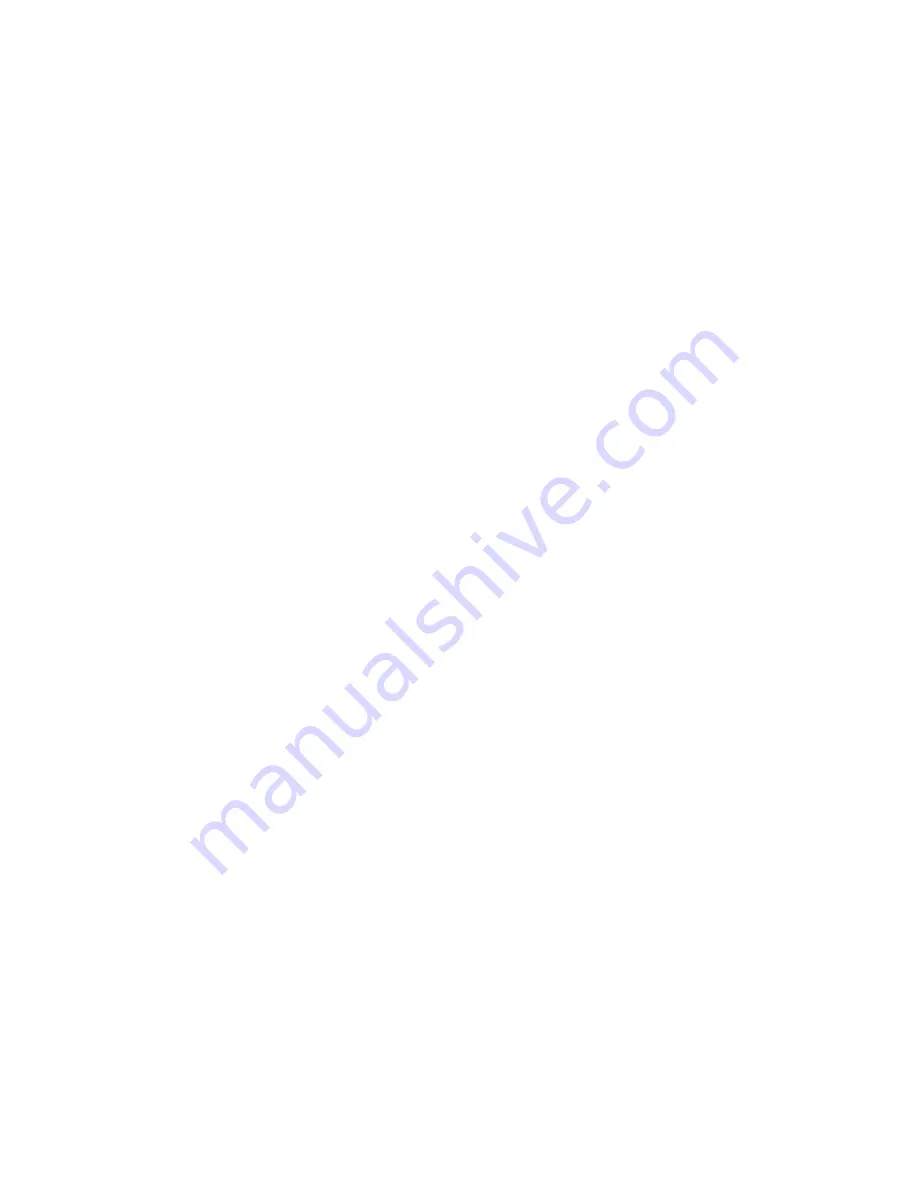
6 - Phaser Pure Water System Operation and Maintenance Manual
1. Strong bypass flow is normal during system operation.
This water is the discharge water and it contains a very
high TDS. This water is non-potable but is also not
harmful to plants. DO NOT DRINK DISCHARGE WATER.
3. Milky white bypass flow is a common occurrence when
starting up the system or using a new RO membrane. It is
trapped air being pushed out of the filter housing and will
stop once the air is gone.
Water Coming Out Of Discharge Hose
1. With the source water off, check that the fitting is
properly tightened. Tighten until you feel the gasket
engage. DO NOT OVER TIGHTEN
2. Unscrew the leaky connection. Check gasket in the
female fitting for damage or deformation. Replace
gasket if necessary.
Leak Between Brass Garden Hose Fittings
1. Unscrew leaky brass fitting.
2. Check brass fittings for damage or deformation.
If necessary replace brass fittings. Replacement parts
can be ordered from ABC or bought from a local store.
The plastic hole size is ½” national pipe thread (NPT)
and the Brass fitting connection are a standard
¾” Garden hose thread (GHT).
3. Fittings should be attached with an adhesive to
prevent leaks. We recommend Liquid Nails Perfect
Glue from Home Depot.
4. If leak persists replace filter.
Leak Between Brass Garden Hose Fitting And
Plastic Housing
of biological fouling. After long term storage, running a
series of long flushes will often return the RO membrane
to normal production levels. Fully open the bypass hose
and then shut off your system’s pure water outlet at the
DI filter. Run it like this for 10 minutes and then open your
pure water outlet and restrict your bypass to its normal
running setting. Doing this flushing process 2 or 3 times
may be required to return to normal production levels.
4. Expect decreased production rates when running your
RO with colder source water. The ideal temperature for
source water is 77°F. You can expect around half the flow
for water at 50 degrees that you would get at 75 degrees,
even if both sources are at the same PSI. Use your TDS
meter to measure the temperature of your source water
to determine if this is the cause of lowered flow rates.
5. Leaks in the system and the pole tubing can release
pressure and take flow away from the jets in your brush.
A couple of small leaks in the pure water lines can cut
pressure to the jets in half. Read the “leaks” section
below for more information on eliminating leaks in the
system.
1. Retest your water sample. When you get a higher than
expected reading on your handheld TDS meter, it is a
good idea to use the water you are testing to wash out
both the measuring lid and the measuring prongs of the
meter itself. Do not get the body of the meter wet, it is
not waterproof. Minerals can stay in the cup from other
measurements and can make the sample appear to
have a higher TDS than it actually does. Taking multiple
samples ensures maximum accuracy.
2. High TDS coming out of the system usually indicates
that the DI filter is spent. Testing before and after the
DI filter will verify that there is not another issue. If the
TDS levels before and after the DI filter are the same, the
filter is completely depleted. Replace the DI filter (P/N
WF2CDI-6) once depleted. If water coming from the RO
filter has high TDS levels, check the RO performance as
well.
3. Elevated TDS levels coming from the RO membrane
can indicate that both the RO and DI need to be
replaced. First, remove the DI filter from the end of the
RO filter. Use your handheld TDS meter to measure the
TDS water coming out of the RO and compare that to the
TDS levels of the source water. Your RO should have a
rejection rate of over 80%. If the rejection rates are below
normal, follow the step below to ensure that the RO filter
needs to be replaced.
High TDS
4. If your RO rejection is lower than expected, you can
try running a 10 minute flush. Increasing flow through the
filter housing will help the flushing process. Fully open the
bypass hose and then shut off your system’s pure water
outlet at the DI filter. Run it like this for 10 minutes and
then open your pure water outlet and restrict your bypass
to its normal running setting. Check your RO TDS to see
if it is dropping to more acceptable levels. Repeat the
forward flush 2-3 times if necessary to drop the RO TDS.
5. If you RO TDS does not drop, your RO is probably
faulty. You can continue to use the faulty RO, however you
will use up your DI resin faster than normal. Replace the
faulty RO filter (P/N WF2CRO-40) as soon as possible.
13. Leaks