Restore parameters to factory defaults
8.02 Motor speed related parameters
1. ->In handheld box system parameter interface -> Press [
Motor speed] ->
enter
parameters ->
Summary of Contents for DJ1600V1-A01
Page 1: ...I TV5600 B01 Series Dispensing Control System User Manual ...
Page 2: ...User Manual of TV5600 B01 Series Dispensing Control System 2 ...
Page 15: ...User Manual of TV5600 B01 Series Dispensing Control System 15 Front view Side view Side view ...
Page 47: ...User Manual of TV5600 B01 Series Dispensing Control System 47 ...
Page 123: ...User Manual of TV5600 B01 Series Dispensing Control System 123 ...