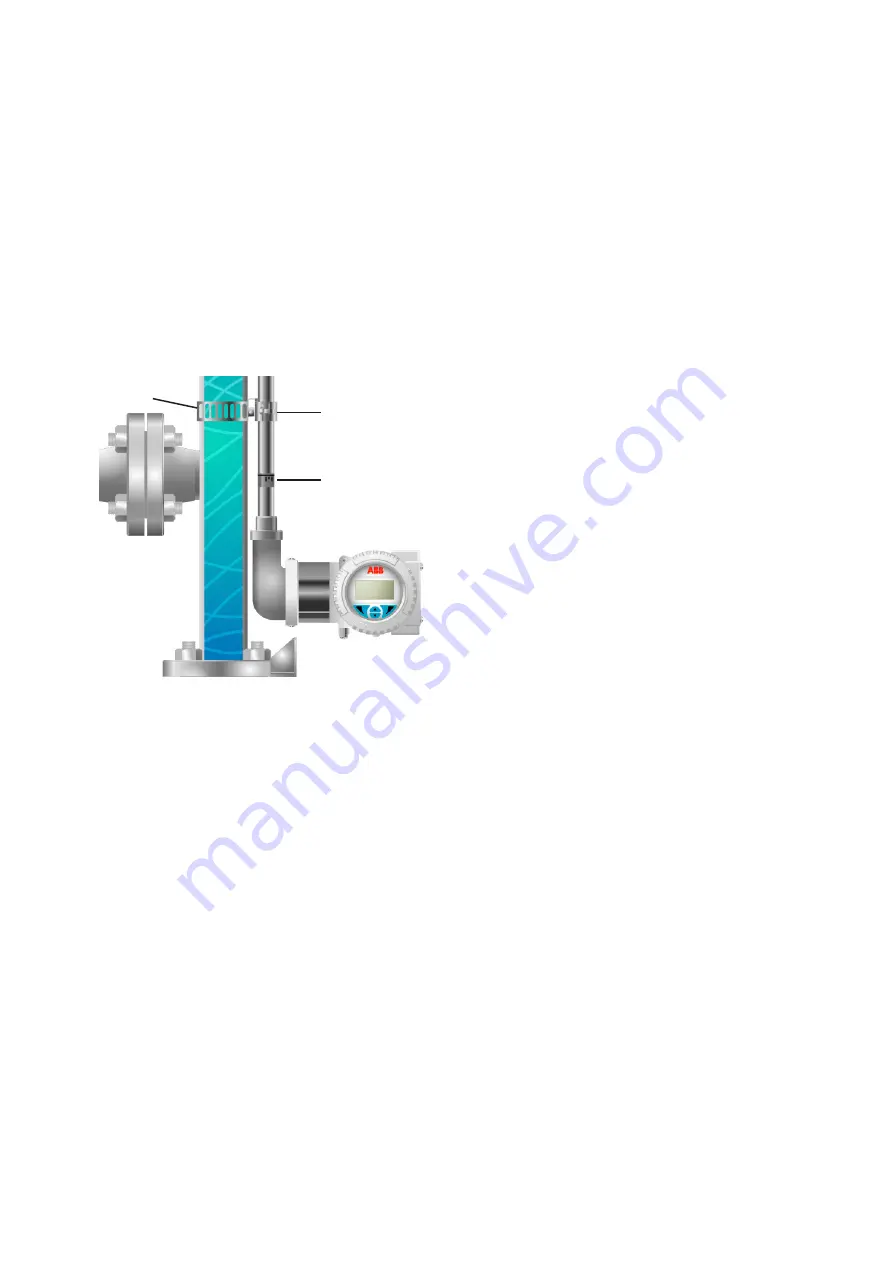
16
KM26 |
MAGNETIC LEVEL GAUGE | OI/KM26-EN REV I
Magnetostrictive transmitter installation
When mounting the LMT200 / AT200 level transmitter, the
following rules need to be applied to ensure proper
installation:
• if the LMT/AT series device was purchased with the KM26
magnetic level gauge (MLG), it will have been shipped
mounted and positioned and will not typically require any
further mechanical adjustment.
• the sensor tube is labeled with a factory zero mark. The
line on this tag should be aligned with the zero on the
scale of the level gauge.
. . . 3 Mounting
Factory zero
mark
Transmitter clamp
Figure 18- LMT200 mountings
Hose / gear
clamp
• The LMT electronic housing, in reference to the sensor
tube, is indicated by the model number:
– B1 or B2 – the housing is at the bottom of the sensor
tube
– T1 or T2 – the housing is at the top of the sensor tube
Please read all directions carefully before performing any
operations per the respective manuals of the transmitters.
Installation without insulation blanket or
pad
The following steps are recommended for the successful
installation a magnetostrictive level transmitter (MLT) on an
existing magnetic level gauge (MLG) which does not include
an insulation blanket or the transmitter does not include an
insulation pad:
1
identify the name tag of the transmitter and based upon
the model number determine the proper orientation of
the electronics housing.
2
compare the measuring length of the transmitter (the last
numbers in the model number) with the measuring length
of the MLG and the center to center dimension if the MLG
to determine if the transmitter should match the scale
measurement or the center to center of the process
connections.
3
identify the ‘factory zero mark’ sticker on the sensor tube
of the transmitter.
4
block the MLG from the process.
5
drain the MLG following plant procedures for pressure
relief and disposal of process fluids.
6
align the magnetostrictive transmitter with the MLG.
– if the transmitter measuring length matches the
measuring length of the gauge, align the zero mark
with the zero of the scale.
– if the transmitter measuring length matches the center
to center of the gauge, align the zero mark with the
center of the bottom process connection.
7
mark the MLG chamber where the mounting tabs of the
transmitter match up to the chamber. Also, place a mark
on the MLG chamber that corresponds to the mounting
tabs of any support bracket included with the transmitter.
8
set the transmitter down.
9
slightly loosen all but the uppermost worm gear clamps
which attach the scale assembly to the MLG.
10
open the worm gear clamps included with the
magnetostrictive transmitter and slide one clamp beneath
the scale assembly at each marked location on the MLG.
Tighten the clamps slightly to hold them in place.
Note
For transmitters with a measuring length longer than 7 feet
(2.1 meters), use a tape measure to determine the location of
mounting tabs on the transmitter and mark the MLG
accordingly.
11
realign the zero mark of the transmitter with the
corresponding zero on the MLG.
12
starting with the highest transmitter mounting clamp,
loosen each transmitter clamp, slide the clamp over or
through the mounting tab of the transmitter, and tighten
the clamp.
13
repeat step 12 until all transmitter mounting clamps are
tightened.
14
tighten all scale mounting clamps being sure to align the
scale vertically on the MLG.
15
to confirm the zero of the transmitter, apply power to the
terminal strip of the magnetostrictive transmitter. If the
transmitter reads higher than ‘zero’, raise the transmitter.
If the transmitter reads lower than ‘zero’, lower the
transmitter.
16
attach proper field wiring to the transmitter according to
the instruction manual, included with the transmitter.
17
open the process to the MLG using the procedure included
in the ‘isolation valves’ section.
Installation with insulation blanket
The following steps are recommended for the successful
installation a magnetostrictive level transmitter (MLT) on an
existing magnetic level gauge (MLG) which includes an
insulation blanket.
Follow steps 1-6 in the previous section and use the following
alternate steps:
7
mark the outside of the insulation blanket where the