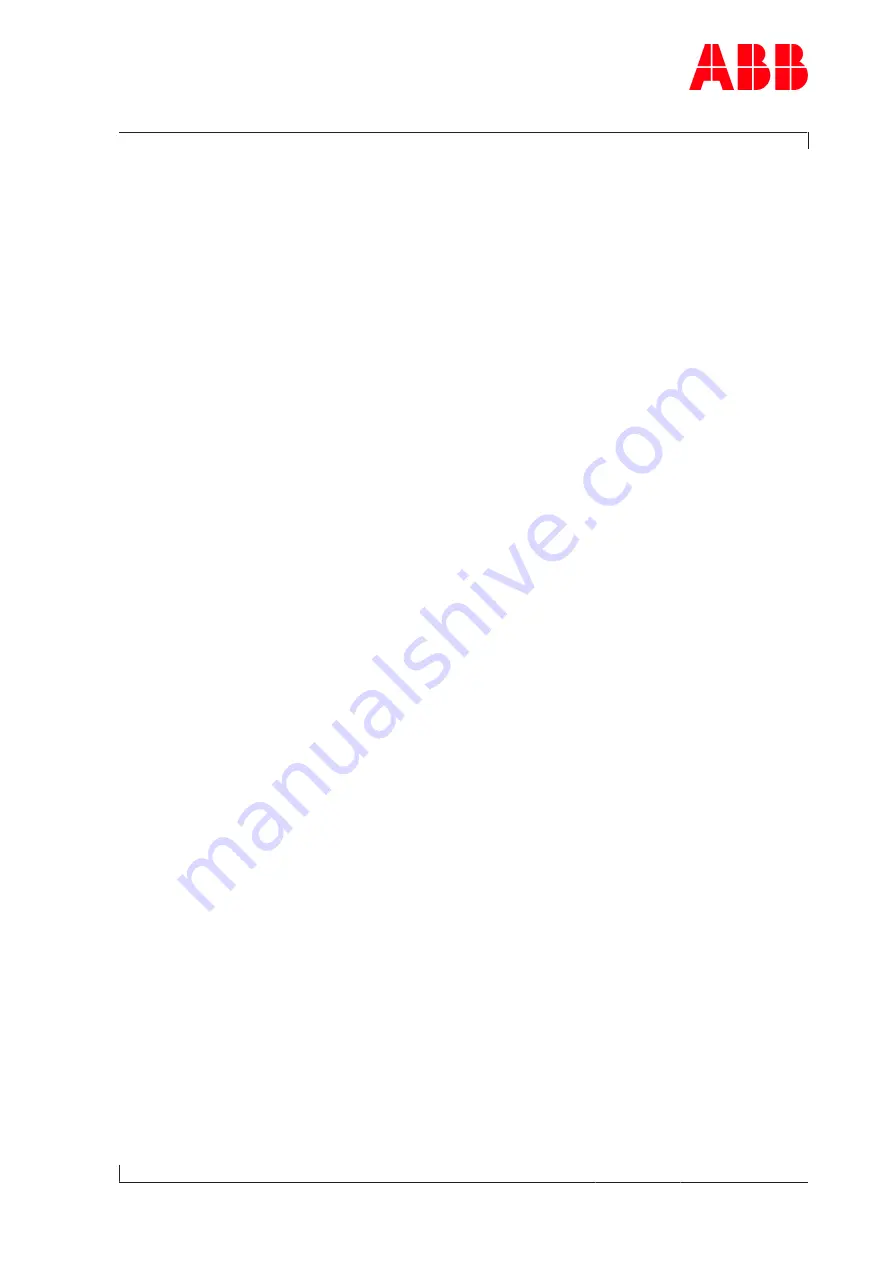
Operation Manual / A130-M.. - A145-M..
5 Monitoring operation / 5.3 Turbocharger speed
© Copyright 2021 ABB. All rights reserved.
HZTL4031_EN
Rev.N
March 2021
5.3.3
Speed differences with several turbochargers per engine
The speeds of all turbochargers on an engine vary only slightly from each other in standard
operation.
The difference between the highest and the lowest turbocharger speed must not be more
than 3 %, relative to the speed limit n
Bmax
.
If this permissible range of difference is exceeded, the following steps must be carried out:
u
Reduce the engine performance immediately to the point at which the maximum tur-
bocharger speed does not exceed 70 % of n
Bmax
.
u
If the engine cannot be stopped, it can continue to be driven at this reduced engine load
or turbocharger speed.
u
If a turbocharger surges continuously, the engine performance must be reduced further.
u
Measure the temperatures in the air lines and gas piping from and to the turbochargers
and compare with normal values. If clear deviations of temperature are found, the nearest
ABB Turbocharging Service Station has to be contacted.
u
Check the pressure loss of the alternative air inlet and compare it with normal values.
If the engine can be stopped temporarily:
u
Inspect air lines, gas piping and the turbochargers and remedy any malfunctions.
u
In any case, contacting the nearest ABB Turbocharging Service Station is recommended.
5.3.4
Malfunctions on the speed measurement system
In the case of malfunctions of the speed measurement system, refer to the chapter entitled
Troubleshooting/
Page
53
/
149