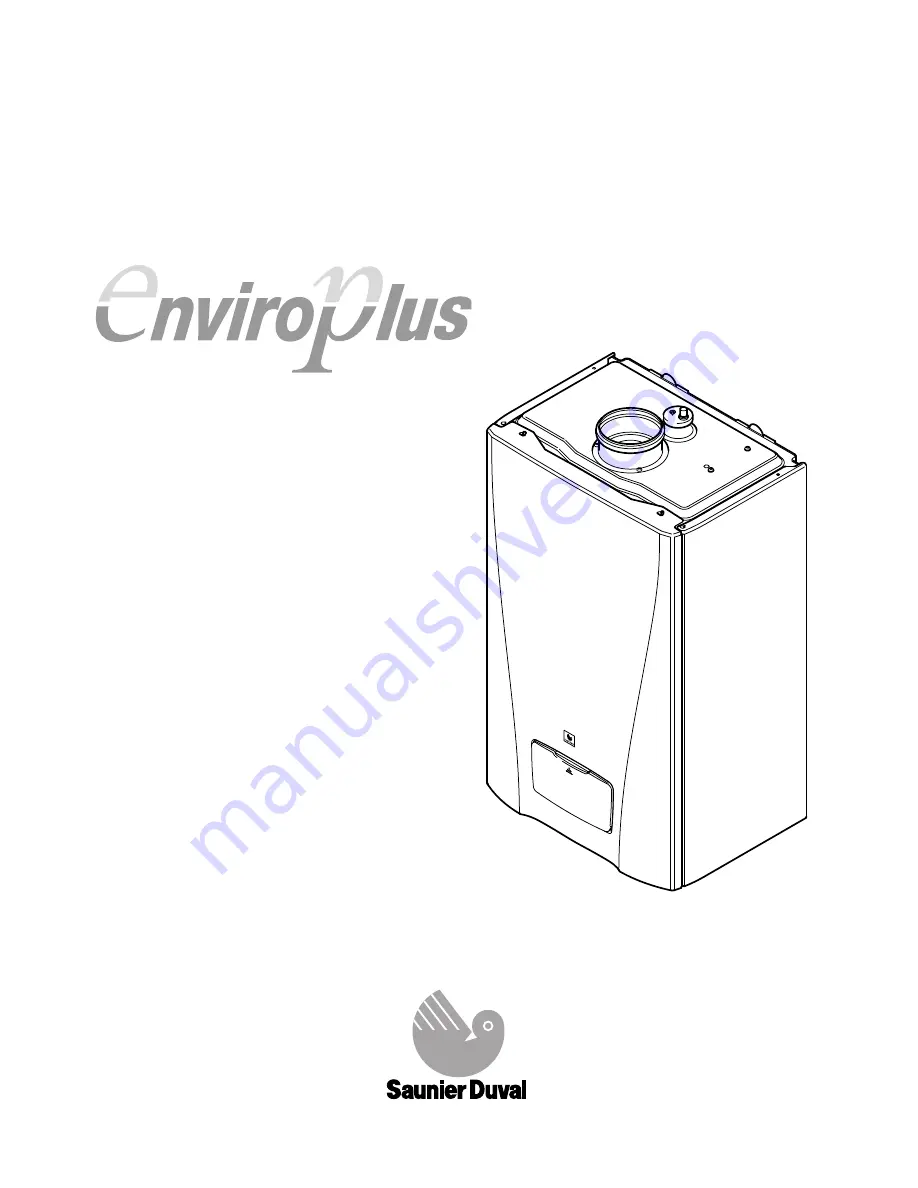
2000225294A.04.04
To b e l e f t w i t h t h e u s e r
Instructions for Use
Installation and Servicing
11915
Saunier Duval,
Nottingham Road, Belper, Derbyshire. DE56 1JT
www.saunier-duval.co.uk
HIGH EFFICIENCY
CONDENSING COMBINATION BOILER
G.C. No. 47-920-39
F28e
HIGH EFFICIENCY
CONDENSING SYSTEM BOILER
G.C. No. 41-920-37
F28e SB
HIGH EFFICIENCY
CONDENSING COMBINATION BOILER
G.C. No. 47-920-45
F24e
Summary of Contents for EnviroPlus F24e
Page 18: ...18 2000225294A Diagram 5 1 11907 5 Boiler Schematic F24e F28e ONLY ...
Page 19: ...19 2000225294A 5 Boiler Schematic Diagram 5 1a 12248 BYPASS F28e SB ONLY ...
Page 49: ...49 2000225294A 14 Fault Finding 12410 Diagram 14 4 ...
Page 51: ...51 2000225294A 15 Wiring Diagram Diagram 15 1a 12240 F28e SB ONLY ...