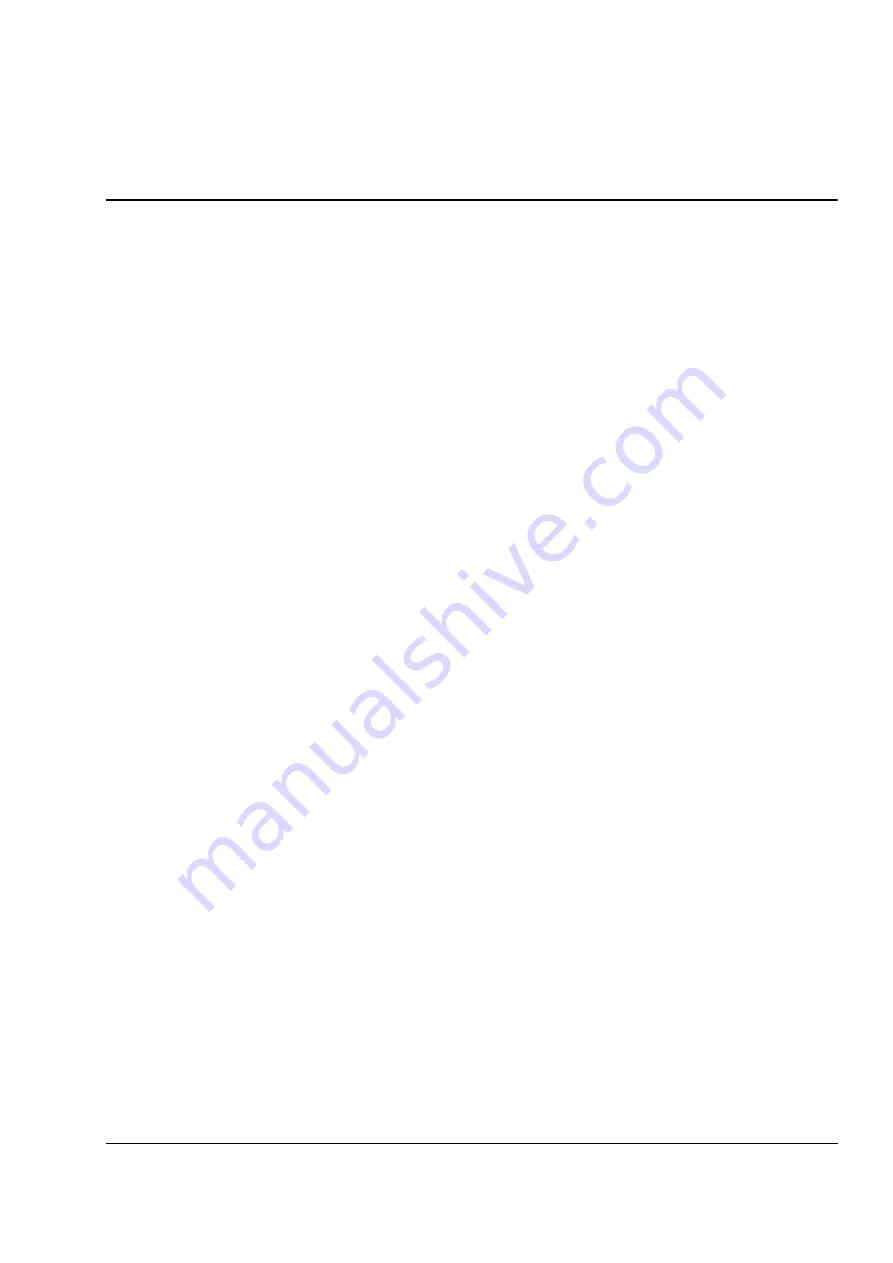
Planning the electrical installation
37
Planning the electrical installation
What this chapter contains
This chapter contains the instructions that you must follow when selecting the motor,
cables, protections, cable routing and way of operation for the drive. If the
recommendations given by ABB are not followed, the drive may experience
problems that the warranty does not cover.
Note:
The installation must always be designed and made according to applicable
local laws and regulations. ABB does not assume any liability whatsoever for any
installation which breaches the local laws and/or other regulations.
Motor selection and compatibility
Select the (3-phase AC induction) motor according to the rating table in the chapter
. The table lists the typical motor power for each drive type.
Only one permanent magnet synchronous motor can be connected to the inverter
output. It is recommended to install a safety switch between the permanent magnet
motor and the drive output in order to isolate the motor from the drive during
maintenance work on the drive.
Protecting the motor insulation and bearings
The output of the drive comprises – regardless of output frequency – pulses of
approximately 1.35 times the equivalent mains network voltage with a very short rise
time. This is the case with all drives employing modern IGBT inverter technology.
The voltage of the pulses can be almost double at the motor terminals, depending on
the attenuation and reflection properties of the motor cable and the terminals. This in
turn can cause additional stress on the motor and motor cable insulation.
Modern variable speed drives with their fast rising voltage pulses and high switching
frequencies can generate current pulses that flow through the motor bearings, which
can gradually erode the bearing races and rolling elements.
The stress on motor insulation can be avoided by using optional ABB du/dt filters.
du/dt filters also reduce bearing currents.
To avoid damage to motor bearings, the cables must be selected and installed
according to the instructions given in the hardware manual. With a non-ABB motor,
optional du/dt filtering is also recommended. An insulated N-end (non-drive end)
bearing is recommended if the motor is random-wound, or if the motor power is
above 100 kW.
Summary of Contents for ACSM1-04 Series
Page 1: ...ACSM1 Hardware Manual ACSM1 04 Drive Modules 55 to 110 kW ...
Page 2: ......
Page 4: ......
Page 18: ...About this manual 18 ...
Page 22: ...The ACSM1 04 22 ...
Page 64: ...Electrical installation 64 ...
Page 70: ...Maintenance 70 ...
Page 82: ...Technical data 82 ...
Page 88: ...Dimension drawings 88 Drive module ...
Page 89: ...Dimension drawings 89 Drive module continued from previous page ...
Page 91: ......