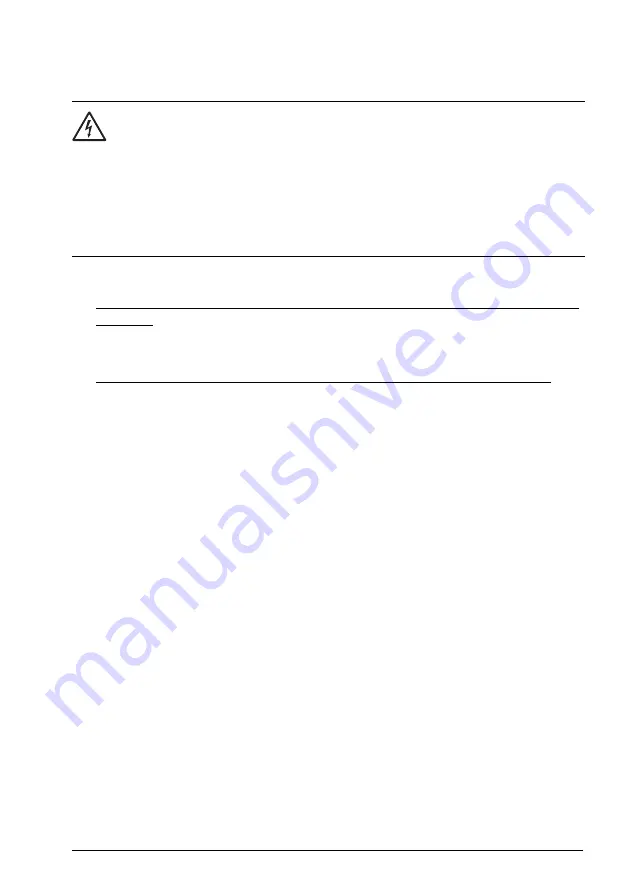
Implementing a motor temperature sensor connection
WARNING!
IEC 61800-5-1 requires double or reinforced insulation between live parts and
accessible parts when:
• the accessible parts are not conductive, or
• the accessible parts are conductive, but not connected to the protective earth.
Obey this requirement when you plan the connection of the motor temperature
sensor to the drive.
You have these implementation alternatives:
1. If there is double or reinforced insulation between the sensor and the live parts of
the motor: You can connect the sensor directly to the analog/digital input(s) of the
drive. See the control cable connection instructions. Make sure that the voltage
does not exceed the maximum allowed voltage over the sensor.
2. If there is basic insulation between the sensor and the live parts of the motor: You
can connect the sensor to the analog/digital input(s) of the drive. All other circuits
connected to the digital and analog inputs (typically extra-low voltage circuits) must
be:
• protected against contact, and
• insulated with basic insulation from other low-voltage circuits. The insulation
must be rated for the same voltage level as the drive main circuit.
Note:
Extra-low voltage circuits (for example, 24 V DC) typically do not meet these
requirements.
Make sure that the voltage does not exceed the maximum allowed voltage over the
sensor.
As an alternative, you can connect the sensor with basic insulation to the
analog/digital input(s) of the drive, if you do not connect any other external control
circuits to the drive digital and analog inputs.
3. You can connect the sensor to the drive via an option module. The sensor and the
module must form a double or reinforced insulation between the motor live parts
and the drive control unit. See
Connecting motor temperature sensor to the drive
via an option module (page 76)
. Make sure that the voltage does not exceed the
maximum allowed voltage over the sensor.
4. You can connect a sensor to a digital input of the drive via an external relay. The
sensor and the relay must form a double or reinforced insulation between the motor
live parts and the digital input of the drive. Make sure that the voltage does not
exceed the maximum allowed voltage over the sensor.
Guidelines for planning the electrical installation 75
Summary of Contents for ACS880-11
Page 1: ... ABB INDUSTRIAL DRIVES ACS880 11 drives Hardware manual ...
Page 2: ......
Page 4: ......
Page 26: ...26 ...
Page 52: ...52 ...
Page 82: ...82 ...
Page 95: ...R6 R8 IP21 R6 R8 IP55 Electrical installation IEC 95 ...
Page 103: ...R6 1 5 N m 0 5 N m Electrical installation IEC 103 ...
Page 104: ...R8 1 5 N m 0 5 0 6 N m 104 Electrical installation IEC ...
Page 116: ...R6 R8 UL Type 1 R6 R8 UL Type 12 116 Electrical installation North America NEC ...
Page 142: ...142 ...
Page 154: ... Fan arrow must point up 154 Maintenance ...
Page 160: ...160 ...
Page 181: ... Package dimensions R6 R3 R8 Technical data 181 ...
Page 202: ...R3 IP21 UL Type 1 3AXD50000045323 202 Dimension drawings ...
Page 203: ...R3 Option B056 IP55 UL Type 12 3AXD50000045322 Dimension drawings 203 ...
Page 204: ...R6 IP21 UL Type 1 3AXD50000045353 204 Dimension drawings ...
Page 205: ...R6 Option B056 IP55 UL Type 12 3AXD50000045352 Dimension drawings 205 ...
Page 206: ...R8 IP21 UL Type 1 3AXD50000047667 206 Dimension drawings ...
Page 207: ...R8 Option B056 IP55 UL Type 12 3AXD50000047667 Dimension drawings 207 ...
Page 208: ...208 ...
Page 225: ... Declarations of conformity The Safe torque off function 225 ...