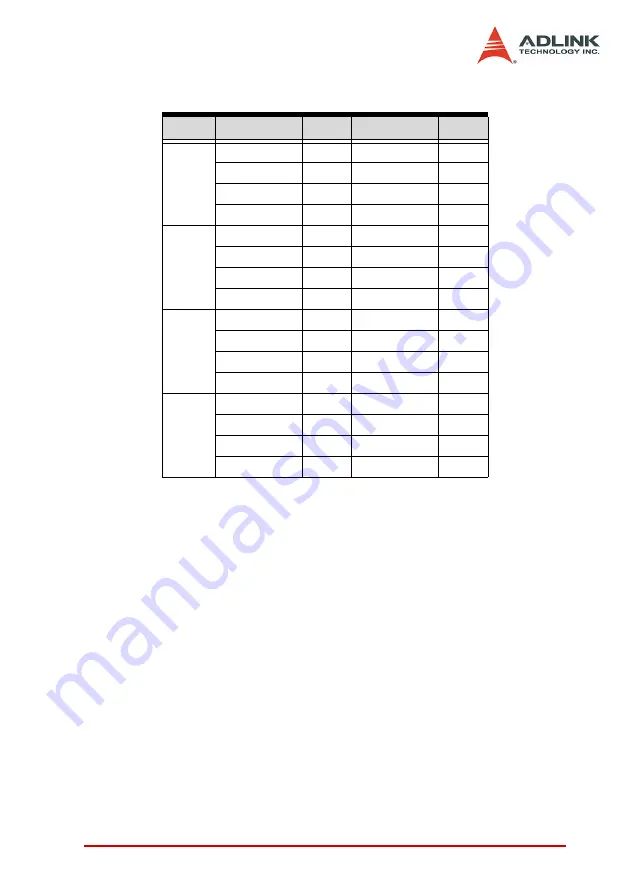
Introduction
7
X
CMRR: (DC to 60Hz, Typical)
X
Time-base source:
Z
Internal 40MHz or External clock Input (fmax: 40MHz,
fmin: 1MHz, 50% duty cycle)
X
Trigger modes:
Z
Post-trigger, Delay-trigger, Pre-trigger and Middle-trigger
X
Data transfers:
Z
Programmed I/O, and bus-mastering DMA with scatter/
gather
X
Input coupling: DC
X
Offset error:
Z
Before calibration: ±60mV max
Z
After calibration: ±1mV max
X
Gain error:
Device Input Range CMRR Input Range CMRR
2010
±10V 90
dB
0~10V
89
dB
±5V
92 dB
0~5V
92 dB
±2.5V
95 dB
0~2.5V
94 dB
±1.25V
97 dB
0~1.25V
97 dB
2005
±10V 86
dB
0~10V
85
dB
±5V
88 dB
0~5V
88 dB
±2.5V
91 dB
0~2.5V
90 dB
±1.25V
93 dB
0~1.25V
93 dB
2006
±10V 87
dB
0~10V
86
dB
±5V
89 dB
0~5V
88 dB
±2.5V
91 dB
0~2.5V
91 dB
±1.25V
93 dB
0~1.25V
93 dB
2016
±10V
85dB
0~10V
86dB
±5V
88dB
0~5V
88dB
±2.5V
91dB
0~2.5V
92dB
±1.25V
95dB
0~1.25V
95dB
Table 1-3: CMRR: (DC to 60Hz)
Summary of Contents for DAQ/PXI-20 Series
Page 5: ......
Page 11: ......
Page 81: ...70 Operation Theory VHDCI Connecting them to any signal source may cause per manent damage ...