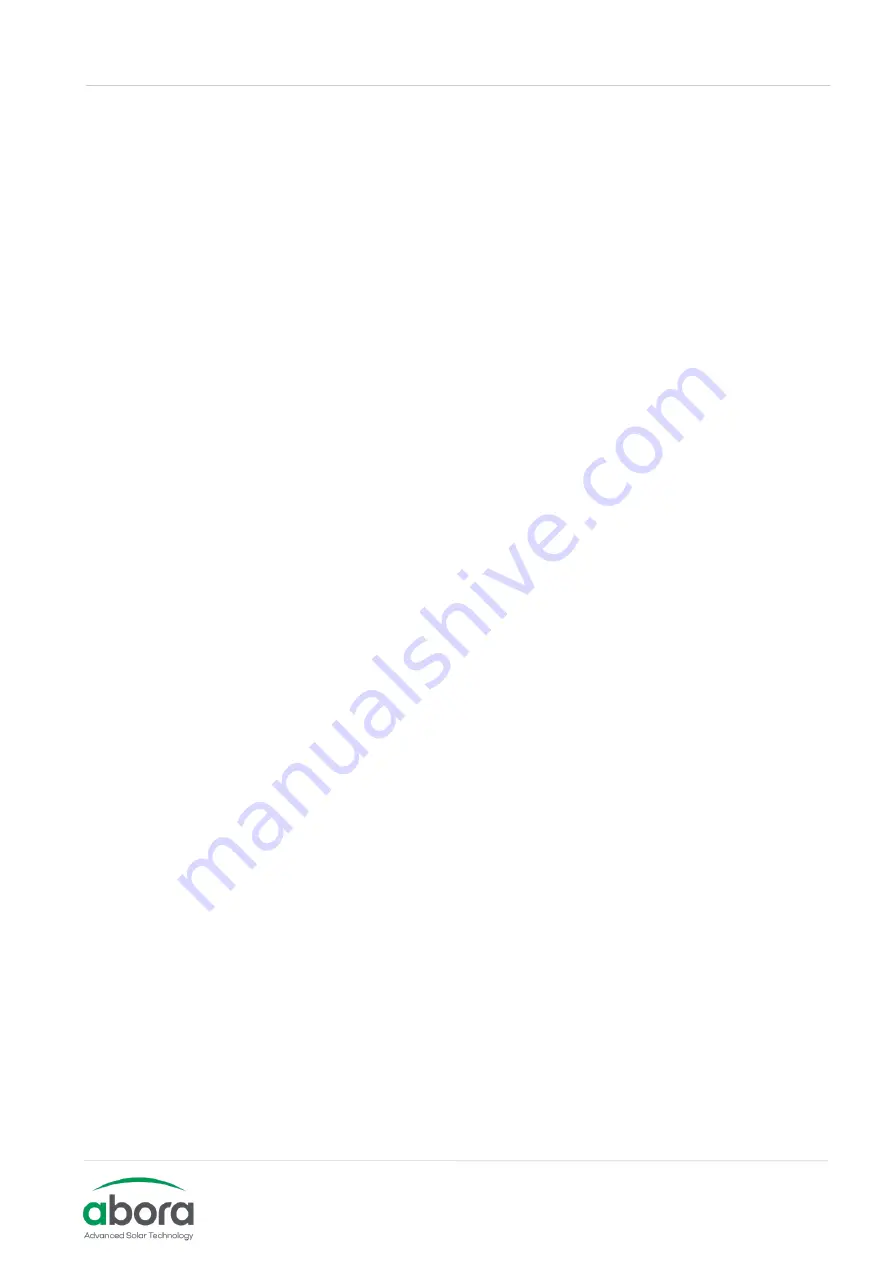
PANEL HANDBOOK aH72 SK
V 6.0
18
/ 31
4.8.1
Cleaning and filling the system
Once the installation is completed, it will be cleaned and filled.
4.8.2
Leakage check of the collector field
To avoid problems with faulty connections or possible pores, the first test for tightness should be
carried out, using water or air. The air allows to retouch the welds without waiting time. This test will
be carried out at high pressures (close to the maximum admissible ones for the collectors and pipes),
making sure not to have connected the components of the installation whose maximum working
pressure is lower than the one used for the test, i.e. expansion vessel, pumping system, air separator,
etc.
4.8.3
Calibration of the expansion vessel
The expansion vessel must be capable of absorbing the fluid expansion that occurs in moments of
stagnation with the consequent risk of overheating. Generally, expansion vessels are set at a higher
pressure in the factory than the actual working pressure, so it will be necessary to adapt it to the needs
of each installation. In the first instance, the circuit pressure must have been calculated. The expansion
vessel must be calibrated at a pressure equal to the initial pressure of the system without operation.
It is important to remember that the content of the expansion tank is nitrogen, since inside it contains
a membrane with metal parts that would oxidize with oxygen.
It is essential to have a pressure gauge to carry out this check.
All specifications of the expansion vessel manufacturer must be followed.
4.8.4
Cleaning, filling and tightness testing
It is advisable to clean the whole installation in an open circuit with water in order to eliminate possible
remains of welds that would obstruct the passage of the fluid in addition to altering its properties. In
installations with bleeding valves in the upper part and a single filling point in the lower part, it is not
possible to carry out this type of cleaning.
Initially, the primary circuit will be filled with a pressure 1.5 times higher than the working pressure,
which will be reduced later. It is very important that the filling phase is carried out with little solar
radiation (at the first or last hour of the day) since, when the primary pump is stopped, the stagnant
fluid could reach high temperatures and evaporate, forming air pockets in the installation and causing
problems in the circulation and filling. The panels will be covered.
Due to the capacity of glycol to penetrate into fine grooves, due to its lower surface tension compared
to water, it is necessary to make a new tightness test, this time with the heat transfer fluid.