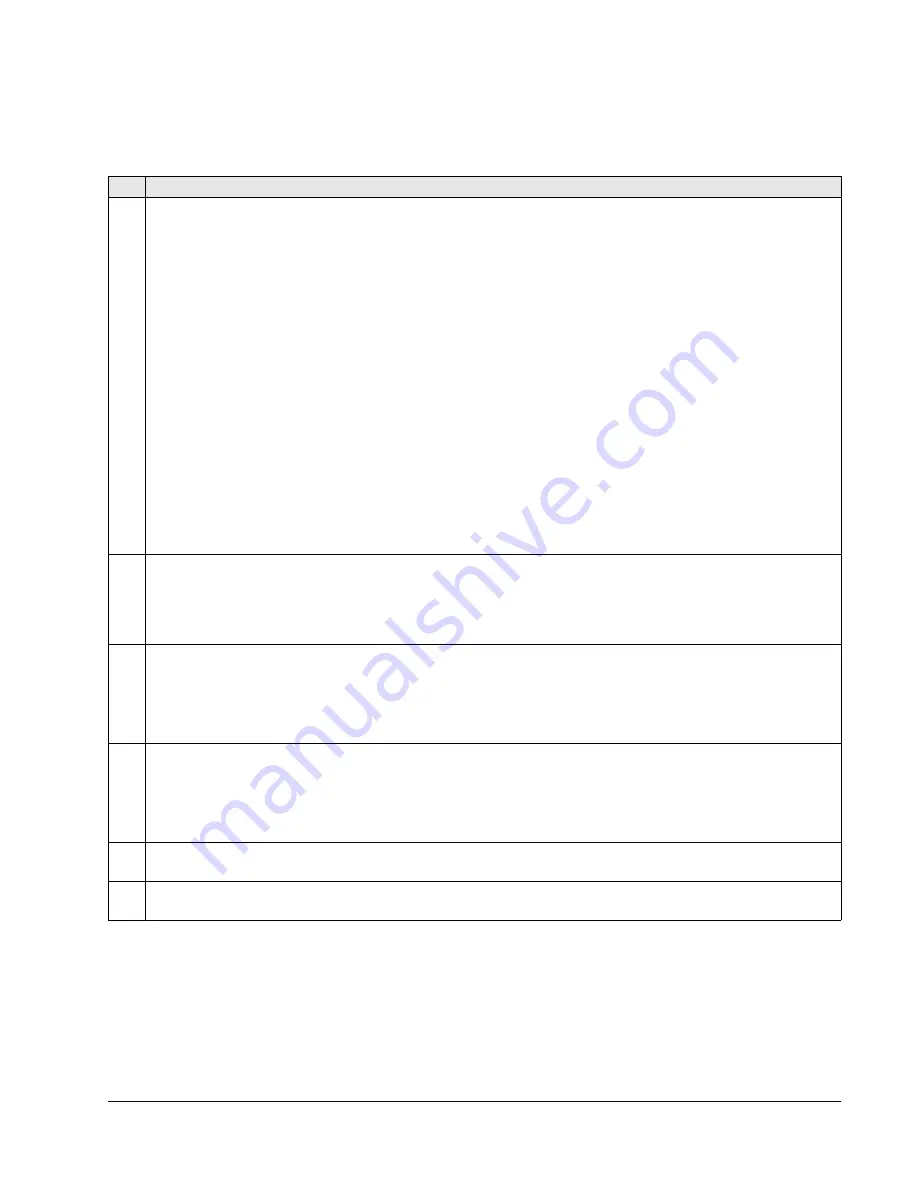
ACS510 User’s Manual
93
Start-Up
Group 21: Start/Stop
This group defines how the motor starts and stops. The ACS510 supports several
start and stop modes.
Code Description
2101
START FUNCTION
Selects the motor start method.
1 =
AUTO
– Selects the automatic start mode.
2 =
DC
MAGN
– Selects the DC Magnetizing start mode.
Note!
Mode cannot start a rotating motor.
Note!
The drive starts when the set pre-magnetizing time (param. 2103) has passed, even if motor magnetization is
not complete.
• Magnetizes the motor within the time determined by the parameter 2103
DC
MAGN
TIME
using DC current. The
normal control is released exactly after the magnetizing time.
3 =
SCALAR
FLYSTART
– Selects the flying start mode.
• The drive automatically selects the correct output frequency to start a rotating motor – useful if the motor is
already rotating and if the drive will start smoothly at the current frequency.
4 =
TORQ
BOOST
– Selects the automatic torque boost mode .
• May be necessary in drives with high starting torque.
• Torque boost is only applied at start, ending when output frequency exceeds 20 Hz or when output frequency is
equal to reference.
• In the beginning the motor magnetizes within the time determined by the parameter 2103
DC
MAGN
TIME
using DC
current.
• See parameter 2110
TORQ
BOOST
CURR
.
5 =
FLY
+
TORQ
BOOST
– Selects both the flying start and the torque boost mode .
• Flying start routine is performed first and the motor is magnetized. If the speed is found to be zero, the torque
boost is done.
8 =
RAMP
– Immediate start from zero frequency.
2102
STOP FUNCTION
Selects the motor stop method.
1 =
COAST
– Selects cutting off the motor power as the stop method. The motor coasts to stop.
2 =
RAMP
– Selects using a deceleration ramp
• Deceleration ramp is defined by 2203
DECELER
TIME
1 or 2206
DECELER
TIME
2 (whichever is active).
2103
DC MAGN TIME
Defines the pre-magnetizing time for the DC Magnetizing start mode.
• Use parameter 2101 to select the start mode.
• After the start command, the drive pre-magnetizes the motor for the time defined here, and then starts the motor.
• Set the pre-magnetizing time just long enough to allow full motor magnetization. Too long a time heats the motor
excessively.
2104
DC CURR CTL
Selects whether DC current is used for braking or DC Hold.
0 =
NOT
SEL
– Disables the DC current operation.
2 =
DC
BRAKING
– Enables the DC Injection Braking after modulation has stopped.
• If parameter 2102
STOP
FUNCTION
is 1 (
COAST
), braking is applied after start is removed.
• If parameter 2102
STOP
FUNCTION
is 2 (
RAMP
), braking is applied after ramp.
2106
DC CURR REF
Defines the DC current control reference as a percentage of parameter 9906
MOTOR
NOM
CURR
.
2107
DC BRAKE TIME
Defines the DC brake time after modulation has stopped, if parameter 2104 is 2 (
DC
BRAKING
).
Supplied from China by: Guangzhou Tofee Electro Mechanical Equipment Co., Ltd
Email: [email protected]