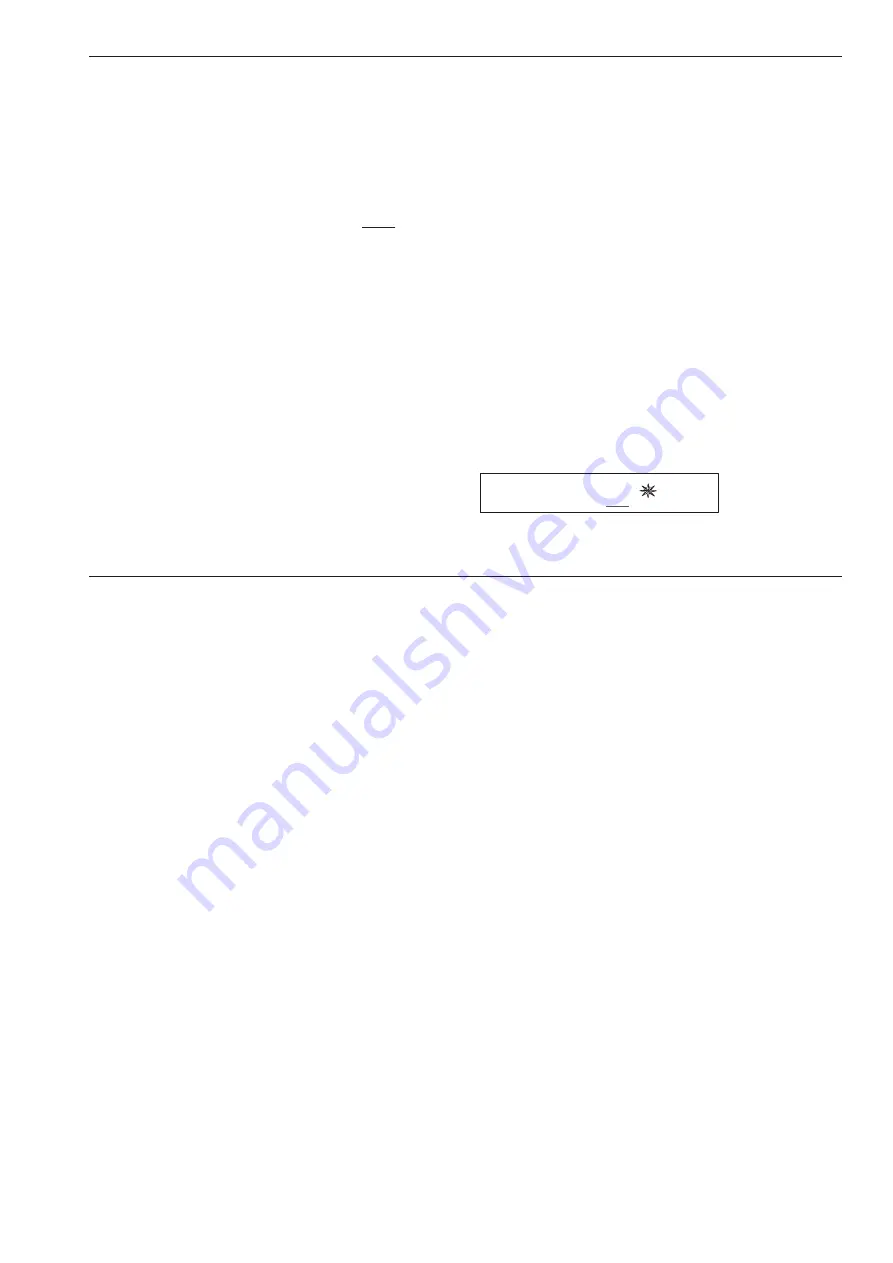
ElektroPhysik
E-13
4.1.3 Deplating speed control (SPEED)
Position the cursor to SPEED (14) by pressing SET-key
and use ARROW-keys for your de-plating speed
selection. The de-plating speed is indicated in steps of
50% (ARROW-DOWN-key) or 100% (ARROW-UP key).
In general, the de-plating speed should be selected so
that a measuring time between one and three minutes
can always be ensured.
The de-plating speed ranges between 0.3 microns/min
at minimum and 40 microns/min at maximum. When try-
ing to set higher or lower, the message “MAXIMUM” or
“MINIMUM” appears.
The de-plating speed indication on the reading display
(2) is more accurate than on the alpha-numerical dis-
play (3). The corresponding measuring unit microns or
mils are displayed on the alpha-numerical display.
To reset to default de-plating speed press CLEAR-key
(10). This default value depends on the metal selection.
Note:
The de-plating speed also depends on the range of
source of electricity powering the instruments.
For special applications the de-plating speed is limited.
The de-plating speed for Chrome in combination with
the measuring area B, for instance, must not exceed 40
microns/min. The message “MAXIMUM” may occur.
4.1.4 Sensitivity (SENS)
Position the cursor to SENS (13) by pressing SET-key.
The current sensitivity is shown on the reading display
(2) and the voltage being displayed alphanumerically.
Use the ARROW-keys for sensitivity control. Press
CLEAR-key to reset to default sensitivity selection.
If the required sensitivity is equal to the default sensitiv-
ity, there willl be an empty space above the cursor.
Ni B 5,4
µm
METAL
AREA
SPEED
SENS
CAL
UNIT