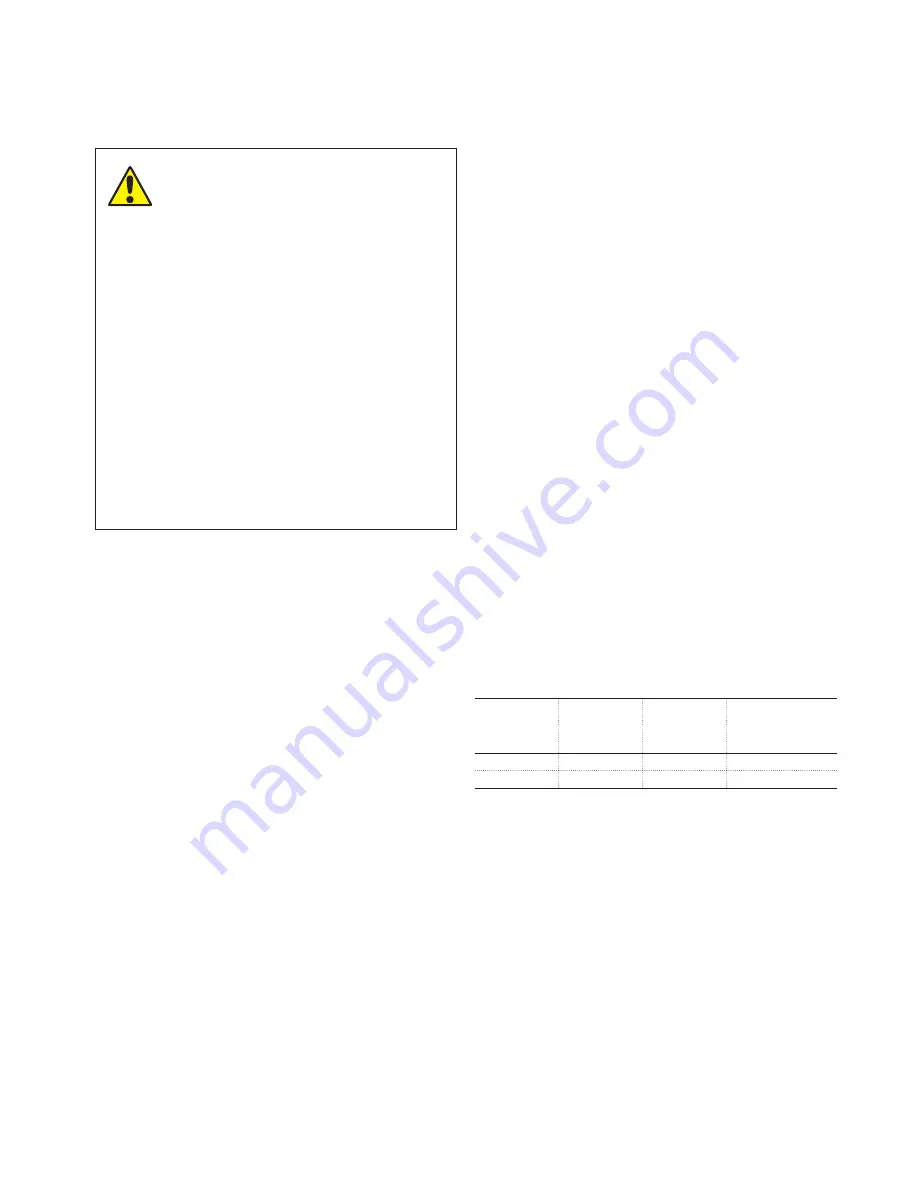
29
6. Service and maintenance
6.1. General recommendations and
precautions
Tools required
– Screwdriver
– Hand screwdrivers for 10 mm screws
– M10 (M8) torque wrench
– Size 5, 6 and 8 hex screw wrenches
– Vacuum cleaner
– Cleansing wipes
– Slightly alkaline detergent
− Do not use trichloroethane, carbon tetrachloride or any
kind of alcohol, etc., for cleaning purposes.
– Clean water
– Silicone liquid
− In special cases, insulating surfaces can be covered by a
thin layer of silicone liquid like DC200/100CS, or similar
products.
– Test equipment.
Checkpoints
– Check that there are no visibile signs of partial discharges
or damage caused by them.
– There should be no visible signs of overheated connections.
– All components should perform perfectly and any faulty
components must be replaced.
Maintenance instructions
Maintenance preserves trouble-free operation and ensures the
switchgear remains functional for the longest possible time.
It comprises the following closely related activities:
– Inspection: Determination of the effective conditions
– Servicing: Measures to preserve the specified conditions
– Repairs: Measures to restore the specified conditions.
The inspection and servicing intervals for some of the
apparatuses/components (e.e. parts subject to wear) are
determined by fixed criteria, such as switching frequency,
length of service and number of short-circuit breaking
operations. On the other hand, for other parts, the length
of the intervals may depend, for example, on the different
modes of operation in individual cases, the degree of loading
and environmental factors (including pollution and corrosive
atmosphere).
The intervals at wich maintenance work must be carried out
always depend on the operating conditions of the switchgear
and, above all, on the operating mode, the number of rated
and short-circuit switching operations, ambient temperature,
pollution, etc.
The maintenance intervals and measures to be taken given in
table 18 are recommended for GSec switchgear under normal
service conditions. Three intervals per year are recommended
for all maintenance measures in more demanding conditions
(such as areas with high pollution levels). Switch-disconnector
1S and 2S operating mechanisms are maintenance-free and
do not need any lubrication.
6.2. Maintenance intervals
It is advisable to perform maintenance operations at the
following intervals:
Task
performed
Time interval
in years
According
to section
According to
number
of switching opera-
tions
Inspection
5 (1)
6.3
Maintenance
5 (2)
6.4
(3)
GSec switchgear must be completely replaced after the following
intervals:
– 100 breaking operations at 630 A
– 5 short-circuit making operations in line
– 5000 mechanical operations for 1S operating mechanism in line
– 1000 mechanical operations for 2S operating mechanism in line
– 5 making operations
– 1000 mechanical operations (M0) on earth
WARNING
Pay attention to the following safety
recommendations:
Preparing the switchgear for safe assembly
1. For each case, define safe working
conditions with the utility safety officer.
2. Make sure that the national safety
regulations are followed.
3. Make sure there is no voltage in the
busbars and cable terminals and that the
risk of reconnection has been eliminated
in all units. Remote control must also be
inhibited.
4. Set the switch (or combined switch-fuse
unit) to the “open” position and then to the
“earthed” position.
5. Make sure that the auxiliary circuits are
also disconnected from all possible power
supply sources (including instrument
transformers).
(1) These intervals should be reduced in more complex operating conditions.
(2) Depending on the results of the inspections.
(3) GSec
Electrical endurance:
100 breaking operations at 630 A
5 short-circuit making operations
Mechanical endurance: 5000 no-load operations
Circuit-breakers:
see the manuals.
Earthing switch
5 making operations − 1000 no-load operations
Table 18. Maintenance intervals
Summary of Contents for GSec/IB
Page 43: ...43 ...