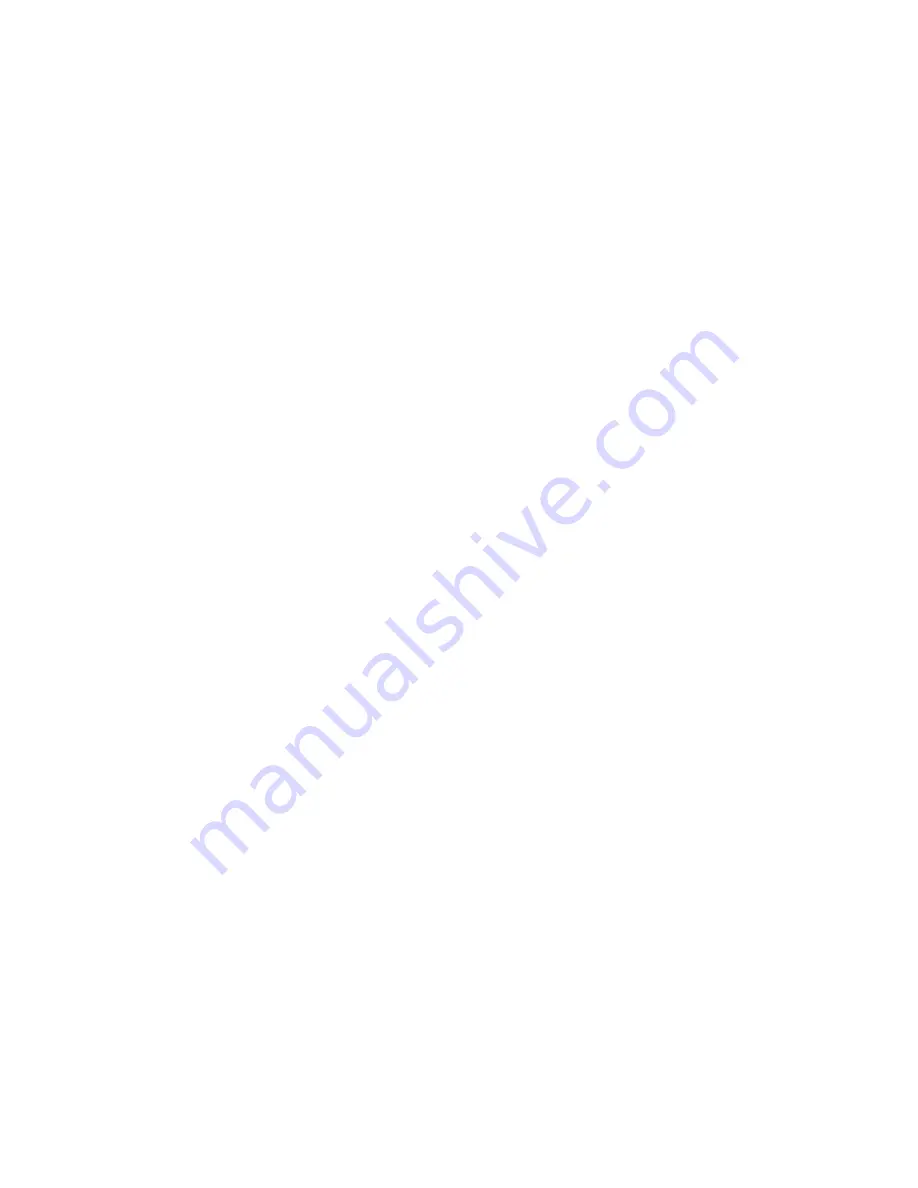
22
E M A X LI N K 2 A B B R E V I ATE D
LV S W I TC H G E A R A P P L I C AT I O N G U I D E
Inspect busbars
Changes in environmental conditions can cause the
busbar mounting components to loosen over time.
During scheduled inspections, check the condition
of the busbar system in locations where it is
possible to access them. The components that can
be removed to provide busbar access include the
rear panels, side walls, segregation barrier between
the cable compartment and main busbar
compartment, and the roof plates.
Exterior metal damage repair
Any scratches or damage to the surface of the
vertical sections must be repaired in order to
avoid oxidation, which can reduce the life of
the equipment.
Maintenance schedule
A periodic maintenance program for the
switchgear is highly recommended. The frequency
of maintenance activities depends on equipment
usage and the operating environment.
Perform a visual inspection, front and rear, to see
that there is no evidence of loose parts, warping
or undue vibration. Take steps to remedy any
deficiencies of this nature that may appear. Keep
the assembly dry. Cover to prevent moisture from
dripping on the equipment. Do not block vents.
—
Installation guidelines
There are hazards of electrical shocks and/or burns
whenever working in or around electrical
equipment. Turn off power ahead of the switchgear
before performing any maintenance operations
and follow lockout/tagout procedures. Check
incoming line terminals to verify that the
equipment is de-energized. Check outgoing
terminals to make sure that no feedback
conditions exist.
Use OSHA approved of solvents to remove grease
and contamination from primary conductors,
insulation, and unpainted metallic surfaces.
Do not use alcohol or halocarbon products. Use
a non-flammable solvent with a threshold limit
of 300 PPM or higher. Use solvents in well-
ventilated areas.