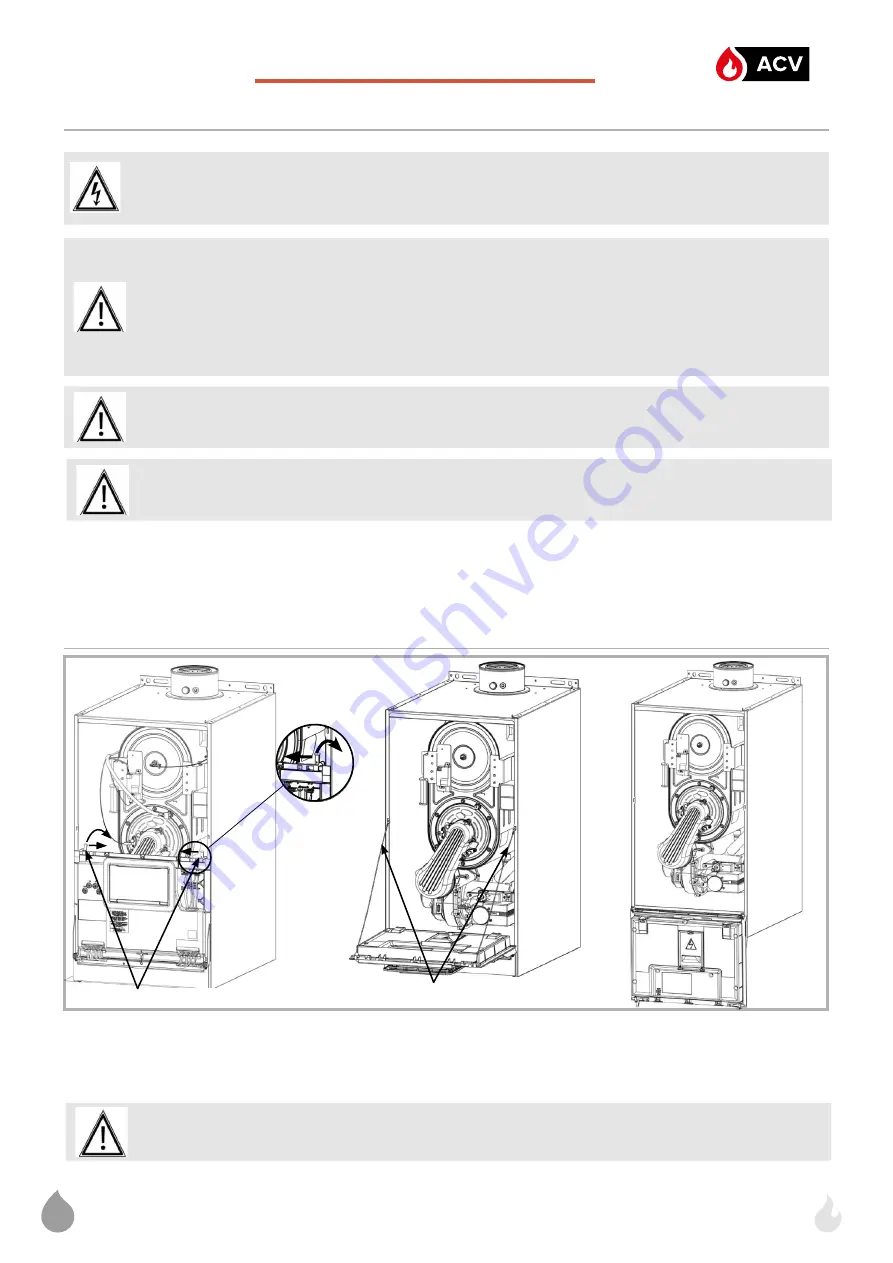
EVO S
, Installation, Commisioning and Servicing Instructions
41
EN
4.7. Electrical connection
WARNING:
Ensure that the general electrical power supply has been cut off
before starting any repair work
.
CAUTION:
It is mandatory to connect this boiler correctly to earth and to comply
with standard for low-voltage electrical installations.
Provide a two-pole circuit breaker upstream of the boiler (distance
between contacts: 3.5 mm minimum).
Fitting the electrical installation with a 30 mA differential protective
device is strongly advised.
Please refer to the installation and user manuals of the NAVISTEM B3100
boiler controller for more information about the electrical connections on
the control panel (characteristics of the electric power supply, cable cross-
sections and connections to the terminals).
4.7.1. Control panel
IMPORTANT:
The front plastic panel must be replaced before starting up the boiler.
To access the control panel, remove the front of the boiler see chapter 4.2.
Push the latches forward and slide them inwards to unlock and tilt the control box.
It is possible to completely tilt the control box by removing the
lanyards
, in
Figure 17 - Access to NAVISTEM B3100
Latches
00U07444570-A
Lanyards
CAUTION :
Do not place anything on the control panel.
order to facilitate access to the interior of the boiler.
ATTENTION :
Compulsory use of the connector supplied with the product.
Summary of Contents for EVO S 100
Page 2: ......
Page 13: ... EVO S Installation Commisioning and Servicing Instructions 13 EN ...
Page 44: ...EVO S Installation Commisioning and Servicing Instructions EN 44 Figure 19 Wiring diagram ...
Page 45: ...EVO S Installation Commisioning and Servicing Instructions 45 EN ...
Page 149: ...EVO S Installation Commisioning and Servicing Instructions 149 EN ...
Page 150: ...EVO S Installation Commisioning and Servicing Instructions EN 150 ...
Page 151: ...EVO S Installation Commisioning and Servicing Instructions 151 EN ...
Page 152: ...EVO S Installation Commisioning and Servicing Instructions EN 152 ...
Page 153: ...EVO S Installation Commisioning and Servicing Instructions 153 EN ...