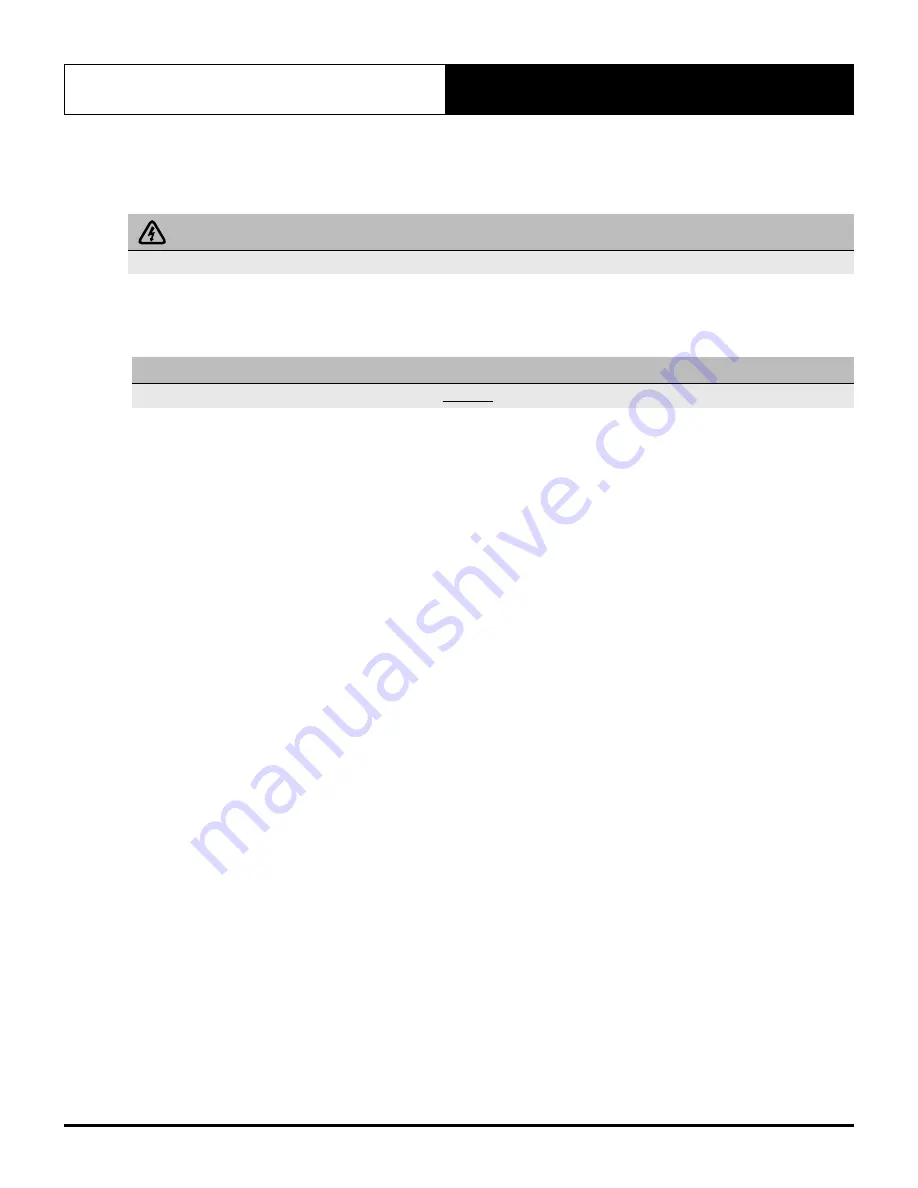
Installation and Commissioning Guide - Wall Hung Split System
Doc. No.9590-5007
Ver. 2 210416
Installation and Commissioning Guide
Wall Hung Split System
42
13.01. Electrical Safety Checks
After installation, confirm that all electrical wiring is installed in accordance with local and national regulations.
WARNING
All wiring must comply with local and national electrical codes, and must be installed by a licensed electrician.
13.02. Gas Leak Checks
Proper pressure test with dry nitrogen should be performed, prior to air evacuation. Perform leak detection test with
electronic leak detector after letting refrigerant into pipework
NOTE
After confirming that the all pipe connection points
DO NOT
leak, replace the valve cover on the outside unit.