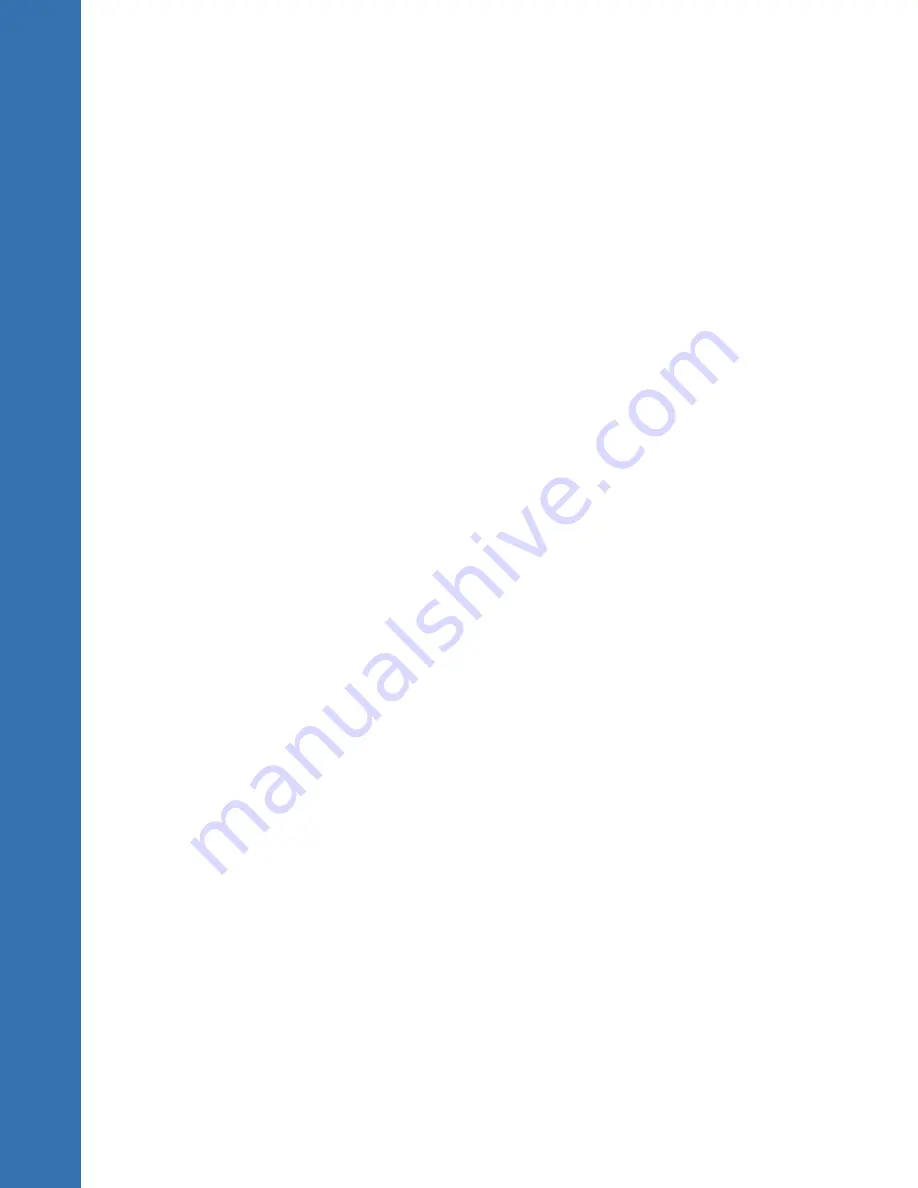
22
V
I.
M
IS
C
EL
L
AN
E
O
U
S
Changing Products
Different types of TyrFil
®
can be pumped interchangeably through the same equipment. If
the material is changed over prior to pump start-up, follow normal start-up procedures after
changing totes/drums. If during processing, use the following procedure to change from one
product to the other:
1. Drain Hoses - The clear supply hoses connecting totes or drums to the pump contain more
than a gallon of usable material. To avoid wasting this, open the drum valves, tilt each drum back
to an approximate 45-degree angle, and lift the supply hoses to drain as much of the unused
material as possible back into the drums. For totes, run approximately 6-8 strokes into a scrap
container to clear the hoses.
2. Change Drums - Close drum valves and small drum closures on old material, disconnect
supply hoses and temporarily hang them, open-end-up, on the pump. Move old drums aside
using drum racks. Immediately clean up any material spilled when disconnecting or
reconnecting supply hoses.
3. Position totes or drums - Correctly position the new material and connect to supply hoses.
4. Cycle Machine - Place fluid gun over waste container and cycle machine until old material
flowing from gun is clearly replaced by new material (approximately six to eight strokes).
5. Continue Processing - Begin processing as before, using new material. Although different
types of TyrFil
®
can be used without problem in the same equipment, if you run out of one
product during processing never add a different product to the same tire. Poor tire performance
will result. Tote sets and drum kits do not always empty identically. However, they should empty
at approximately the same rates. Avoid allowing air from an empty container to be pumped into
the system. Change to full totes or drums before the old ones are completely empty.
Cross Contamination
Cross contamination occurs when the “ISO” and “CAT” side hoses are accidentally switched
and connected to the opposite side. This can happen when switching empty totes/drums or
changing from one product to another. Unfortunately, when this happens, it is not usually
realized until it is too late. In most cases you will need to replace the lower cylinder unit,
material supply hoses, line gauges, pressure gauge, and manifold hoses. If this mistake is
realized before the pump is operated, it can be simply corrected by reconnecting the supply
hoses to their proper sides.
On-Site Flatproofing
Accella Tire Fill Systems does not recommend on-site flatproofing, however for reasons of
convenience and efficiency, it can be done if:
1. The site can meet the 72° F (22° C) temperature requirements for storing the material,
pumping the material and curing the processed tires.