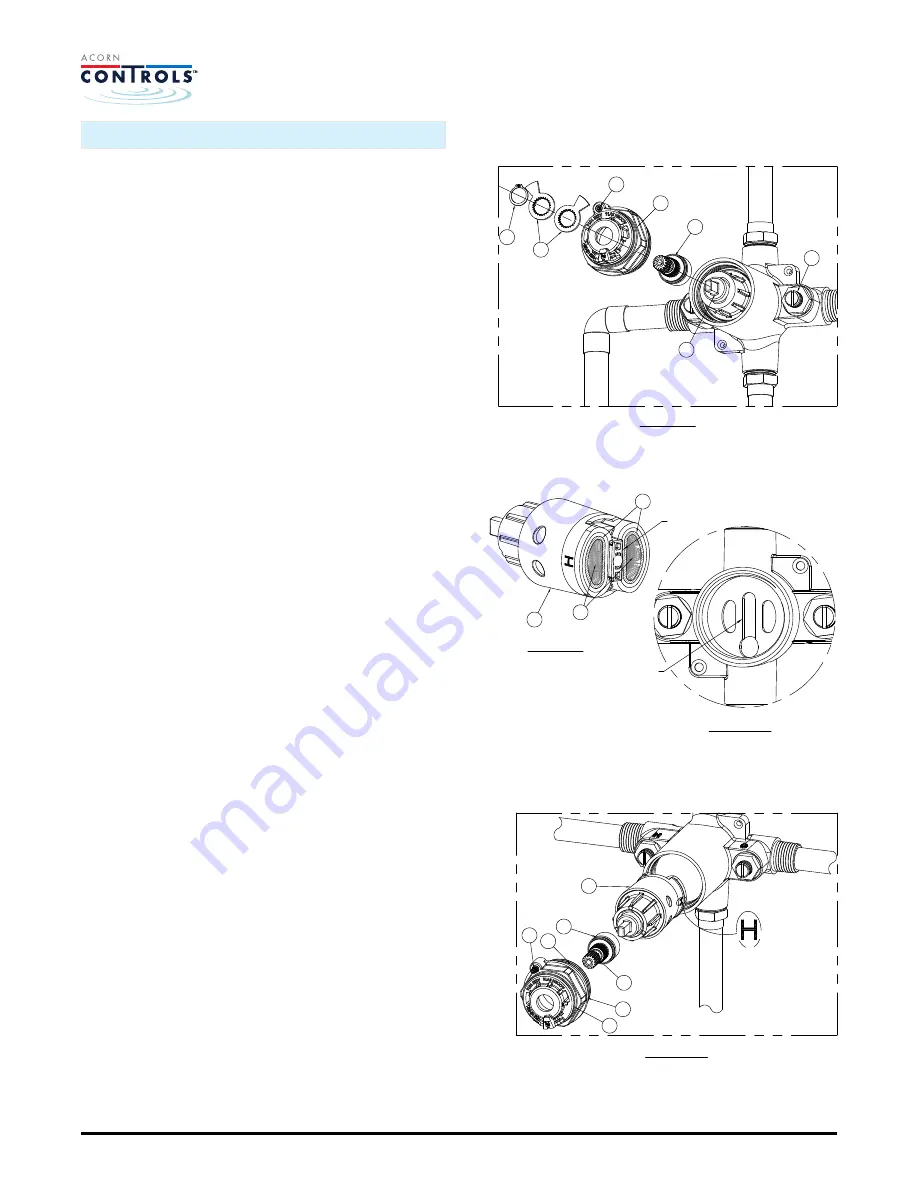
Page 6 of 9
1.
Bonnet Removal:
Figure
8
.
a. Close Checkstops
16
.
b. Using snap-ring pliers with pins less than 0.03”,
by others, remove snap-ring
17
.
c. Remove both temperature limit washers
18
.
d. Loosen 1/16” hex set screw
19
.
e. Unscrew bonnet
20
.
f. Remove external valve stem
21
g. Pull cartridge
22
out.
2.
Cartridge Reversal and Reassembly:
a. Inspect valve cartridge
22
ensuring that 'D'
shaped grooves have cartridge screen O-rings
23
in them and that stainless steel screens
24
are seated. See
Figure 8.
b. Insert cartridge
22
into valve body. Ensure the 'H'
(see detail) on the side of cartridge housing is on
the cold water supply side of valve casting.
This is so when the
cartridge is installed, it seats in the valve casting
and cartridge will not rotate. See
Figures 9 and
10
.
c. With valve stem O-ring
25
assembled onto valve
stem
21
, slide valve stem
21
onto cartridge stem
while holding in place. See
Figure 11
.
d. Inspect valve bonnet set screw
19
and ensure it
is in the backed out position. Slide bonnet O-ring
26
over threaded area on bonnet
20
and seat in
groove. See
Figure 11
.
NOTE:
For optional
Lever Handle, slide O-ring
26
into groove on the
top of
bonnet
20
.
e. Thread valve bonnet
20
into valve casting
turning clockwise. Apply pressure on top of stem
while screwing valve bonnet
20
into place. This
will keep cartridge from slipping out of slot while
bonnet is threaded into place. Tighten valve
bonnet
20
onto valve body firmly (180 In-Lbs).
Tighten set screw
19
with 1/16” Allen wrench
firmly (75 In Oz). This will prevent valve bonnet
20
from coming loose during use. See
Figure 11.
Take
note of the rib on the bottom of cartridge
22
(between the screens) and the slot in the bottom
of valve body are aligned.
CARTRIDGE REMOVAL:
Acorn Controls
Division of Acorn Engineering Company
®
, A member of Morris Group International
™
Manual #7802-116-000
SV16 Installation & Operation Manual
FIGURE 8
22
FIGURE 11
VIEW FROM REVERSED SIDE
HOT
COLD
17
18
19
21
16
22
20
22
FIGURE 10
24
23
25
21
20
19
FIGURE 9
26
25
SLOT
RIB
Date: 09/01/16
Summary of Contents for Controls SV16-LVR
Page 10: ......