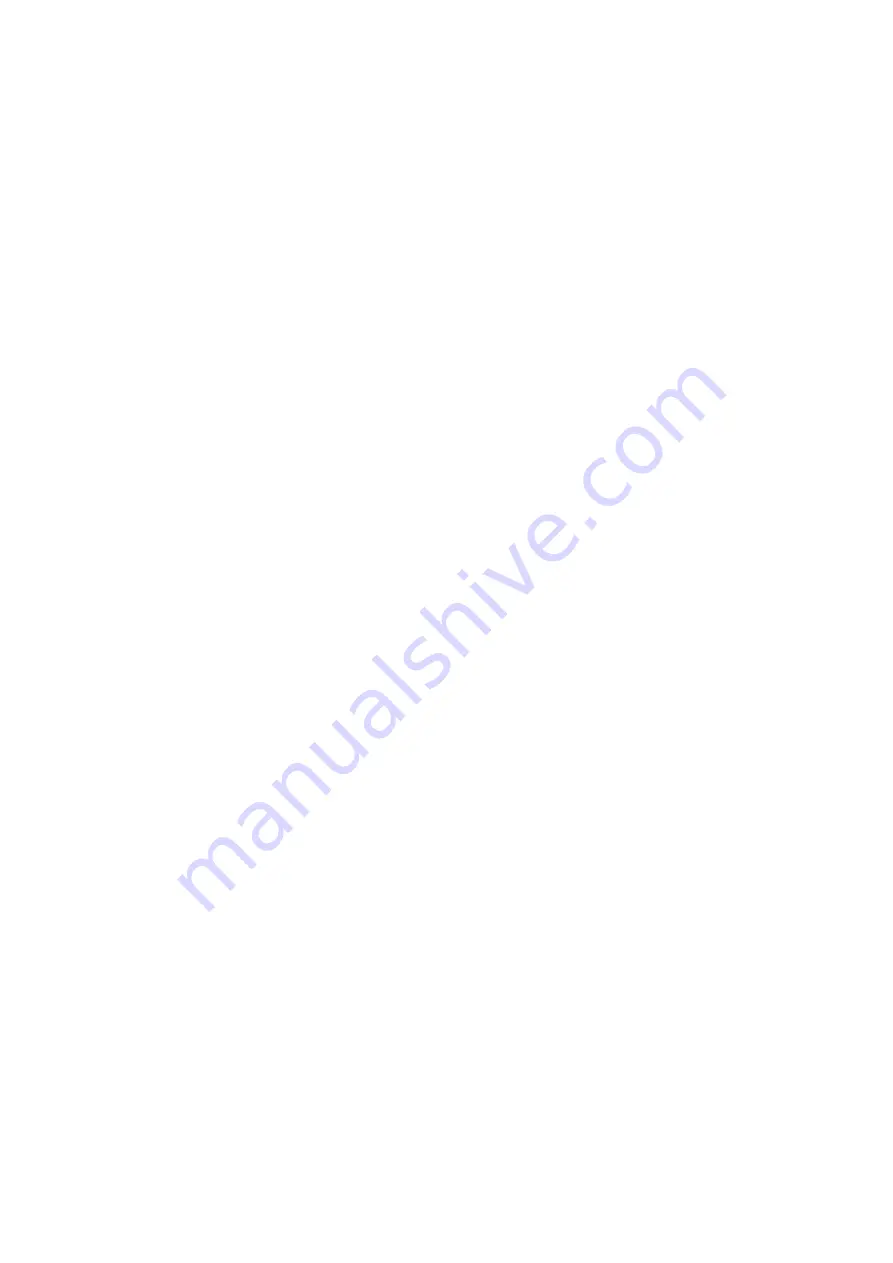
16
VM1
- INSTRUCTION MANUAL BA 504/05 E
Where appropriate in individual cases, further
information can be found in the technical
documentation appurtenant to the switchgear
system (e.g. agreed special operating
conditions) in addition to this operating
manual.
7.2 Inspection and functional
testing
7.2.1 Circuit breaker in general
•
Under normal operating conditions, inspection
within the stated number of operating cycles is
not necessary.
•
Inspection may be necessary under exceptional
operating conditions (including adverse climatic
conditions) and/or particular environmental
stresses (e.g. serious contamination and
aggressive air).
•
The inspection primarily comprises visual
examination for contamination, corrosion,
moisture and discharge phenomena on the high
voltage side.
If an irregular condition is found, appropriate
maintenance work is to be initiated.
•
No external discharge may occur on the surfaces
of equipment at operating voltage. This can, for
example, be detected by characteristic noises, a
clearly perceptible smell of ozone, or visible
glowing in the dark.
•
If irregular conditions are detected, then
corresponding repair measures should be
initiated.
7.2.2 Magnetic actuator operating mechanism
(Figures 9/17 and 9/26)
A first functional test of the operating mechanism
is to be performed:
•
after the stated number of operating cycles, or
•
during maintenance work as described in section
7.2.1.
Before the functional test, open the circuit
breaker and
•
move it into the test position (withdrawable
breaker) or
•
isolate and secure the working area in accordance
with the Safety Regulations to DIN VDE / IEC (with
stationary mounted breakers).
•
Observe the procedure for capacitor discharge as
set down in section 7.1.
•
Perform visual examination of the condition
(removing front plate 1.1), e.g.:
- the lubrication at the rotary bearings,
- the operating cycle counter,
- the sensor mounting,
- the position indicator.
Scope of functional testing:
•
Connect the supply voltage.
•
Perform several switching operations under no
load. This is predominantly applicable to circuit-
breakers which are rarely operated under normal
circumstances.
To check the storage capacitor, switch the
circuit breaker rapidly OFF-ON-OFF once,
pressing push-buttons 3 and 4 rapidly in
succession.
•
The LEDs on the inductive proximity switches 15
and 16 are activated when the circuit breaker has
reached its OFF and ON limit positions.
7.2.3 Withdrawable part
•
The inspection should always include a visual
examination of the withdrawable part assembly.
Special attention is to be paid to those parts
which may possibly be damaged by improper
handling.
•
Perform a visual check on the condition of the
isolating contact system. It is recommended that
the contact system be turned alternately so that
its inner contact points can be cleaned.
If there are signs of impermissible overheating
(discoloured surface), the contact points are to
be cleaned (see the section on repairs).
•
The interlock conditions and the ease of
movement of the withdrawable assembly are to be
checked as described under “Repair”.
When checking the interlock conditions, it is
essential toensure that no force is used.
Maximum torque 25 Nm!
7.3 Servicing
7.3.1 Circuit breaker in general
If the necessity of cleaning is established during
inspections as described in 7.2.1, the following
procedure is to be adopted:
•
Prior to cleaning, isolate and secure the working
area if necessary in accordance with the safety
regulations of DIN VDE and IEC.
•
Observe the procedure for capacitor discharge as
set down in section 7.1.
•
Cleaning of surfaces in general:
- Remove weakly adhering dry dust deposits with
a soft dry cloth.
- Remove more strongly adhering dirt with a
slightly alkaline household cleanser, or with
Rivolta BWR 210.
•
Cleaning of insulating material surfaces and
conductive parts:
- Minor contamination: with Rivolta BWR 210.
- Strongly adhering contamination: with cold
cleanser 716
—
7. Maintenance
Summary of Contents for VM1
Page 51: ...MEDIUM VOLTAGE PRODUCTS 51 51...