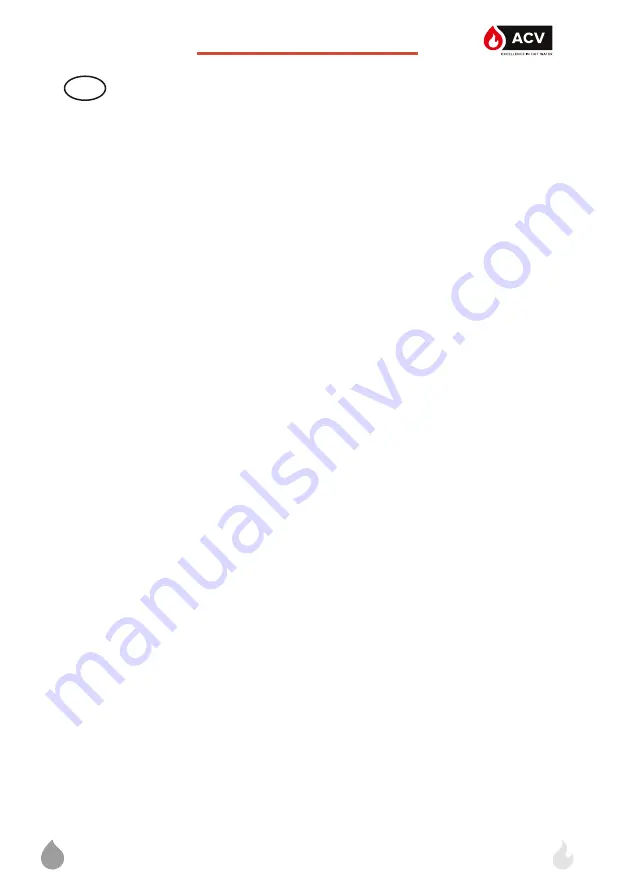
3.55
Any discharge should be visible at the tundish. In addition, where discharges from
safety devices may not be apparent, e.g. in dwellings occupied by people with impai-
red vision or mobility, consideration should be given to the installation of a suitable
safety device to warn when discharge takes place, e.g. electronically operated.
Discharge pipe D2
3.56 The discharge pipe (D2) from the tundish should:
(a) have a vertical section of pipe at least 300mm long below the tundish before any
elbows or bends in the pipework; and
(b) be installed with a continuous fall thereafter of at least 1 in 200.
3.57 The discharge pipe (D2) should be made of:
(a) metal; or
(b) other material that has been demonstrated to be capable of safely withstanding
temperatures of the water discharged and is clearly and permanently marked to iden-
tify the product and performance standard (e.g. as specified in the relevant part of BS
7291)
3.58 The discharge pipe (D2) should be at least one pipe size larger than the nominal outlet
size of the safety device unless its total equivalent hydraulic resistance exceeds that
of a straight pipe 9m long, i.e. for discharge pipes between 9m and 18m the equivalent
resistance length should be at least two sizes larger than the nominal outlet size of the
safety device; between 18 and 27m at least 3 sizes larger, and so on; bends must be
taken into account in calculating the flow resistance. See figure, table and the worked
example.
3.59 Where a single common discharge pipe serves more than one system, it should be at
least one pipe size larger than the largest individual discharge pipe (D2) to be connec-
ted.
3.60 The discharge pipe should not be connected to a soil discharge stack unless it can
be demonstrated that that the soil discharge stack is capable of safely withstanding
temperatures of the water discharged, in which case, it should:
(a) contain a mechanical seal, not incorporating a water trap, which allows water into
the branch pipe without allowing foul air from the drain to be ventilated through the
tundish;
(b) be a separate branch pipe with no sanitary appliances connected to it;
(c) if plastic pipes are used as branch pipes carrying discharge from a safety device
they should be either polybutalene (PB) to Class S of BS 7291-2:2006 or cross linked
polyethylene (PE-X) to Class S of BS 7291-3:2006; and (d) be continuously marked
with a warning that no sanitary appliances should be connected to the pipe.
Note:
1. Plastic pipes should be joined and assembled with fittings appropriate to the circums-
tances in which they are used as set out in BS EN ISO 1043-1.
2. Where pipes cannot be connected to the stack it may be possible to route a dedicated
pipe alongside or in close proximity to the discharge stack.
Termination of discharge pipe
3.61 The discharge pipe (D2) from the tundish should terminate in a safe place where there
is no risk to persons in the vicinity of the discharge.
3.62 Examples of acceptable discharge arrangements are:
(b) to a trapped gully with the end of the pipe below a fixed grating and above the
water seal;
(c) downward discharges at low level; i.e. up to 100mm above external surfaces such
as car parks, hard standings, grassed areas etc. are acceptable providing that a wire
UK
HR s & Jumbo : A1007851 - 661Y1200 • E
Installation
19
EN
Summary of Contents for HR s 1000
Page 5: ...HR s Jumbo A1007851 661Y1200 E Product Information ENERGY LABELLING 5 EN...
Page 23: ...HR s Jumbo A1007851 661Y1200 E Installation 23 EN Install the rating plate sticker here...
Page 25: ...HR s Jumbo A1007851 661Y1200 E Installation 25 EN 8 10 9 2 x 11...
Page 26: ...HR s Jumbo A1007851 661Y1200 E Installation EN 26 5 16 14 15 13 12...
Page 36: ......