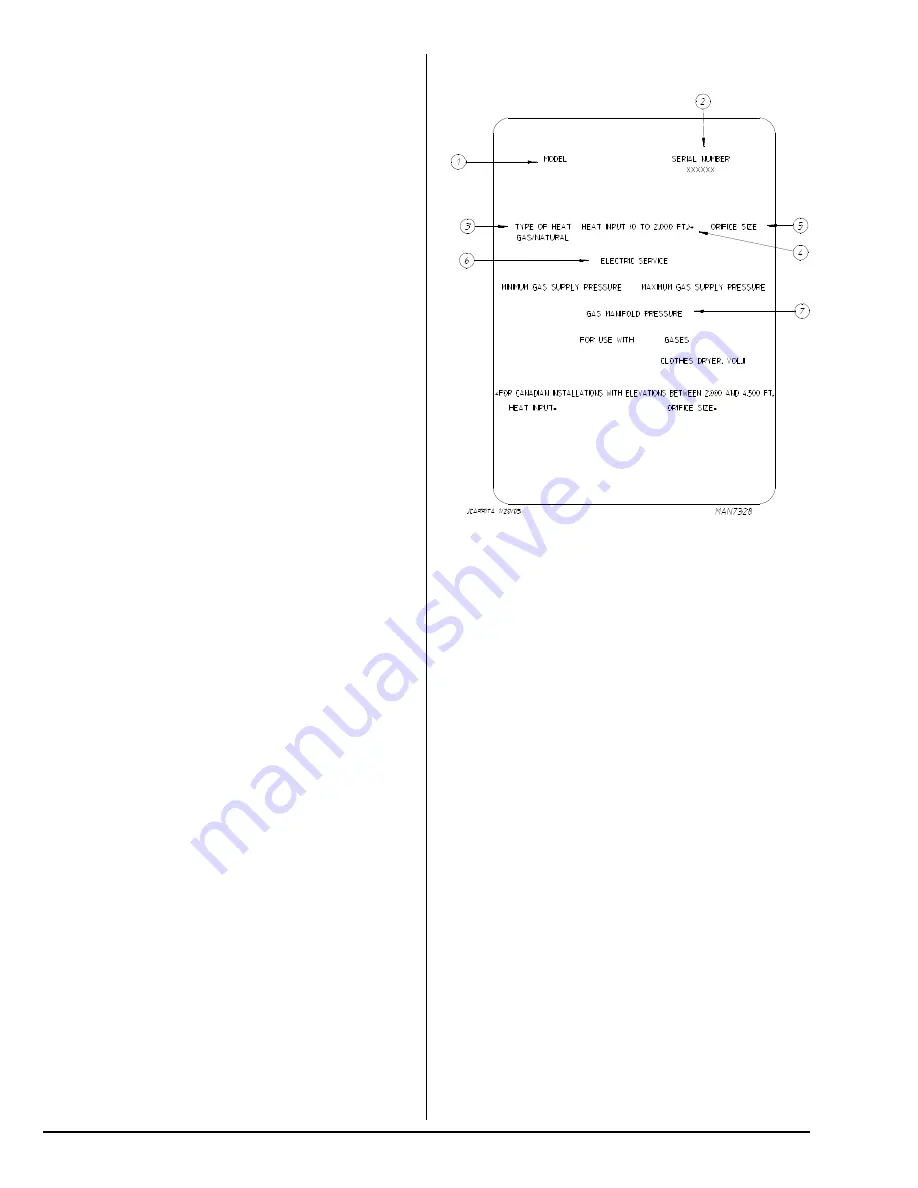
18
American Dryer Corp.
112174-7
Data Label Information _______________
Every Six Months
Inspect and remove lint accumulation in customer furnished
exhaust ductwork system and from dryer’s internal exhaust
ducting.
NOTE:
The accumulation of lint in the exhaust ductwork
can create a potential fire hazard.
Do not obstruct the flow of combustion and ventilation air.
Check customer furnished back draft dampers in the
exhaust ductwork. Inspect and remove any lint
accumulation, which can cause the damper to bind or
stick.
A back draft damper that is sticking partially closed can
result in slow drying and shutdown of heat circuit safety
switches or thermostats.
When cleaning the dryer cabinet(s), avoid using harsh
abrasives. A product intended for the cleaning of
appliances is recommended.
Adjustments
7 Days After Installation
and Every Six Months Thereafter
Inspect bolts, nuts, screws, setscrews, grounding
connections, and nonpermanent gas connections (unions,
shutoff valves, and orifices). Motor and drive belt should be
examined. Cracked or seriously frayed belt should be
replaced. Tighten loose belts when necessary. Complete
operational check of controls and main valves. Complete
operational check of all safety devices (door switch, lint drawer
switch, sail switch, burner and exhaust hi-limit thermostats).
Lubrication
The motor bearings and under normal/most conditions the
tumbler bearings are permanently lubricated. It is physically
possible to relubricate the tumbler bearings if you choose to
do so even though this practice is not necessary. Use Shell
Alvania #2 grease or its equivalent. The tumbler bearings
used in the dryer do not have a grease fitting. Provisions are
made in the bearing housing for the addition of a grease
fitting, which can be obtained elsewhere, or from ADC by
ordering kit P/N 882159 (includes two fittings).
When contacting ADC, certain information is required to
ensure proper service/parts information from ADC. This
information is on the data label affixed to the right side panel
area at the rear of the dryer. When contacting ADC, please
have the model number and serial number available.
1.
Model Number
– This describes the style of dryer and
type of heat (gas, electric, or steam).
2.
Serial Number
– Allows the manufacturer to gather
information on your particular dryer.
3.
Type of Heat
– This describes the type of heat for your
particular dryer, gas (either natural gas or L.P. gas),
electric, or steam.
4.
Heat Input
(For Gas Dryers) – This describes the heat
input in British thermal units per hour (Btu/hr) or kilowatts
(kW).
5.
Orifice Size
(For Gas Dryers) – Gives the number drill
size used.
6.
Electric Service
– This describes the voltage and current
rating for a particular model.
7.
Gas Manifold Pressure
(For Gas Dryers) – This
describes the manifold pressure taken at the gas valve
tap.
Summary of Contents for AD-444
Page 20: ...ADC Part No 112174 7 09 02 14 ...