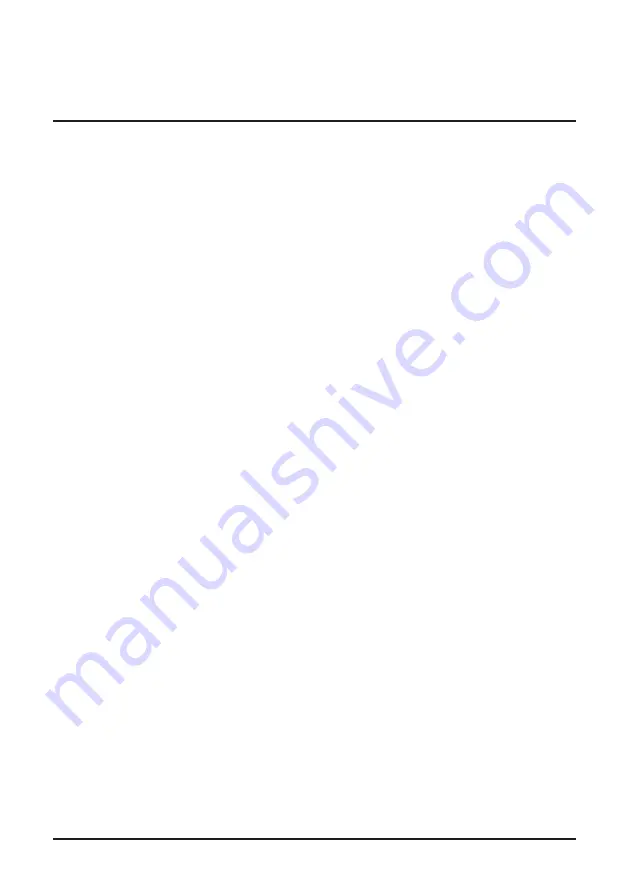
1-1
MN1240
Section 1
General Information
Overview
This manual contains general procedures that apply to ABB Motor products.
Be sure to read and understand the Safety Notice statements in this manual.
For your protection, do not install, operate or attempt to perform maintenance
procedures until you understand the Warning and Caution statements.
A Warning statement indicates a possible unsafe condition that can cause harm to
personnel.
A Caution statement indicates a condition that can cause damage to equipment.
Important: This instruction manual is not intended to include a comprehensive listing
of all details for all procedures required for installation, operation and maintenance.
This manual describes general guidelines that apply to most of the motor products
shipped by ABB. If you have a question about a procedure or are uncertain about any
detail,
Do Not Proceed .
Please contact your distributor for more information for clarification.
Before you install, operate or perform maintenance, become familiar with the following:
• NEMA Publication ICS16, Motion/Position Control Motors; Controls; and
Feedback Devices.
• The National Electrical Code
• Local codes and Practices
Safety Notice:
This equipment contains high voltage! Electrical shock can cause serious or fatal injury.
Only qualified personnel should attempt installation, operation and maintenance of
electrical equipment. Be sure that you are completely familiar with NEMA publications
ICS16 and MG-2, safety standards for construction and guide for selection,
installation and use of electric motors and generators, the National Electrical Code
and local codes and practices. Unsafe installation or use can cause conditions that
lead to serious or fatal injury. Only qualified personnel should attempt the installation,
operation and maintenance of this equipment.
WARNING: Do not use these motors in the presence of flammable or combustible vapors
or dust. These motors are not designed for atmospheric conditions that require
explosion proof construction.
WARNING: Do not touch electrical connections before you first ensure that power has been
disconnected. Electrical shock can cause serious or fatal injury. Only qualified
personnel should attempt the installation, operation and maintenance of this
equipment.
WARNING: Be sure the system is properly grounded before applying power. Do not apply
power before you ensure that all grounding instructions have been followed.
Electrical shock can cause serious or fatal injury. National Electrical Code and
Local codes must be carefully followed.
WARNING: Avoid extended exposure to machinery with high noise levels. Be sure to wear
ear protective devices to reduce harmful effects to your hearing.
WARNING: The holding brake alone does not guaranty personnel safety. Use structural
measures such as protective fences or a second brake to secure personnel
safety.
WARNING: This equipment may be connected to other machinery that has rotating parts or
parts that are driven by this equipment. Improper use can cause serious or fatal
injury. Only qualified personnel should attempt to install, operate, or maintain
this equipment.
Summary of Contents for BSM100
Page 1: ... MN1240_October 2021 October 2021 Brushless Servo Motors Installation and Operating Manual ...
Page 4: ...ii MN1240 ...
Page 7: ...1 3 MN1240 ...
Page 23: ......