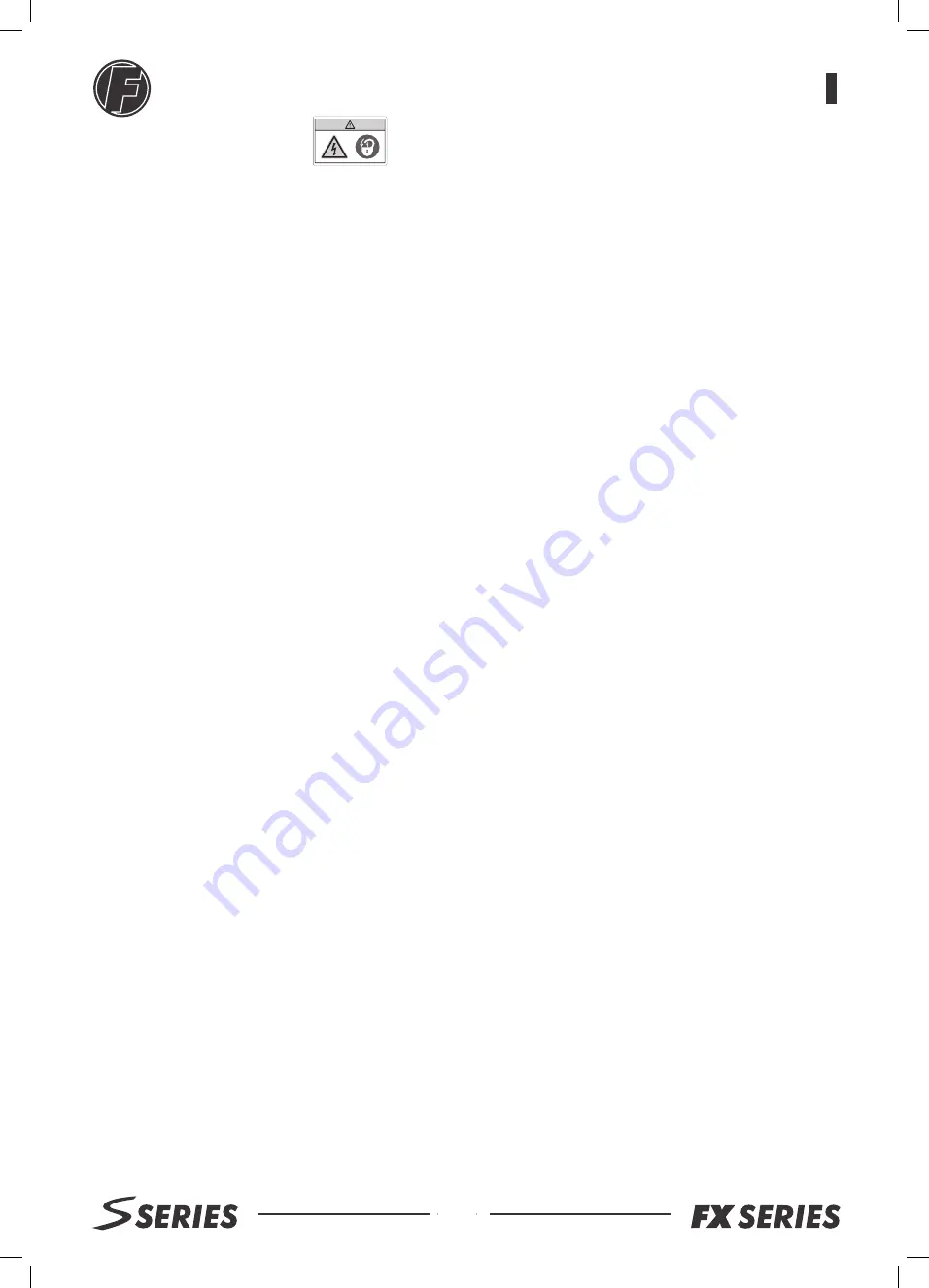
5
Safety Information
Isolation from any power supply shall either be visible (visible break in the power supply circuits) or the isolation
device is actuated to the off position and physically locked off.
The unit must not be operated without the case fitted.
At least
seconds must be allowed for the inner drum to stop rotating before the case is removed.
Oil leaks can be a hazard. The complete Filtermist system should be checked regularly for possible oil leaks.
Daily visual checks of both unit and extraction duct are recommended.
Contact with oils, coolants etc. can cause skin disorders. Avoid contact with skin and eyes and wear PVC,
neo prene or nitrile gloves, safety glasses and overalls when cleaning or working on the filter.
The unit to be used on wet applications only, e.g. Oil, emulsion, coolant or steam.
The unit is not to be used on flammable, explosive, corrosive or dry applications, e.g dust, smoke, acid.
The unit is intended for indoor use only.
Daily visual checks of both unit and extraction duct are recommended.
Ensure that the recommended schedules of checks, as detailed in the accompanying Log Book, are followed.
General Information
Filtermist units remove and separate contaminants by centrifugal impaction, forcing aerosols to coalesce into
larger droplets and removing them from the airstream. High levels of filtration and constant efficiency make this
method of separation ideal for machining applications using coolants.
Recovered oil can be returned to the machine tool or a separate container, whilst the cleaned air is exhausted
back into the work area. Collection of contaminated air should be as close as possible to its source so installation
of a Filtermist unit will usually be directly on, or very close to, the machine tool, simplifying any installation
requirements.
Filtermist unit are available in a comprehensive range of air volumes suitable for a wide range of machine tools.
Some simple guidelines need to be followed to ensure trouble free installation of each unit.
• On enclosed machine applications, the extraction point should be positioned as far as practically possible
from the cutting area of the machine. This will prevent oil droplets being drawn up into the unit and possibly
overloading the unit. It will also prevent swarf being drawn into the inlet grille which over time will cause a
reduction in air flow and therefore extraction.
• The extraction point should also be positioned so that mist is drawn away from the operators working area.
Installation Information
Summary of Contents for Filtermist FX Series
Page 21: ...21 21 Local Exhaust Ventilation LOG BOOK...
Page 24: ...24 Daily Log Sheet s t n e m m o C d e n g i S S S F T W T M k e e W Daily Log Sheet...
Page 25: ...25 Daily Log Sheet s t n e m m o C d e n g i S S S F T W T M k e e W Daily Log Sheet...
Page 26: ...26 Daily Log Sheet s t n e m m o C d e n g i S S S F T W T M k e e W Daily Log Sheet...
Page 27: ...27 Daily Log Sheet s t n e m m o C d e n g i S S S F T W T M k e e W Daily Log Sheet...
Page 28: ...28 Daily Log Sheet s t n e m m o C d e n g i S S S F T W T M k e e W Daily Log Sheet...