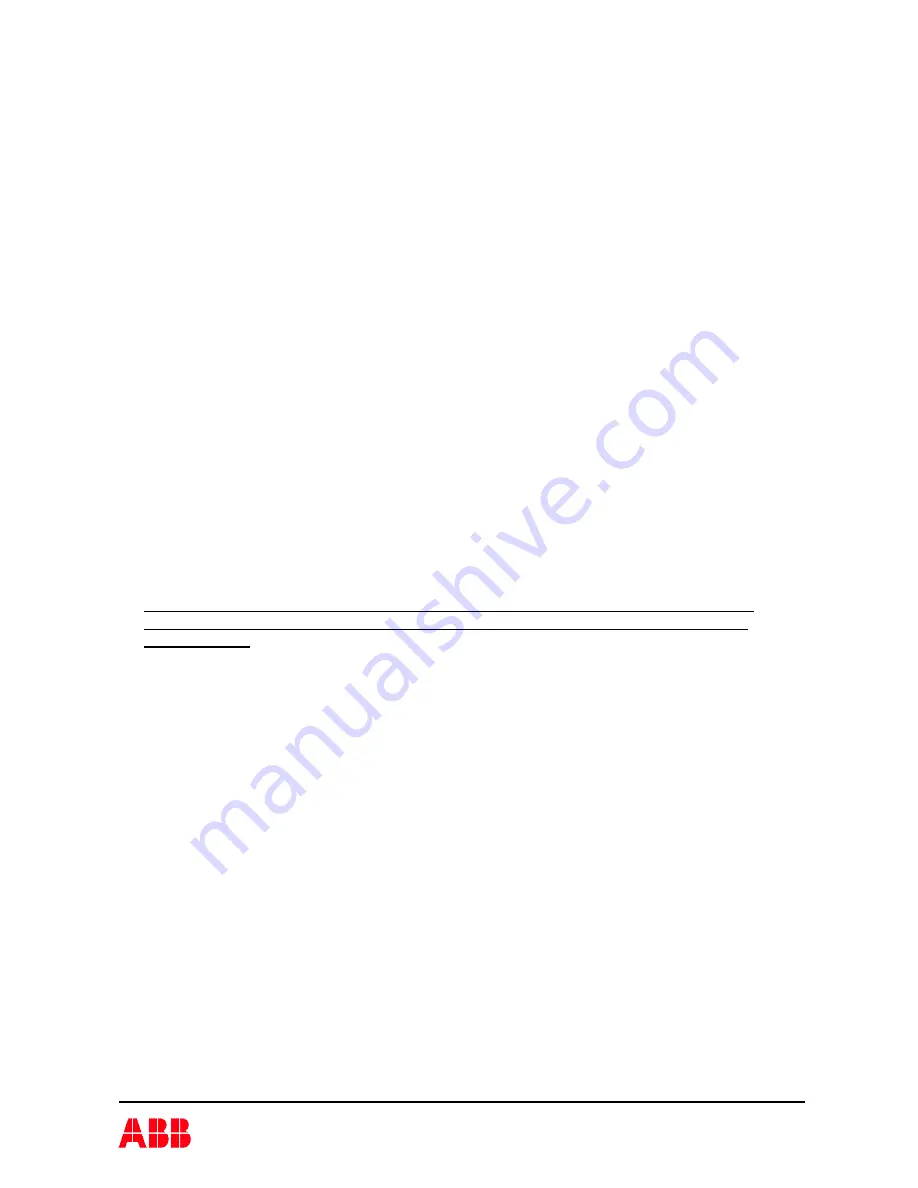
26
2TLC172001M0211_A
Pluto as Safe Input
This is the setting for a Pluto that is used as a safe input slave. A special function block,
“PlutoAsSafeInput”, is needed for the PLC program. Configuration of the safe input and non-
safe outputs are the same as for the ordinary “Safe input” slave. Pluto can handle up to 16
“PlutoAsSafeInput” + “SafeOutput“ slaves.
4.6.4 Modes of operation
Pluto has three modes of operation on the AS-i bus:
Bus Master
Pluto controls the AS-i bus. Via the PLC program Pluto can read the inputs and set the outputs
of the slaves.
Monitor only
In this case Pluto only listens to the bus traffic, which is controlled by an external master.
Normally this external master is a non-safety PLC system for control of the non safety related
part of the application.
In monitor mode Pluto can read all I/O:s on the AS-i bus but not set any outputs since it is the
external master that controls the bus.
Monitor / Slave
This mode is the same as “Monitor only” mode but Pluto can also be a slave node under the
external master. Pluto and the external master can then communicate with each other, 4 bits in
each direction.
AS-i profile: S-7.F
4.6.5 Exchange of Safety slaves after commissioning
The system allows exchange of a safety slave without any tool for modification of the PLC
program or other setup.
The requirement is that all slaves, except the one that shall be replaced, are working and
connected to the AS-i bus. It is also necessary that the IDFIX is of type “IDFIX-DATA” or
“IDFIX-PROG”.
Some AS-i units contain two AS-i addresses/slaves. For these units it is necessary to first set
these two addresses to the same two addresses as in the unit it shall replace. The address can
be set either with a programming tool or through Pluto Manager (Tools/AS-i/Change AS-i slave
address).
The procedure is as follows:
- Press “K” button for 2 seconds.
- If one safety slave is missing the display flashes “CC” -> “[slave number]”.
- Press the “K” button one more time to acknowledge and the display will show steady “CC”.
- The new safety slave can now be connected and the display will show “CF” (Code found).
(If the same slave is connected again the display will show “Cd” (Code Duplicate), which
means that the code is already stored in Plutos memory.)
- By pressing “K” a last time, Pluto will automatically store the new code and reboot.
4.6.5.1 Exchange of non-safe slaves after commissioning
For exchange of a non-safe slave the requirement is that all slaves, except the one that shall
be replaced, are working and connected to the AS-i bus.
- Remove the slave which shall be replaced.
- Connect the new slave.