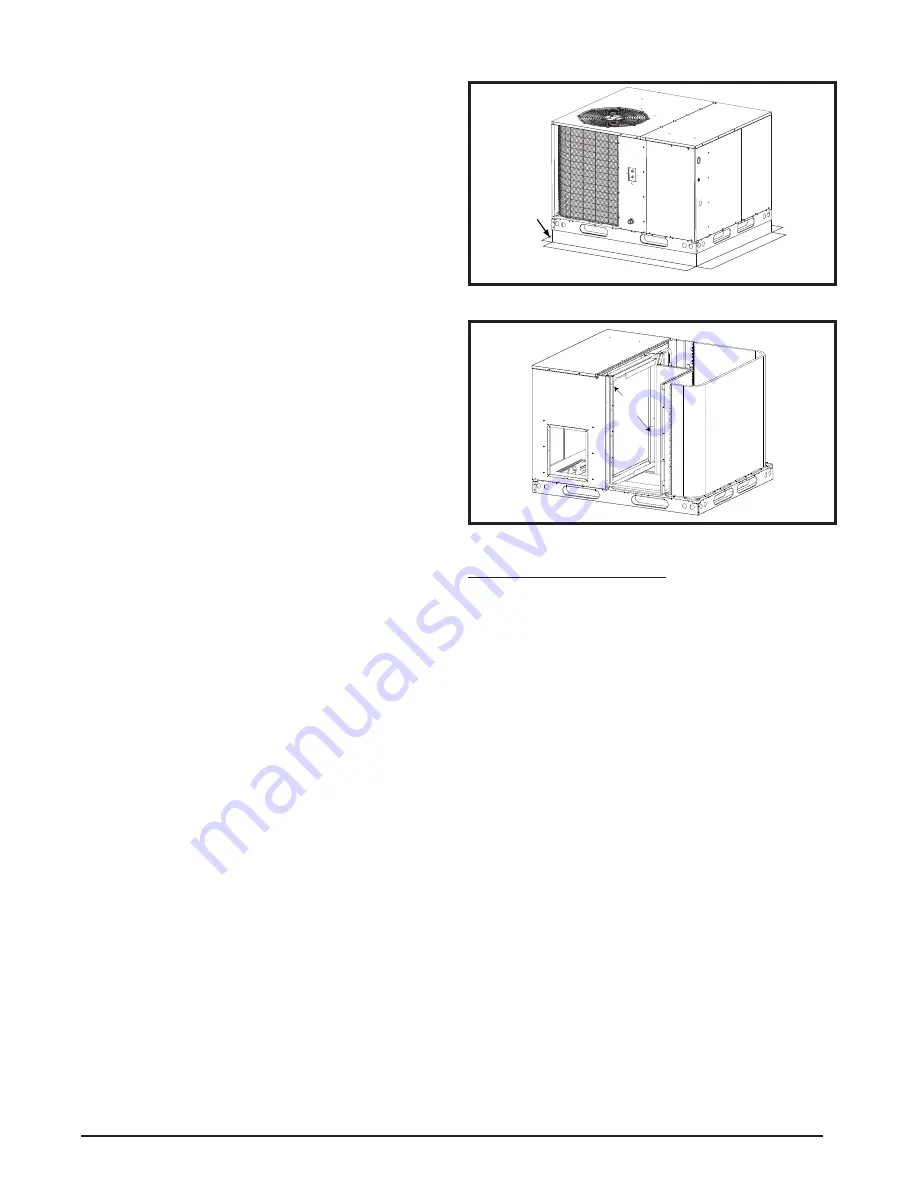
9
• Units require horizontal roof curb and return air kit for
horizontal installations.
• Ductwork should be attached directly to flanges on
panels supplied in horizontal duct conversion kits.
rooftop
Rooftop installations must be located according to local
building codes or ordinances and these requirements:
• The roof must be capable of handling the weight of the
unit. For unit weights, see
Table 5 (page 15)
. Reinforce
the roof if necessary.
• The appropriate accessory roof curb (
Figure 4
) must be
installed prior to unit installation. The roof curb must be
square and level to ensure proper condensate drainage.
Please follow all instructions provided with the kit
.
• Secure roof curb or frame to roof using acceptable
mechanical methods per local codes.
notE:
Make sure
the two supports beneath the unit have been removed.
removal of internal Filter rack
(3 Phase Only)
1. Remove the return air panel from the unit.
2. Remove the height adjustment screw from the inside
of the rack.
3. Remove (1) screw securing the assembly to the coil
located on the left leg of the rack.
notE:
The assembly
can now be easily collapsed and removed from the unit.
See
Figure 5
for filter rack securing screw locations.
removal of internal Filter rack
notE:
If a downflow economizer is installed, an internal
filter kit is not required, the economizer already has a filter.
1. Remove the return air panel from the unit.
2. Remove the height adjustment screw from the inside
of the rack.
3. Remove 4 screws securing the assembly to the coil
located on the left leg of the rack.
notE:
The assembly
can now be easily collapsed and removed from the
unit. The bracket secured to the top rear of the coil can
remain in place. See Figure 5 for filter rack securing
screw locations.
installing Filters in the internal Filter rack
(If Equipped)
1. Remove access panel screws from return air panel.
(
Hint:
Loosen the unit’s top panel screws near the
top edge of the access panel. The access panel was
designed to fit underneath the top panel.)
2. Slide the first filter between both guide channels of filter
rack and allow the filter to drop easily into place.
3. Verify the bottom of the filter is within the channels of
the rack.
4. Slide the 2nd filter (and 3rd filter on taller models)
between both guide channels of filter rack.
5. Verify the top of the filter is within the channels of the
rack.
6. Replace access cover by sliding the top edge of panel
under the lip of the unit’s top panel. Secure access
panel by replacing the screws.
Roof
Curb
Figure 4. roof top installation
Securing
Screws
Figure 5. internal Filter rack location
1” to 2” Filter Conversion
Factory installed internal filter rack (3 phase models only)
is set up to accept 1” filters. If conversion to 2” filters
is desired, remove the two (or three) 1” filter adaptors
secured in the assembly with clips by pulling straight off
the frame. The filter bracket must be reoriented to accept
2” filters by removing two screws securing it to the hinge
and rotating 180 degrees. See Figure 5.
removing Filters from internal Filter rack
(If Equipped)
1. Remove access panel screws from return air panel. (Hint:
Loosen the unit’s top panel screws near the top edge
of the access panel. The access panel was designed
to fit underneath the top panel.)
2. Remove upper filter by gently pulling filter through the
access panel opening.
3. Remove lower filter by lifting media to top of filter rack.
Remove in the same manner as described in step 2.
4. Install new filter in the filter rack as described in the
previous section.
Horizontal to Downflow conversion
The unit is shipped ready for horizontal duct connections.
If down flow ducts are required, the unit must be converted
following the steps below for the supply and return ducts.
1. Locate the duct cap inside the duct openings and remove
the screw holding it in place.
2. Lift the cap out of the unit. (
Hint:
The cap can be pushed
up from the bottom by reaching through the fork slot).
3. Cover the horizontal duct opening with the horizontal
duct cap. The insulation will be on the indoor side.
4. Fasten the cover with screws to seal.