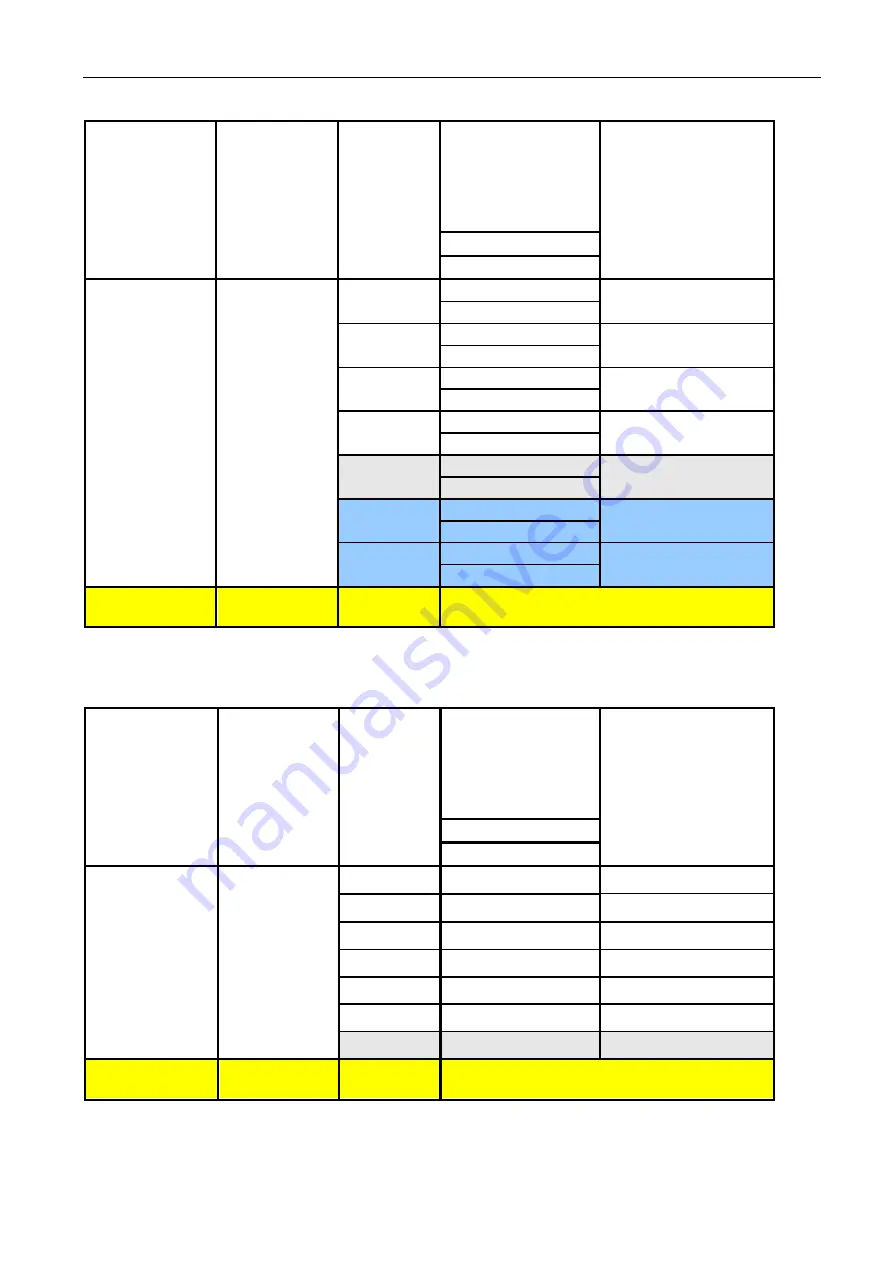
USER’S MANUAL
V-line 46xx, 47xx
37
Table 1 – Operating flow rate of the fuel dispenser in relation on the fuel storage tanks parameters for
hydraulic unit with Q
max
= 40 dm
3
.min
-1
.
Geodetic
suction head
Hsg
max
[ m ]
Inner diameter
of suction
piping
DN
min
[ mm ]
Length
of suction
piping
L [ m ]
Operating flow rate
of the fuel
disppenser without
vapour recovery
Q [ dm
3
. min
-1
]
±10
%
Supposed loss in
pressure in suction
piping
[ kPa ]
Petrol
Diesel oil
3
40
10
40
13
40
20
40
14
40
25
35
15
40
30
35
16
40
35
30
17
35
40
25
18
35
45
20
19
30
–
50
Greater
than 35
Pressure system – submersible pump in the
tank
Table 2 – Operating flow rate of the fuel dispenser in relation on the fuel storage tanks parameters
for hydraulic unit with Q
max
= 80 dm
3
.min
-1
.
Geodetic
suction head
Hsg
max
[ m ]
Inner
diameter of
suction piping
DN
min
[ mm ]
Length
of suction
piping
L [ m ]
Operating flow rate
of the fuel
disppenser without
vapour recovery
Q [ dm
3
. min
-1
]
±10
%
Supposed loss in
pressure in suction
piping
[ kPa ]
Petrol
Diesel oil
3
50
10
80
14
20
80
15
25
80
16
30
75
17
35
75
18
40
70
19
45
65
20
–
50
Greater
than 45
Pressure system – submersible pump in the
tank