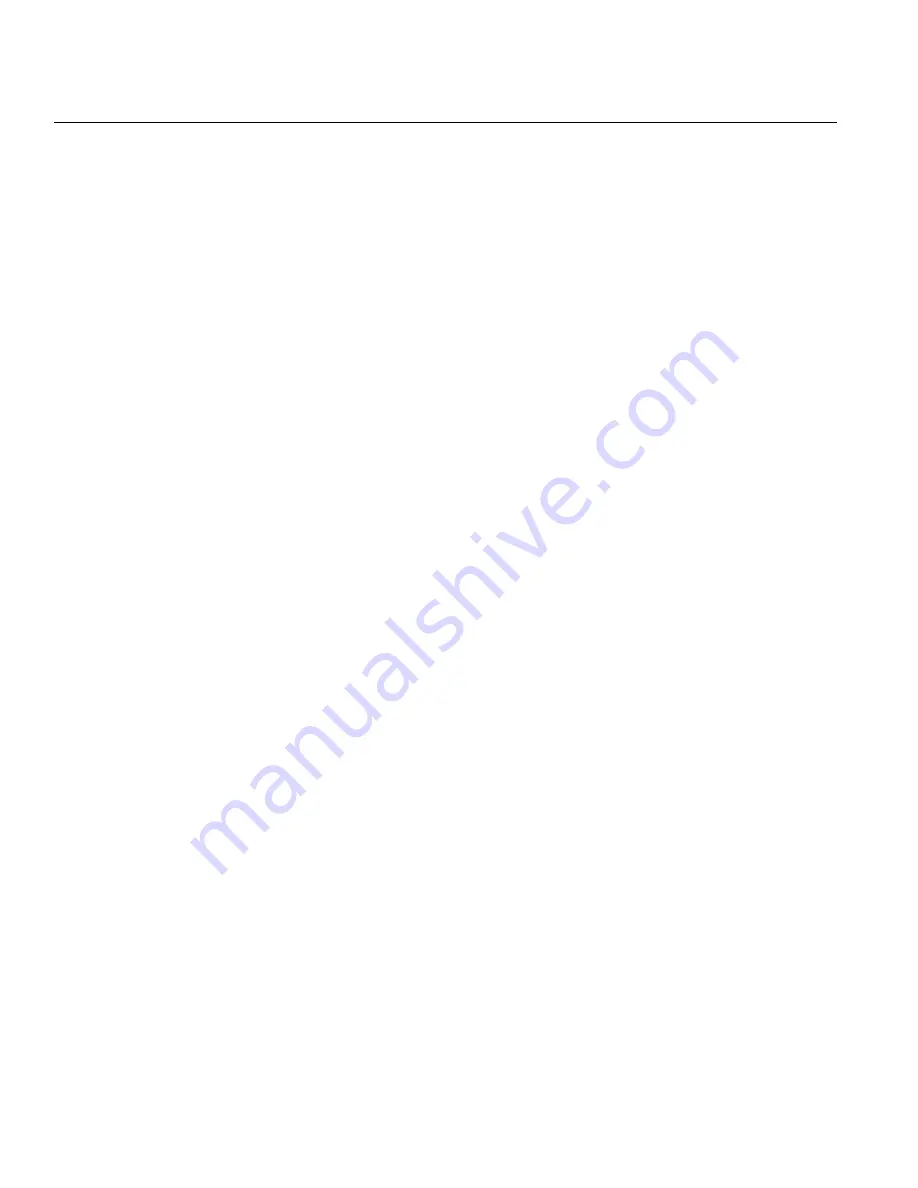
IB 6.2.11.1-1C
Page 14
ABB
Circuit Breaker Removal
To move the circuit breaker to the TEST position or to
remove it from the compartment, proceed as follows:
1. On electrically operated (EO) models, turn the motor
disconnect switch to the OFF position.
2. With the compartment door closed, trip the circuit
breaker by means of the remote mounted control
switch or manual TRlP button on the escutcheon.
3. Lift the racking shutter, insert the racking crank and
turn counterclockwise until the position indicator on the
right-hand side of the escutcheon shows TEST
position. (NOTE: The circuit breaker may be tested in
this position; the primary contacts are disconnected
and the control contacts are connected.)
4. Continue turning the racking crank counterclockwise
until the position indicator on the right-hand side of the
escutcheon shows DISCONNECTED position.
5. The circuit breaker may not be racked out with the
closing springs charged. At a point between the
DISCONNECTED and OUT positions, the closing
springs will automatically discharge.
6. Rack the circuit breaker through the DISCONNECT
position to the OUT position. Rack the circuit breaker
as far as the stops will allow but DO NOT FORCE.
Open the cubicle door.
7. Pull circuit breaker forward until tracks are in the fully
extended and latched position.
8. Using a lifting yoke, just pick up the circuit breaker
weight.
9. Lift the pivoting latches on the sides of the breaker,
and pull the breaker forward to release the positioning
pins from the cut-out sections of the tracks.
10. Lift the circuit breaker free from the tracks.
11. Release latch on each track, push tracks into the
compartment, and close compartment door.
MAINTENANCE AND INSPECTION
Safety Notes
De-energize both primary circuits and secondary
control circuits before making any inspections,
adjustments or parts replacements. Check the OPEN/
CLOSED indicator for contact status and closing spring
charge indicator for closing spring status.
When it is necessary to charge the closing springs and/
or operate the circuit breaker during maintenance, keep
hands and tools away from operating parts.
Circuit breakers should be withdrawn to the TEST
position for checking the breaker operation. For further
inspection, adjustments, cleaning, or parts
replacement, the circuit breaker should be withdrawn
and moved to a suitable work area.
Periodic Maintenance Inspection
The safety and successful functioning of downstream
devices depends upon the proper operation of their
feeder circuit breaker. Therefore, a maintenance
program should be established that will provide for
periodic inspection of the circuit breaker as follows:
KP-8, KPE-8, or KDP-8 - After 1,750 Operations
KPH-8, KP-16, KPE-16, KDP-16 or KP-20 - After 500
Operations
Note: An operation counter is available as an option.
The above inspection periods apply for no load or load
current switching. At the end of the first year of service
the circuit breaker should be inspected regardless of
the number of operations on it.
If the total number of operations in service is very low,
maintenance schedules should be based on time rather
than operations; yearly inspections are advised. When
operations are low, moreover, mechanism exercising is
important.
The circuit breaker should always be inspected after
short circuit or severe overload interruption, regardless
of the time elapsed or number of operations since the
last maintenance interval. When the circuit breaker is
used as a contactor, where it may be operated by
automatic switching devices, the operations on it will
accumulate more quickly necessitating more frequent
inspection. ANSI Standard C37.16 can provide
additional information on this subject.
Where unusual service conditions exist, it must be
assumed that the conditions were considered at the
time of order; that the equipment supplied was
designated for the special application; and that an
appropriate supplemental maintenance program has
been developed. Maintenance records containing the
date of last inspection and the condition of the circuit
breaker, as well as any adjustments or replacements
made, should be filed as a guide for any special