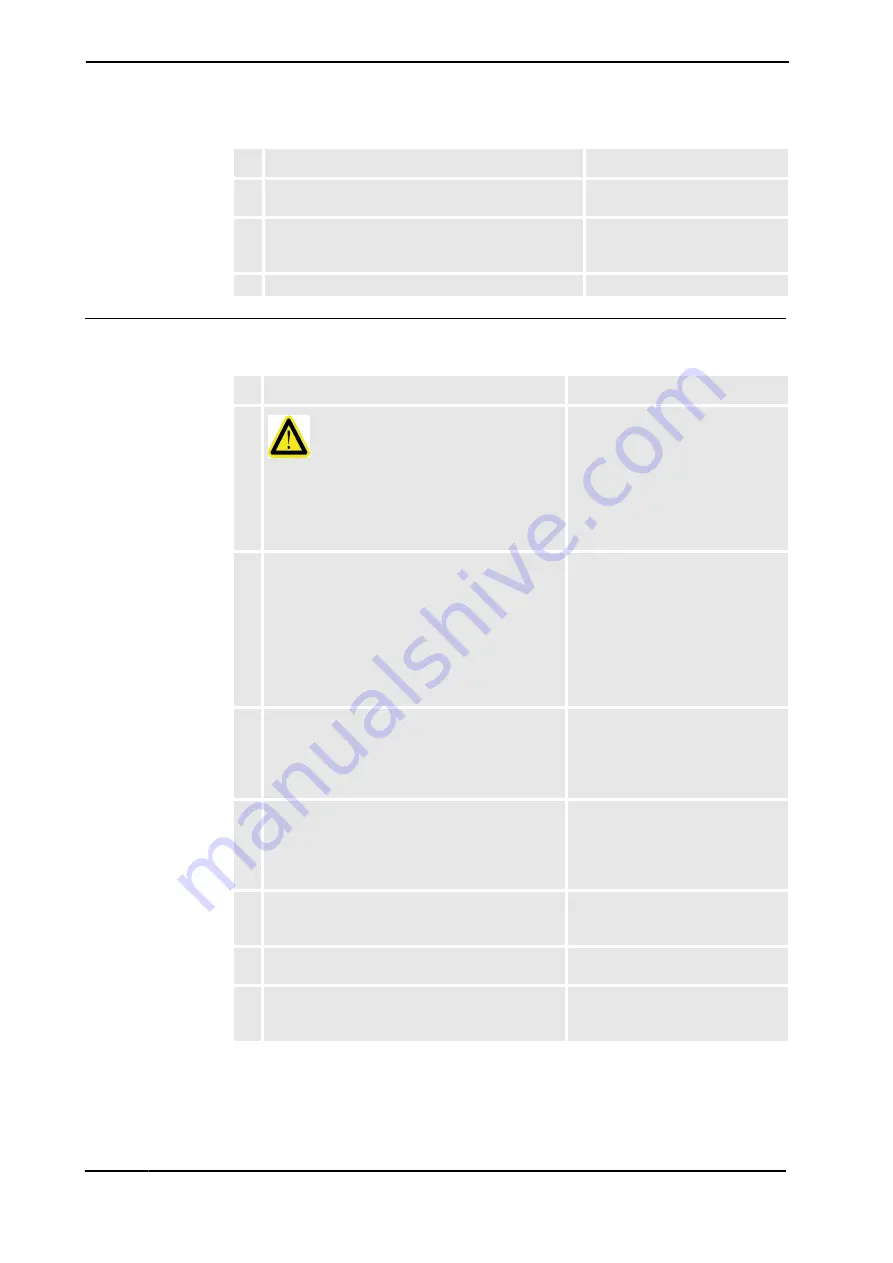
4 Repair
4.3.4. Replacement of cable harness, axes 1-4- IRB 6640ID
3HAC026876-001 Revision: C
224
© Copyri
ght
200
6-2008 ABB.
All rights reserved.
Refitting, cable harness, axes 1-4
The procedure below details how to refit the cable harness, axes 1-4.
14. Disconnect connector R2.M5/6 at the cable division
point.
!
15. Disconnect all connectors at motor 3 and motor 4.
Specified and shown in the figure
Location of cable harness on
page 220
16. Gently pull the cable harness out.
Action
Note
Action
Note
1.
DANGER!
Turn off all electric power, hydraulic and
pneumatic pressure supplies to the robot!
For Foundry Prime robots: Do not turn off the air
pressure to motors and SMB.
2. In order to facilitate refitting of cable harness,
move the robot to the specified position:
•
Axis 1: 0 degrees
•
Axis 2: 0 degrees
•
Axis 3: 0 degrees
•
Axis 4: 0 degrees
•
Axis 5: +90 degrees
•
Axis 6: no significance
Axes 2 and 3 may be tilted slightly
to improve access.
3. Pull the cable and connectors down through the
cable guide in the center of the frame.
Make sure the cables are not
twisted with each other or with
eventual customer harnesses!
Make a note of the correct positions
of the connectors!
4. Reconnect connectors R1.MP and R1.SMB at the
rear cover plate.
Make a note of the correct positions
of the connectors!
Attachment point is shown in the
figure
5. Reconnect the earth cable.
Attachment point is shown in the
figure
6. Refit the rear cover plate to the robot with its
attachment screws.
Shown in the figure
.
7. Reconnect all connectors at motors 1 and 2.
Specified and shown in the figure
Location of cable harness on page
220
!
Continued
Continues on next page