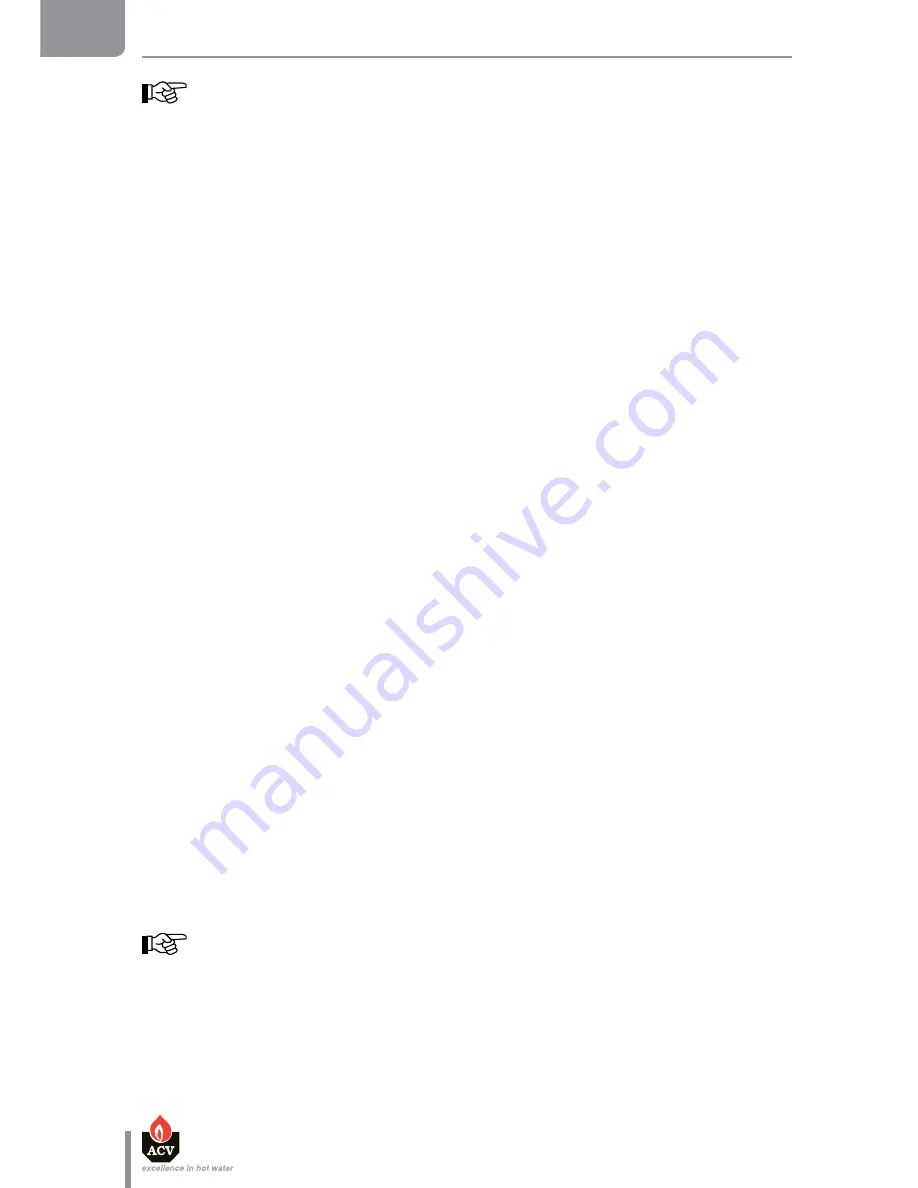
EN
en
36
Maintenance
664Y5900 • A
It is recommended to stop the boiler and have it serviced during good weather
conditions.
cleaninG the bUrner and the heatinG body
Set-up conditions
•
Boiler shut-down
•
External power supply isolated
•
Oil supply closed
Procedure
1. Open the front panel.
2. Release the burner flange and place the burner in the maintenance position to clean it (see the
burner manual).
3. Remove the burner
4. Open the heating body door.
5. Using a brush, clean the soot that may be present in the heating body and on the turbulators.
6. Check the correct position of the braid.
Follow-on tasks
•
Close the door and tighten with sufficient torque to ensure it is sealed against combustion
products.
•
Reinstall the burner flange and the burner.
•
Close the front panel.
cleaninG the condenser
Set-up conditions
•
Boiler shut-down
•
External power supply isolated
•
Oil supply closed
Procedure
1. Disconnect the flue pipe at the flue exhaust duct connection.
2. Inspect the inside and clean as required:
•
If the condenser is moderately dirty, pour a mixture of water and liquid soap (dish-washing
type).
•
If the condenser is very dirty, open the rear side panel, or the rear panel (
A
), to access the
condenser. Open the condenser (
B
) and clean it using a synthetic bristle brush.
Do not use the same brush as the one used to clean the heating body to prevent any
risks of corrosion.
Summary of Contents for BNE 2 Condens
Page 1: ...EN 21 8 kW BNE 2 Condens 664Y5900 A Installation operation and maintenance instructions ...
Page 22: ...EN en 22 Installation 664Y5900 A Boiler Preparation 5 3 4 1 2 6 ...
Page 23: ...en 23 EN Installation 664Y5900 A 9 8 10 11 7 1 2 ...
Page 24: ...EN en 24 Installation 664Y5900 A Burner installation 2 6 3 4 90 mm 5 1 1 2 ...
Page 25: ...en 25 EN Installation 664Y5900 A 8 2 1 7 9 ...
Page 40: ...EN en 40 664Y5900 A Declaration of conformity EC ...
Page 41: ...en 41 EN 664Y5900 A Declaration of conformity RD 17 7 2009 ...
Page 42: ...EN en 42 664Y5900 A Markings Labels Pending approval ...