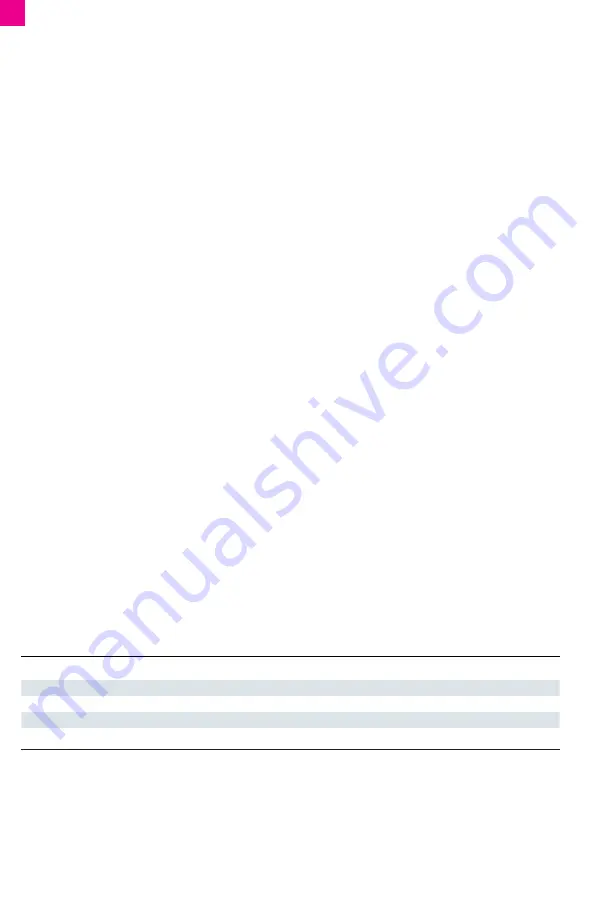
6
STEP 7: EWR Initialization (Cont.)
Setting the Gas Flow
Begin with the default setting (yellow LED displayed at 14) and complete weld. If the weld is
not acceptable due to porosity, unstable arc, etc., continue to Troubleshooting. If the weld is
acceptable, continue with the following procedure:
■
Press the minus (-) button once and repeat.
■
Continue with this process, moving towards a schedule with less flow, until the weld
exhibits excessive spatter, instability, and/or porosity.
■
At this point, press the plus (+) button once.
■
Complete another weld and verify that this setting is acceptable. If so, move on to Step 8.
Troubleshooting
■
Press the plus button (+) once and repeat the weld. If the weld is acceptable, this
procedure is completed and you can move on to Step 8.
■
If the weld still is not acceptable, repeat the procedure until an acceptable weld is
achieved, then move on to Step 8.
STEP 8: Setting the Gas Flow Pressure
What is this Adjustment?
The gas pressure between the EWR and the closed magnetic valve in the power source or
feeder can be adjusted. This adjustment is necessary if you have longer cable assemblies or
other circumstances which might affect a proper gas flow. The factory default setting is 0.6bar
(8.7 PSI) outgoing pressure. The pressure can be changed from 0.2bar – 2.0bar (2.9 PSI –
29 PSI).
BINZEL Recommendations for MIG/MAG
Length of Cable Assembly
Recommended RMA Gas Flow Pressures
Under 8m (26 feet)
0.4 - 0.6bar (5.8 - 8.7 PSI)
9 - 18m (29 - 59 feet)
0.8 - 1.0bar (11.6 -14.5 PSI)
19 40m (62 - 131 feet)
1.2 - 1.4bar (17.4 - 20.3 PSI)
Longer than 41m (134 feet)
1.6 - 2.0bar (23.2 - 29 PSI)