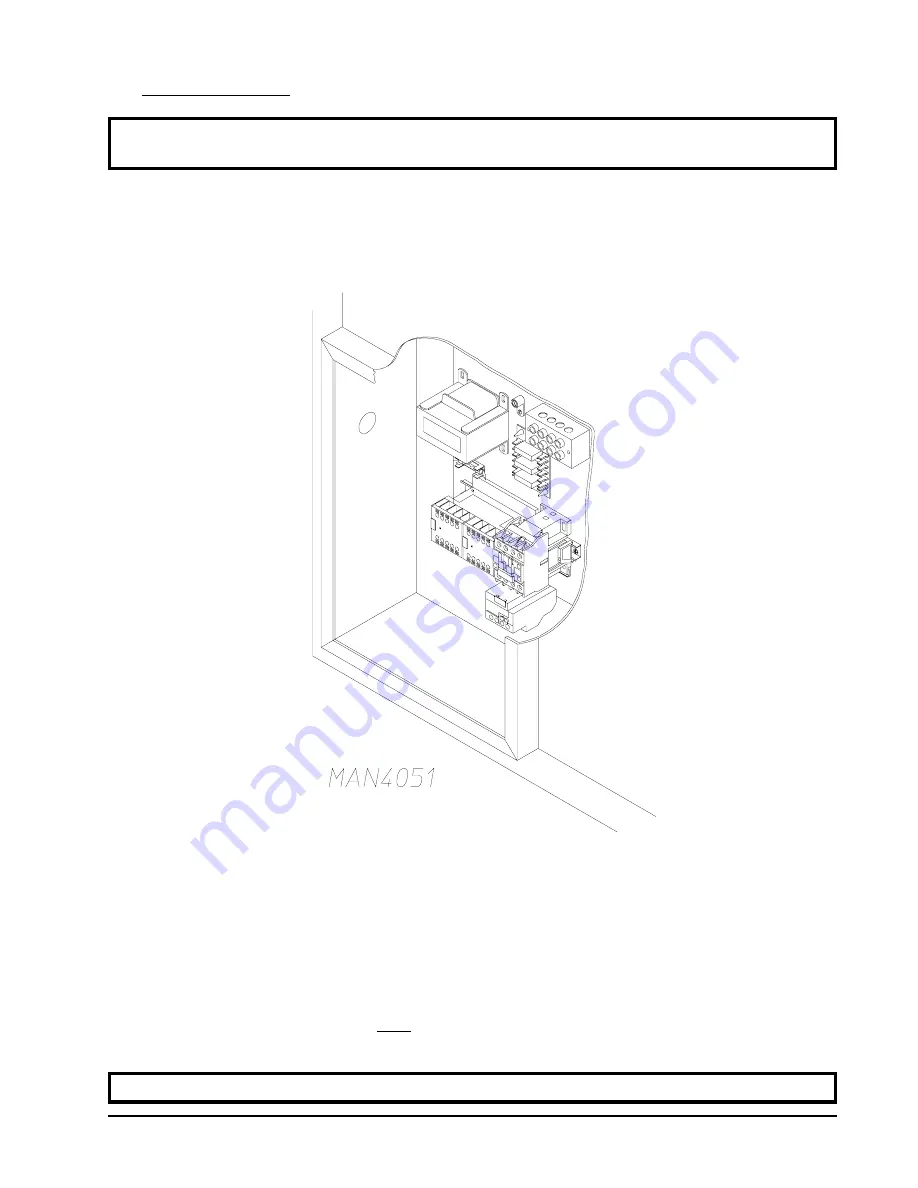
113354-23
25
3. Electrical Connections
NOTE: A wire diagram is included with each dryer and is affixed to the back side of the top control
(access) door.
The only electrical input connections to the dryer are the 3-phase (3ø) power leads (L1, L2, and L3),
GROUND, and in the case of 4 wire service, the NEUTRAL. These electrical connections are made at
the terminal block located in the service/relay box at the rear, upper left hand corner of the dryer. To gain
access into this service box, the service cover must be removed.
The “LINE POWER” and the “GROUND” connections to the dryer must be made through the knockout
hole at the top of the electric service/relay box. A strain relief must be used where the line power ground
wires go into the electric service/relay box.
Providing local codes permit, power connections to the dryer can be made by use of a flexible underwriters
laboratory list cord/pigtail (wire must conform to ratings of the dryer), or the dryer can be hard wired
directly to the service breaker. In ALL cases, a strain relief must be used where the wire(s) enter the
dryer’s electrical service (relay) box.
NOTE: A CIRCUIT SERVICING EACH DRYER MUST BE PROVIDED.
Summary of Contents for AD-190
Page 60: ...ADC Part No 113354 23 06 21 21...