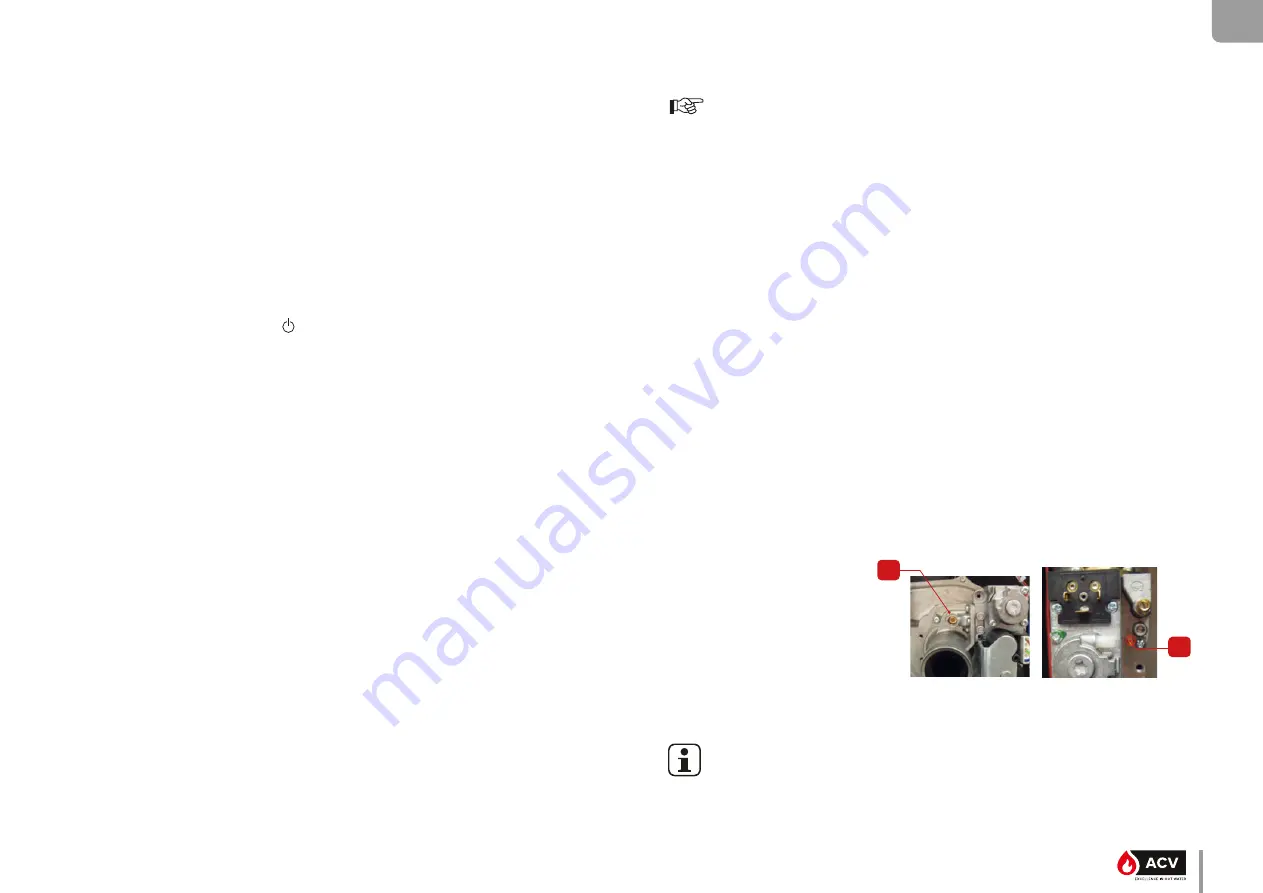
1
1
PRESTIGE 42-50-75-100-120 Solo : A1007856 - 664Y6200 • G
EN
FR
NL
ES
IT
DE
PL
RU
en
39
STARTING UP
STARTING UP THE BOILER
Set-up conditions
• All connections made
• Gas conversion carried out as required
• Condensate trap full of water
• Electrical power supply on
• Gas supply open
• Hydraulic circuit full of water
Procedure
1. Check that there is no gas leak.
2. Push in the ON/OFF master switch ( ).
3. If a room thermostat is installed, possibly increase the temperature set-point to generate a
demand.
4. Check the gas pressure and allow the boiler to heat up for a few minutes
5. Check and adjust the burner according to local standards and regulations, refer to “Checking
and Adjusting the Burner” on page 39.
6. Set the central heating temperature to the required value using the control panel. Refer to
“Boiler Setup Guide” on page 8 and to the Installer’s Handbook (or the ACVMax System
Control manual, depending on the boiler build, refer to page 3.)
7. After 5 minutes of operation, bleed the heating circuit until all air is evacuated and restore a
1.5 bar pressure.
8. Bleed the central heating circuit once again and top it up with water to get the required pres-
sure, if necessary.
9. Make sure that the central heating system is properly balanced and, if needed, adjust the
valves to prevent certain circuits or radiators from getting a flow rate that is far above or below
the set rate.
Follow-on tasks
1. Check that there are no leaks.
2. Check that the flow rate in the appliance is sufficient as follows :
• Operate the boiler at maximum power
• Once the temperatures are stable, read out the supply and return temperatures
• Check that the difference between the supply and return temperature is equal or less than
20k.
• If the Delta T is higher than 20k, check the pump settings/specifications.
CHECKING AND ADJUSTING THE BURNER
When the burner operates at full power, the CO
2
rate must be within the limits mentioned
in the technical characteristics, (see “Combustion Characteristics” on page 18).
Set-up conditions
• Operating boiler
Procedure
1. Check if the ACVMAX parameters are set to meet the user's requirements (refer to “Boiler Setup
Guide” on page 8), and change them if required.
2. Put the boiler to maximum power mode (Refer to the Installer’s Handbook (or the ACVMax System
Control manual, depending on the boiler build, refer to page 3)).
3. Using a pressure tester, check that the dynamic gas pressure at the gas valve is at least 18 mbar.
4. Allow the appliance to heat for a few minutes until it reaches at least 60°C.
5. Make sure that the front panel is closed.
6. Measure the burner combustion by placing the flue gas analyser probe into the measurement unit
port on the flue pipe and compare the CO and CO
2
values displayed with those indicated in the
combustion characteristics table. Refer to “Combustion Characteristics” on page 18.
7. Open the front panel, refer to “Removal and Installation of the Front and Top Panels” on page 32.
8. Measure the CO
2
. If the difference in CO
2
Max power with and without front panel is > 0.4% (abso-
lute), then check the flue system for recirculation.
9. If the CO
2
value (front panel closed) differs by more than 0.3% from the value mentioned in the
“Combustion Characteristics” on page 18, carry out the adjustment mentioned in the procedure
below.
10. Then put the boiler to the minimum power mode (Refer to the Installer’s Handbook (or the ACVMax
System Control manual, depending on the boiler build, refer to page 3)). Allow the boiler to stabilize
for a few minutes.
11. Measure the CO
2
level. It must be equal to the value at full power, or lower than that value by 0.5%
maximum. In case of significant deviation, please contact ACV's maintenance department.
CO2 adjustment procedure
To adjust the CO
2
rate, rotate the venturi
screw (
1
) :
• to the left (counter-clockwise) to in-
crease the CO
2
rate.
• to the right (clockwise) to decrease the
CO
2
rate.
Follow-on tasks
None
The CO
2
adjustment screw (1) of the Prestige 100 - 120 Solo is a worm screw, whose
rotation in a direction causes the CO
2
rate to cyclically increase to the maximum, then
decrease to the minimum, then increase again, and so on. To adjust, monitor the value
change on the analyzer to determine whether the rotation in the selected direction
causes the CO
2
value to increase or decrease
Prestige 42 - 50 - 75 Solo
Prestige 100 - 120 Solo