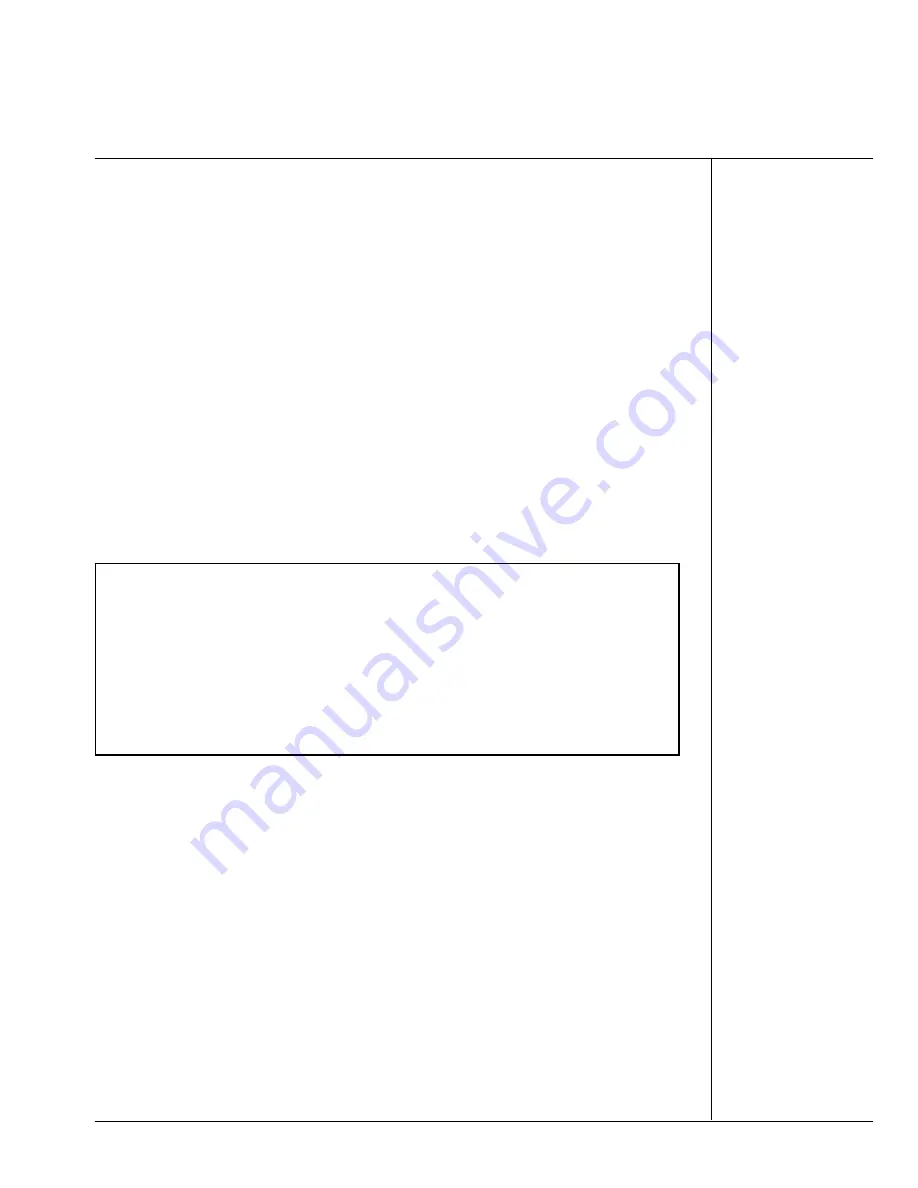
INSTALLATION AND OPERATION
Before Installing
Plan the installation in such a way as to allow a strainer to be coupled directly to the inlet of the
flowmeter. Where this is not possible, any piping between these units should be thoroughly cleaned
out.
Be careful to allow room for easy removal of the strainer screen.
An air release or other effective means must be provided in the metering system to prevent air
from entering the flowmeter. If an air release is used, the unit should be installed in a position as
close as possible to the inlet of the flowmeter. This will ensure the removal of the greatest possible
amount of air from the liquid before metering.
The vent line from the air release should be
3
⁄
4
″
pipe or
1
⁄
2
″
inside diameter tubing. Care should
be taken to prevent any possible obstruction to the free flow of air in this line. This line should vent
into the supply tank or into a container (5 gallons or larger) to collect possible liquid spewed with the
air.
Use pipe tape or cement on male threads only.
The piping on the outlet side of the flowmeter should be so arranged as to eliminate the possi-
bility of draining the measuring chamber.
A bypass connection should not be installed around the flowmeter. Experience has shown that
the valve in this line will eventually leak, work open or be accidentally left open.
WARNING
When Installing
The connecting piping should be firmly secured to prevent strain on the flowmeter casing.
Care should be taken that there is provision for expansion due to change in temperature.
All piping on the inlet side of the flowmeter should be very thoroughly cleaned out. Whenever
possible, place a spool in the place of the flowmeter and flush out all lines thoroughly before the
flowmeter is installed.
The majority of service calls on new installations would be eliminated
if these directions were followed.
Inlet and/or outlet are marked on flowmeter; do not install backwards.
After Installing
Pass sufficient liquid to clear the lines of air. Check the rate of flow. It should not exceed the
rated capacity of the flowmeter. The bypass of the pump should be regulated to deliver the maximum
practical rate of flow for the least amount of pressure. Pressure on the flowmeter should not exceed
125 psi. Do not try to increase the flow through undersized pipes and fittings by means of excessive
pressures which will cause leaking gaskets and collapsed air release floats.
Temperature of the liquid should not exceed 140
°
F.
All flowmeters are tested and calibrated by Actaris and adjustment should not be necessary. If
registration appears to be in error, the flowmeter registration should be checked using a calibrated
volumetric prover.
The prover must be of sufficient capacity to permit a full flow delivery for at
least one minute.
Do not base calibration upon assumed volume of ordinary containers or “dip
stick” measurement.
If the registration is not in agreement refer to the section on “Calibration.”
Cleaning The Strainer
While the installation is still new, the strainer, if used, should be cleaned very frequently. After
the system has been thoroughly flushed of foreign material, only periodic maintenance of the unit is
recommended.
INSTALLATION AND
OPERATION
Before Installing
When Installing
After Installing
Cleaning The Strainer
Page 1
Summary of Contents for RED SEAL MEASUREMENT neptune
Page 18: ...Page 16 ...
Page 19: ...Page 17 ...