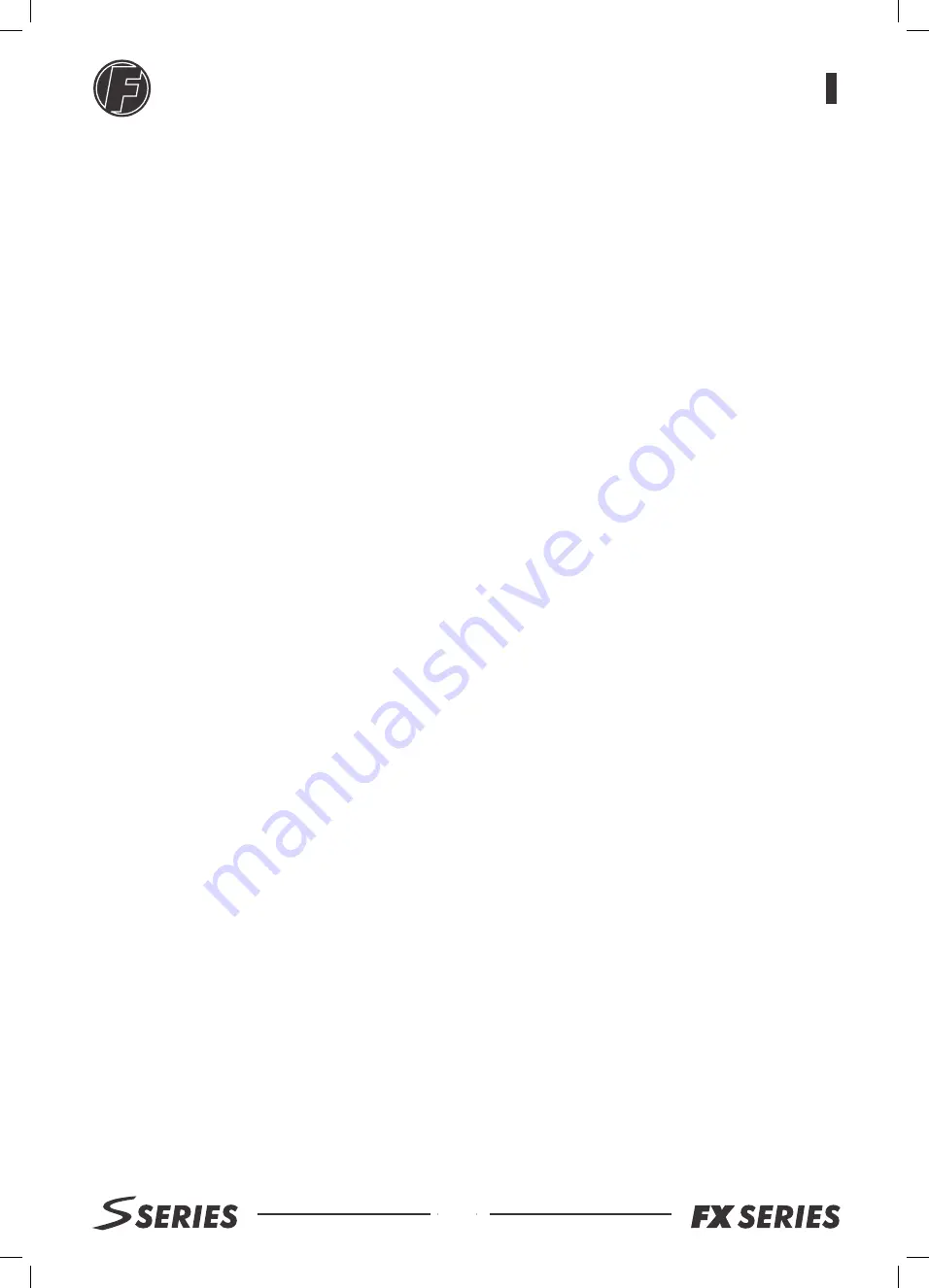
3
Filtermist as an LEV System
Filtermist units are designed for the control of aerosol mists, namely those generated by machining operations
that use either soluble or neat oil coolants. Other applications include component washing machines and EDM
machines. Due to the aggressive nature of the fluid, it is recommended that only stainless-steel versions are used
on component washing machine applications.
Filtermist units are NOT designed to work on welding fume or dry dust applications. Please contact the Filtermist
Technical Support Department (01952 290500) if further advice is required regarding the suitability of any
application.
Filtermist units are designed for use with the majority of machine tools, both enclosed and open, and offer high
levels of filtration with minimal service requirements. Enclosed machines are covered by changing the air within
the enclosure between 6 and 10 times per minute, depending on application, whilst ensuring gaps within the
enclosure are kept under a negative pressure. Open machines are usually covered by hoods positioned to capture
and extract mists generated by the machining process.
Generally a capture velocity between 30 – 45 m/min is needed at the source of the contaminant. Typical
installations are described later in this manual. Bespoke installations are also available.
Operation
Filtermist units are specifically designed to separate aerosol particles, usually oil mist, from the air, including oil
and coolant mist and steam generated in parts washing process. A perforated steel drum, open at one end, is
directly driven by a 3-phase electric motor. Four vanes within the drum generate suction which draws aerosols
into the drum. Here the aerosols are impacted by the vanes at velocities in excess of 50 metres per second. The
aerosol particles are forced to collide and coalesce before being driven by centrifugal force against the inner
surface of the units casing. A drainage point ensures that the liquid is drained away under pressure. Cleaned air
is returned to the workshop.
Four pads are fitted between the drum vanes to minimise noise levels and prevent the possibility of liquid
fragmentation. As the drum speed is constant, the separation phase of the process remains constant ensuring
high levels of filtration are maintained.
Efficiency
Aerosol particles are generally considered to be in the 0.2 – 5.0 micron range. Within this range are particles
which provide a potential hazard to health. Particles above 3.5 micron are usually filtered out by the natural
filters in the human system. Particles of 0.3 micron and below are thought to be exhaled.
This leaves an important range of particles that can be retained within the body and which should be removed
from the air before they are inhaled
Filtermist units provide high filtration efficiencies across this critical range. Efficiencies of 98% have been shown
in independent tests carried out on typical oil mist applications.
Greater efficiencies can be achieved using a high-efficiency secondary filter (afterfilter) on the exhaust side of the
unit. UK customers have an afterfilter supplied as additional standard equipment along with each unit (excluding
those units to be used on parts washing machines).
General Information
Summary of Contents for Filtermist FX Series
Page 21: ...21 21 Local Exhaust Ventilation LOG BOOK...
Page 24: ...24 Daily Log Sheet s t n e m m o C d e n g i S S S F T W T M k e e W Daily Log Sheet...
Page 25: ...25 Daily Log Sheet s t n e m m o C d e n g i S S S F T W T M k e e W Daily Log Sheet...
Page 26: ...26 Daily Log Sheet s t n e m m o C d e n g i S S S F T W T M k e e W Daily Log Sheet...
Page 27: ...27 Daily Log Sheet s t n e m m o C d e n g i S S S F T W T M k e e W Daily Log Sheet...
Page 28: ...28 Daily Log Sheet s t n e m m o C d e n g i S S S F T W T M k e e W Daily Log Sheet...