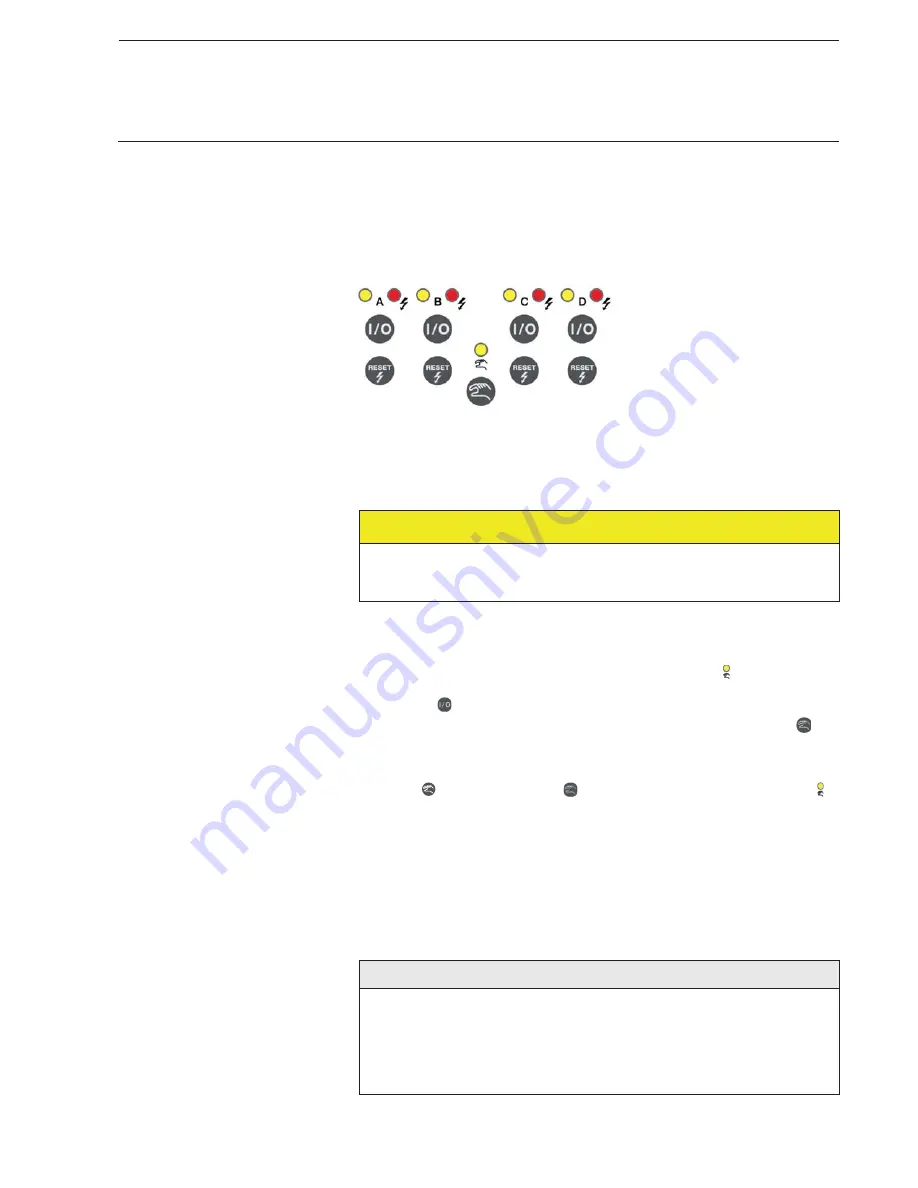
ABB i-bus
£
KNX
Device technology
© 2010 ABB STOTZ-KONTAKT GmbH
11
2.6
Manual operation
General
The outputs can be directly controlled using the manual pushbuttons
in manual operation.
Accordingly, the wiring of the loads connected to the outputs can be verified
during commissioning. You can, for example, ensure that the connected
valve drives open or close the valves correctly. If bus voltage is not yet
available at the time of commissioning, the device can be supplied with
power for manual operation using the Power Supply NTI/Z.
Caution
The manual pushbuttons may not be operated with pointed or sharp-
edged objects, e.g. screwdrivers or pens.
This may damage the keypad.
Supplied state
Manual operation is enabled by default in the supplied state. The device is
in KNX mode after connection to the bus. The yellow LED is off. All LEDs
for the outputs indicate the actual state.
The buttons
for the outputs are non-functional.
You toggle between manual mode and KNX mode by pressing button
.
Activation of manual operation
The pushbuttons can be activated and deactivated by the button
Manual
operation
. To activate, button
must be pressed until the yellow LED
lights continuously (prerequisite: Manual operation is enabled in the appli-
cation program). The LED flashes during switchover. If manual operation
is activated, the current set value of the respective output
is retained and the yellow LEDs on the outputs indicate the current status
(ON/OFF). A target position which may not have yet been achieved is ap-
proached. The outputs can now only be operated via the manual pushbut-
tons. The first button push switches on the output if the control value = 0.
If the control value > 0, the output is switched off. Every subsequent button
push toggles the output.
Note
Manual operation can be inhibited via the KNX using communication ob-
ject
Enable/block manual operation
(No. 2). In this case, it is not possible
to change over to manual operation using button
Manual operation
.
The block can be removed by sending a telegram with the value 0 on the
communication object (No. 2). The block is also removed after a download
and bus voltage recovery.
Summary of Contents for ES/S 4.1.2.1
Page 1: ...ABB i bus KNX Electronic Switch Actuator ES S 4 1 2 1 Product Manual ...
Page 2: ......
Page 4: ......
Page 16: ......
Page 58: ...ABB i bus KNX Appendix 2010 ABB STOTZ KONTAKT GmbH 56 A 5 Notes ...
Page 59: ......