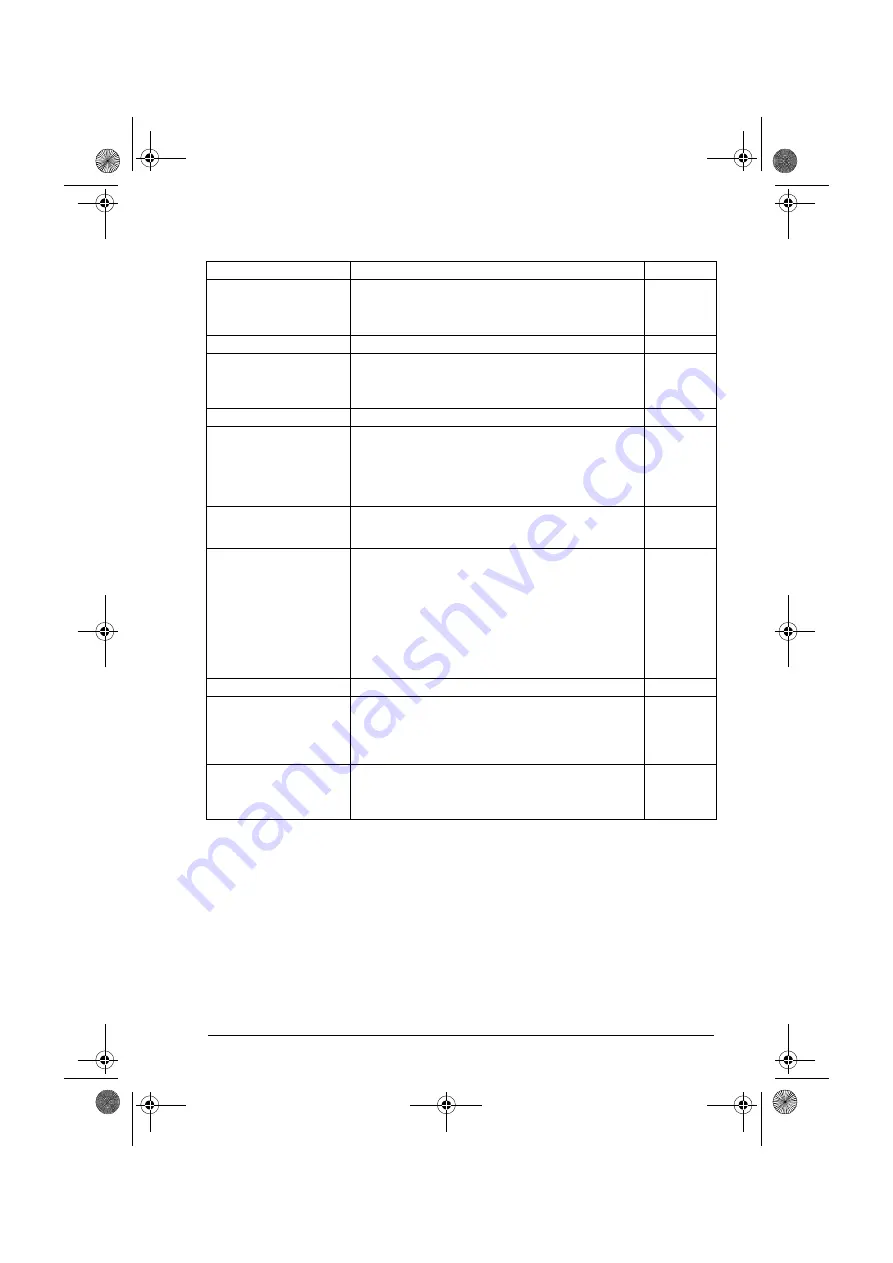
Parameters 339
Defines the nominal motor frequency. This setting must
match the value on the rating plate of the motor.
Note:
This parameter cannot be changed while the drive is
running.
50.0 Hz
0.0…500.0 Hz
Nominal frequency of the motor.
10 = 1 Hz
Defines the nominal motor speed. The setting must match the
value on the rating plate of the motor.
Note:
This parameter cannot be changed while the drive is
running.
0 rpm
0…30000 rpm
Nominal speed of the motor.
1 = 1 rpm
Defines the nominal motor power. The setting must match the
value on the rating plate of the motor. If multiple motors are
connected to the drive, enter the total power of the motors.
The unit is selected by parameter
.
Note:
This parameter cannot be changed while the drive is
running.
0.00 kW or
hp
0.00… 10000.00
kW or
0.00… 13404.83 hp
Nominal power of the motor.
1 = 1 unit
Defines the cosphi of the motor for a more accurate motor
model. The value is not obligatory, but is useful with an
asynchronous motor, especially when performing a standstill
identification run. With a permanent magnet or synchronous
reluctance motor, this value is not needed.
Notes:
• Do not enter an estimated value. If you do not know the
exact value, leave the parameter at zero.
• This parameter cannot be changed while the drive is
running.
0.00
0.00…1.00
Cosphi of the motor.
100 = 1
Defines the nominal motor shaft torque for a more accurate
motor model. Not obligatory. The unit is selected by
parameter
Note:
This parameter cannot be changed while the drive is
running.
0.000
N·m or lb·ft
0.000…4000000.000
N·m or
0.000…2950248.597
lb·ft
Nominal motor torque.
1 = 100 unit
No.
Name/Value
Description
Def/FbEq16
ACS580 FW.book Page 339 Wednesday, September 21, 2016 9:48 PM