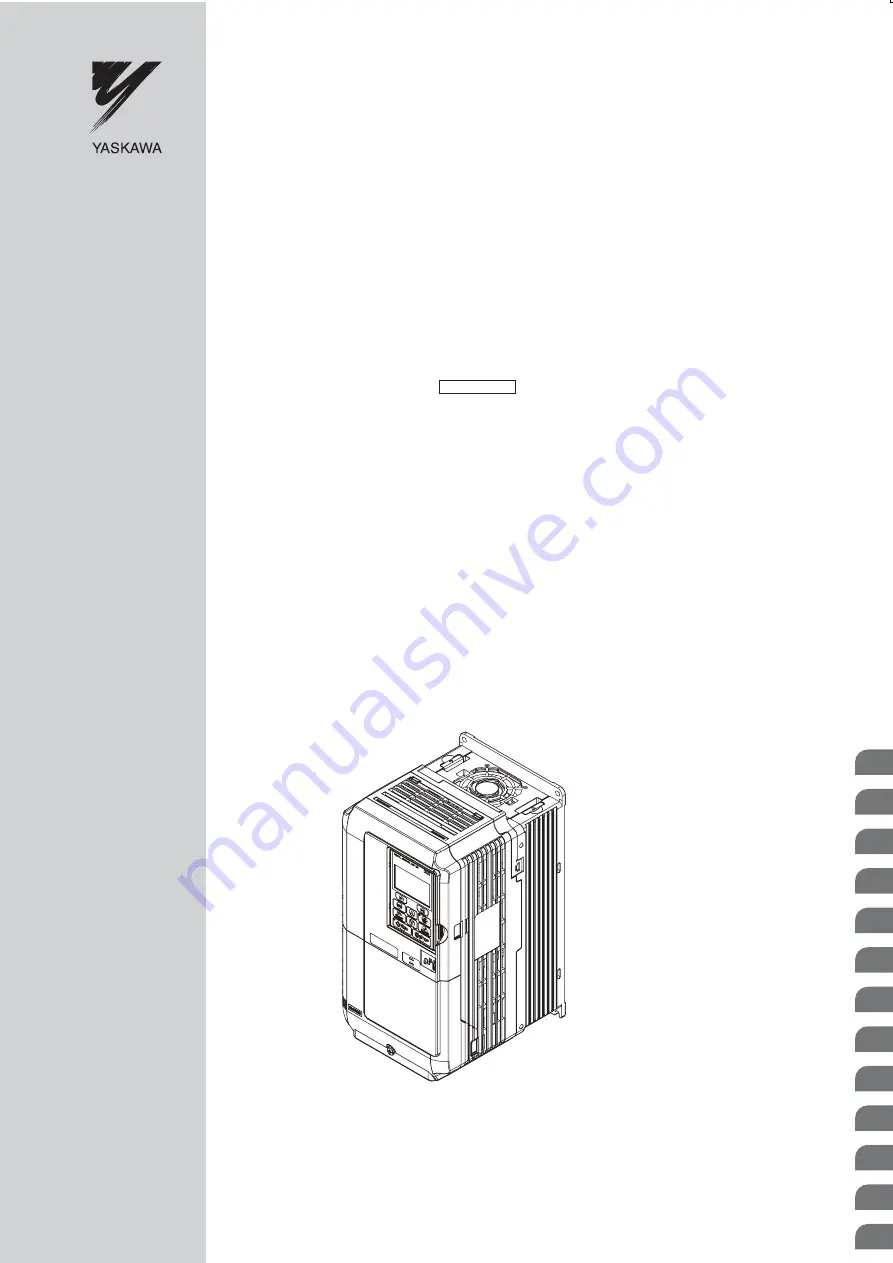
YASKAWA AC Drive L1000V
AC Drive for Elevator Applications
Technical Manual
Models: 200 V Class: 4.0 to 15 kW
400 V Class: 4.0 to 15 kW
To properly use the product, read this manual thoroughly and retain
for easy reference, inspection, and maintenance. Ensure the end user
receives this manual.
Type: CIMR-LC
V
1
2
3
4
5
6
7
8
A
B
C
D
E
1
2
3
4
5
6
7
8
A
B
C
D
E
MANUAL NO. SIEP C710606 50A
Receiving
Mechanical Installation
Electrical Installation
Start-Up Programming &
Operation
Parameter Details
Troubleshooting
Periodic Inspection &
Maintenance
Peripheral Devices &
Options
Specifications
Parameter List
MEMOBUS/Modbus
Communications
Standards Compliance
Quick Reference Sheet
Summary of Contents for Lift Inverter L1000V
Page 4: ...4 YASKAWA EUROPE SIEP YASKAWA AC Drive L1000V Technical Manual...
Page 28: ...1 4 Component Names 28 YASKAWA EUROPE SIEP YASKAWA AC Drive L1000V Technical Manual...
Page 62: ...3 10 Wiring Checklist 62 YASKAWA EUROPE SIEP YASKAWA AC Drive L1000V Technical Manual...
Page 162: ...5 12 U Monitor Parameters 162 YASKAWA EUROPE SIEP YASKAWA AC Drive L1000V Technical Manual...
Page 279: ...8 YASKAWA EUROPE SIEP YASKAWA AC Drive L1000V Technical Manual...
Page 281: ...10 YASKAWA ELECTRIC SIEP C710616 33C YASKAWA AC Drive L1000A Technical Manual...