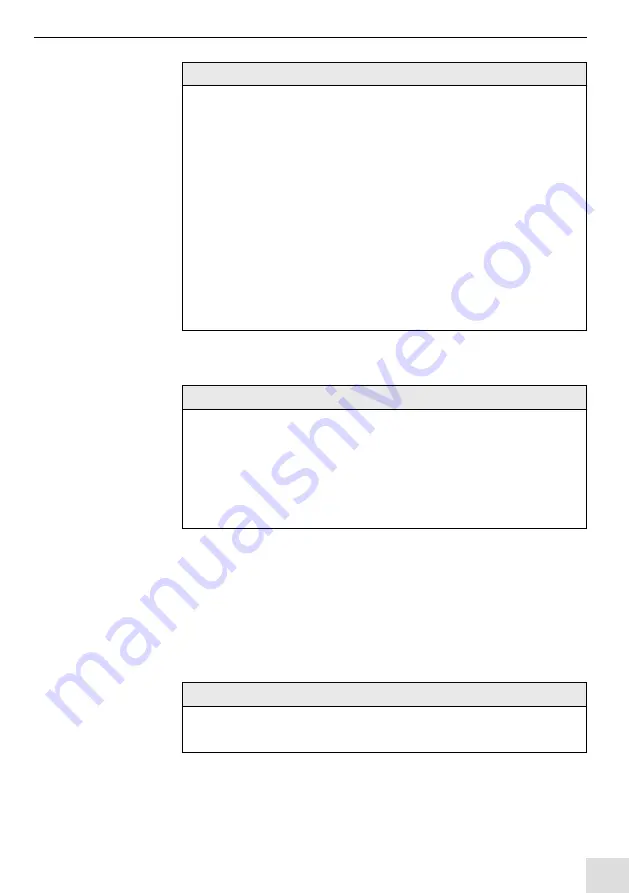
EN - 7
Welding torch ERGO
5 Handle operating elements
4.4 Setting the shielding gas volume
4.5 Feeding in wire
1
Insert the wire into the wire feed unit as specified by the manufacturer.
2
Press the ‘zero-current wire feed’ trigger on the wire feed unit until the wire
emerges from the contact tip.
5 Handle operating elements
The trigger’s two-cycle mode can be activated when using a standard welding
torch. Further operating modes and handle modules depend on the
corresponding welding power source and must be ordered separately.
NOTICE
• Check the minimum fill level on the cooling unit.
• Ensure that the coolant supply and return hoses have been correctly
installed. Coolant supply = blue, coolant return = red.
• Do not use deionised or demineralised water as coolant or for leak and
flow tests. This may shorten your welding torch’s service life.
• For liquid-cooled welding torches, we recommend using
ABICOR BINZEL
BTC coolant.
• The cooling system must be purged of any air each time the device is
commissioned and after every cable assembly change: disconnect the
coolant return hose from the coolant recirculator and hold it over a
collection receptacle. Close the opening on the coolant return hose then
re-open it by abruptly releasing it. Repeat until the coolant flows into the
collection receptacle continuously and without air bubbles.
NOTICE
• The type and amount of shielding gas used depend on the welding task
and the gas nozzle geometry.
• Make all shielding gas connections gas-tight.
• To prevent the shielding gas supply from becoming clogged by
impurities, the cylinder valve must be opened briefly before connecting
the cylinder. This will expel any impurities that may be present.
NOTICE
• Please also consult the operating instructions for the welding
components, e.g. the welding power source.