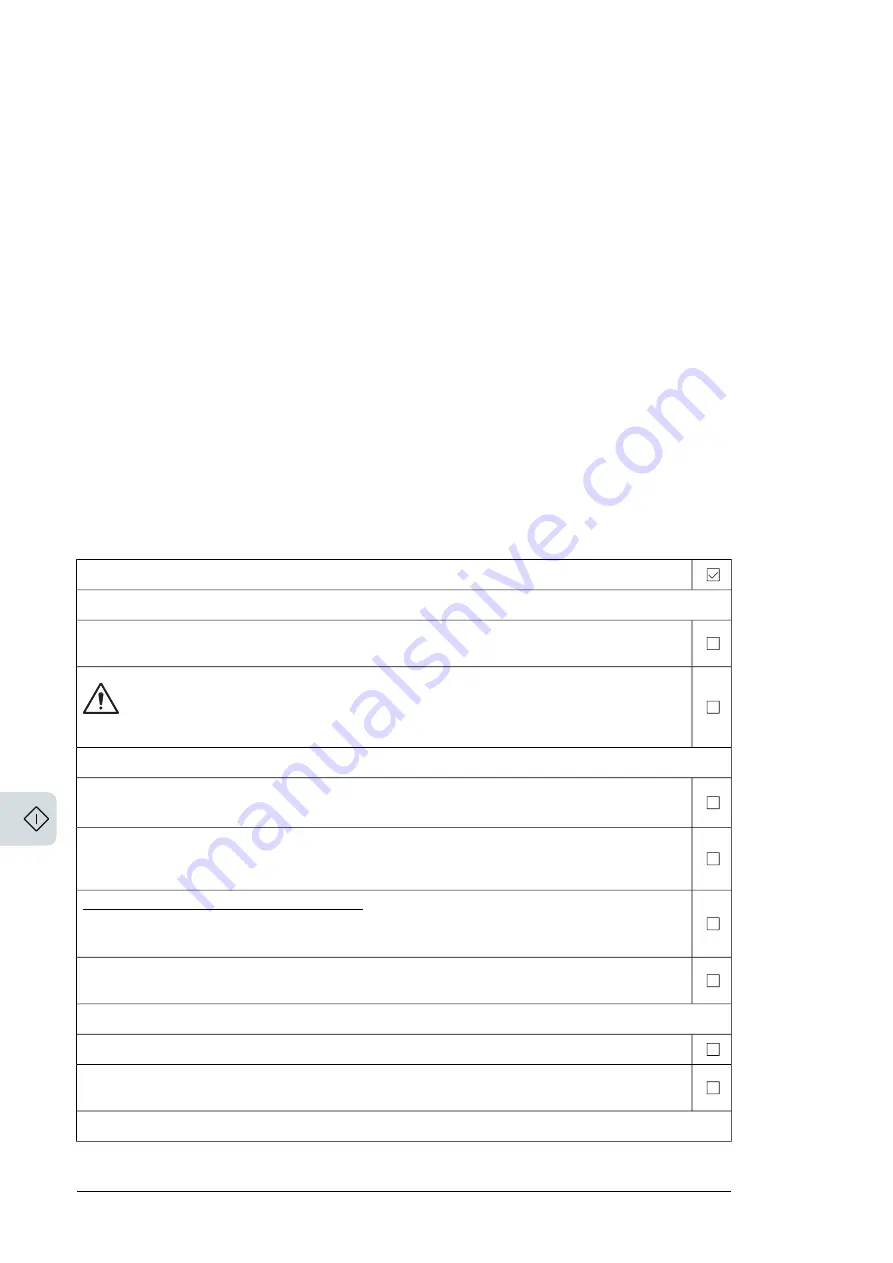
•
you must sign and store the acceptance test report for further reference.
■
Acceptance test reports
You must store the signed acceptance test reports in the logbook of the machine. The report
must include, as required by the referred standards:
•
a description of the safety application (including a figure)
•
a description and revisions of safety components that are used in the safety application
•
a list of all safety functions that are used in the safety application
•
a list of all safety-related parameters and their values
•
documentation of start-up activities, references to failure reports and resolution of failures
•
the test results for each safety function, checksums, date of the tests, and confirmation
by the test personnel.
You must store any new acceptance test reports performed due to changes or maintenance
in the logbook of the machine.
Start-up and acceptance test
You need the Drive composer PC tool or a control panel to perform the start-up and
acceptance test.
Action
Initial status
Make sure that the drive is ready for use, that is, you have done the tasks of the drive start-up procedure.
See the hardware manual.
WARNING!
Obey the safety instructions. If you ignore them, injury or death, or damage to the equipment
can occur.
Checks and settings with no voltage connected
Stop the drive and do the steps in section
Electrical safety precautions (page 8)
before you start the
work.
If you have done any connections for the emergency stop circuit on site (such as wiring of additional
emergency stop buttons, connection of shipping splits of large drives, etc.), check the connections
against the appropriate circuit diagrams.
Inverter units with parallel R8i inverter modules:
Check that the XSTO.OUT output on the inverter control unit [A41] is chained to the STO inputs of all
inverter modules.
Check that the hardware settings relevant to the safety function are set as defined in section Hardware
settings.
Settings with voltage connected
Close the cabinet doors and power up the drive. See the hardware manual.
Check the parameters that are relevant to the safety function. If necessary, set the parameters as
defined in section Parameter settings.
Acceptance test
30 Start-up and acceptance test