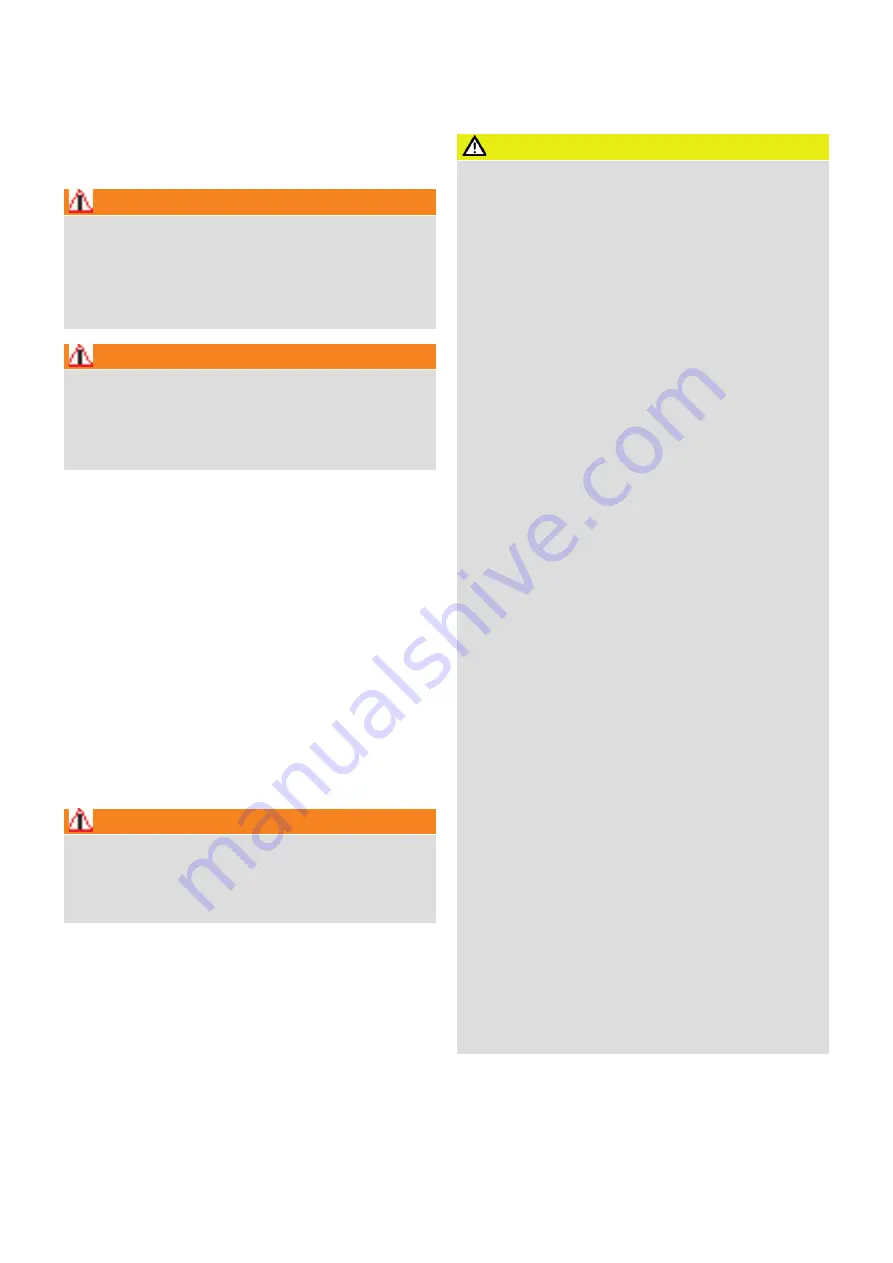
6
KM26 |
MAGNETIC LEVEL GAUGE | OI/KM26-EN REV I
Safety information for inspection and
maintenance
Corrective maintenance work may be performed only by
trained personnel.
• before removing the device, depressurize the device and
any adjacent lines or containers.
• check whether hazardous materials have been used as
measured materials before opening the device. Residual
amounts of hazardous substances may still be present in
the device and could escape when the device is open
• within the scope of operator responsibility, check the
following as part of a regular inspection:
– pressure-bearing wall / lining of the level device
– measurement-related function
– leak-tightness
– wear (corrosion)
Explosives atomspheres installation
For installation requirements in explosives atmospheres
applications refer to IEC 60079-14 and any local safety or
electric code regulations mandatory in your area.
. . . 2 Safety
Safety information for electrical
installation
Electrical connections may only be established by
authorized personnel in accordance with the electrical
circuit diagrams. The electrical connection information in
the manual must be observed; otherwise, the application
protection type may be affected. Ground the measurement
system according to requirements.
There is no EMC protection or protection against
accidental contact when the housing cover is open. There
are electric circuits within the housing which are
dangerous if touched. Therefore, the auxiliary power must
be switched off before opening the housing cover.
The device can be operated at high pressure and with
aggressive media. Any process media released may cause
severe injuries. Depressurize the pipeline / tank before
opening the transmitter connection.
WARNING
WARNING
WARNING
• for category II 1 G installation, parts of the equipment
shall be protected so that impact or friction sparks
cannot occur, taking into account rare malfunction.
Measures to prevent impact or friction sparks when
using the equipment include but are not limited to:
– limited mechanical agitation shall be used;
– use of stilling wells to mitigate effect of agitation.
– limit rate of change of level to values such that
friction sparks cannot occur, less than 1 m/s, at all
times.
– extra precaution should be taken during installation
and maintenance to prevent float from traveling
down / up chamber too fast while initially filling and
/ or pressurizing the vessel / chamber and likewise
while depressurizing and emptying vessel.
• the user shall take the appropriate mitigation
measures in accordance with their own risk
assessment to prevent any other conditions capable
of producing impact or friction sparks.
• if additional non-conductive paint / coatings are
applied to the process connection, flange or
instrument housing (for example to provide additional
corrosion resistance) there may exist a risk of
electrostatic discharge due to charge build-up on the
non-conductive paint / coating layer. The user shall
take the appropriate mitigation measures in
accordance with their own risk assessment.
• when non-metallic sensor well or probe sleeve
materials are used there is a risk of ignition from
electrostatic discharge due to the flow of non-
conductive media (for example in stirring vessels and
pipes). The user shall decide on the suitability of the
equipment for the particular application.
• the equipment temperature class rating, TX, cannot
exceed the auto-ignition temperature of the process
fluid contained within the chamber by a safety margin
and should take into account variations, fluctuations
and upset conditions of process fluid temperature
that may be encountered. The end user should
conduct their own risk assessment to prevent auto
ignition of its process fluid.
• the equipment and any ancillary equipment attached
shall be grounded using at least a 4 mm 2 cross
sectional area connection device onto non-painted
surface for good coupling / bonding.
• to help prevent a stuck float, keep process fluid debris
free and when warranted carry out cleaning of
chamber considering the type of process fluid in use.
These actions are the responsibility of the end user.
CAUTION