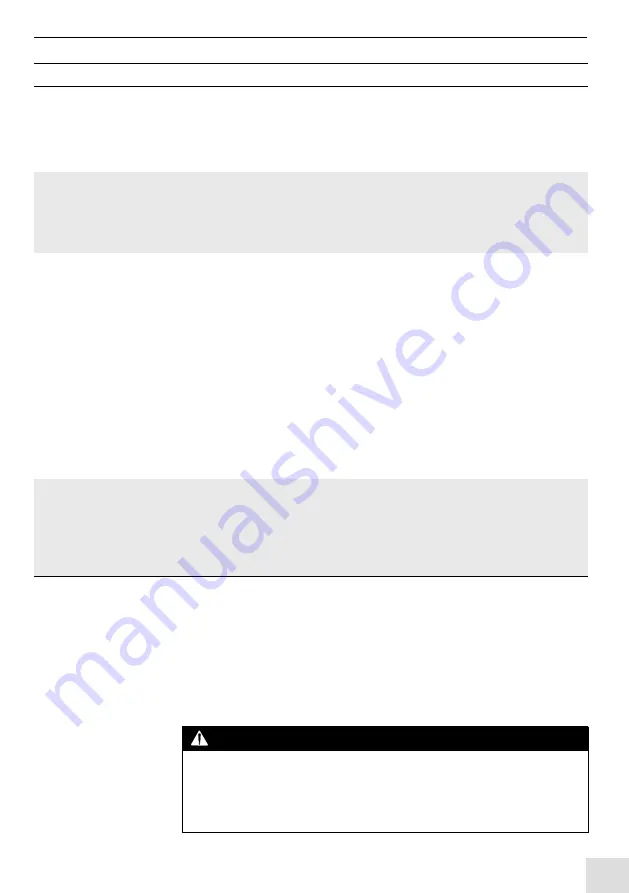
EN - 23
ABIPLAS
®
CUT
11 Dismounting
11 Dismounting
Dismounting may only be carried out by specialised personnel. Please make
sure that the shutdown procedures are strictly observed before the dismounting
is started. Make sure to include also the components integrated into the
welding system.
Cutting arc breaks
• Cutting rate too low
• Torch standoff distance too high
• Material thickness too high
• Output too low
• Increase cutting rate
• Reduce torch standoff distance
• Use lower material thickness.
• Adjust output
Excess dross formation
• Cutting rate too low or too high
• Equipment parts worn or
damaged
• Output not adjusted
• Adjust cutting rate
• Replace equipment parts
• Adjust output
Cutting nozzle burned
out
• Damaged or loose nozzle
• Contact with work-piece
• Start of cut at edge of work-piece
too fast
• Too much spatter when punching
holes
• Pilot arc struck too long and too
frequently in air
• Pilot arc too strong (depending on
power source)
• Tighten nozzle or protection cap
hand-tight, or replace nozzle, if
necessary
• Avoid contact
• Start cut at a lower rate
•
• Shorten/avoid ignitions in air if
possible
• Set pilot arc current to lowest
possible value
Strong electrode burn-out • Pressure drop while cutting due to
incorrectly set pressure monitor
• Loose electrode
• Pilot arc struck too long and too
frequently in air
• Correct pressure monitor setting
• Tighten electrode by hand
• Shorten/avoid ignitions in air if
possible
Fault
Cause
Solution
Tab. 11
Troubleshooting
DANGER
Risk of injury due to unexpected start-up.
For the entire duration of maintenance, servicing, dismounting and repair
work, the following instructions must be adhered to:
• Switch off the entire welding system.
Summary of Contents for abiplas cut
Page 27: ...DE 27 ABIPLAS CUT 12 Entsorgung ...
Page 51: ...EN 25 ABIPLAS CUT 12 Disposal ...
Page 77: ...FR 27 ABIPLAS CUT 12 Elimination ...
Page 103: ...ES 27 ABIPLAS CUT 12 Eliminación ...