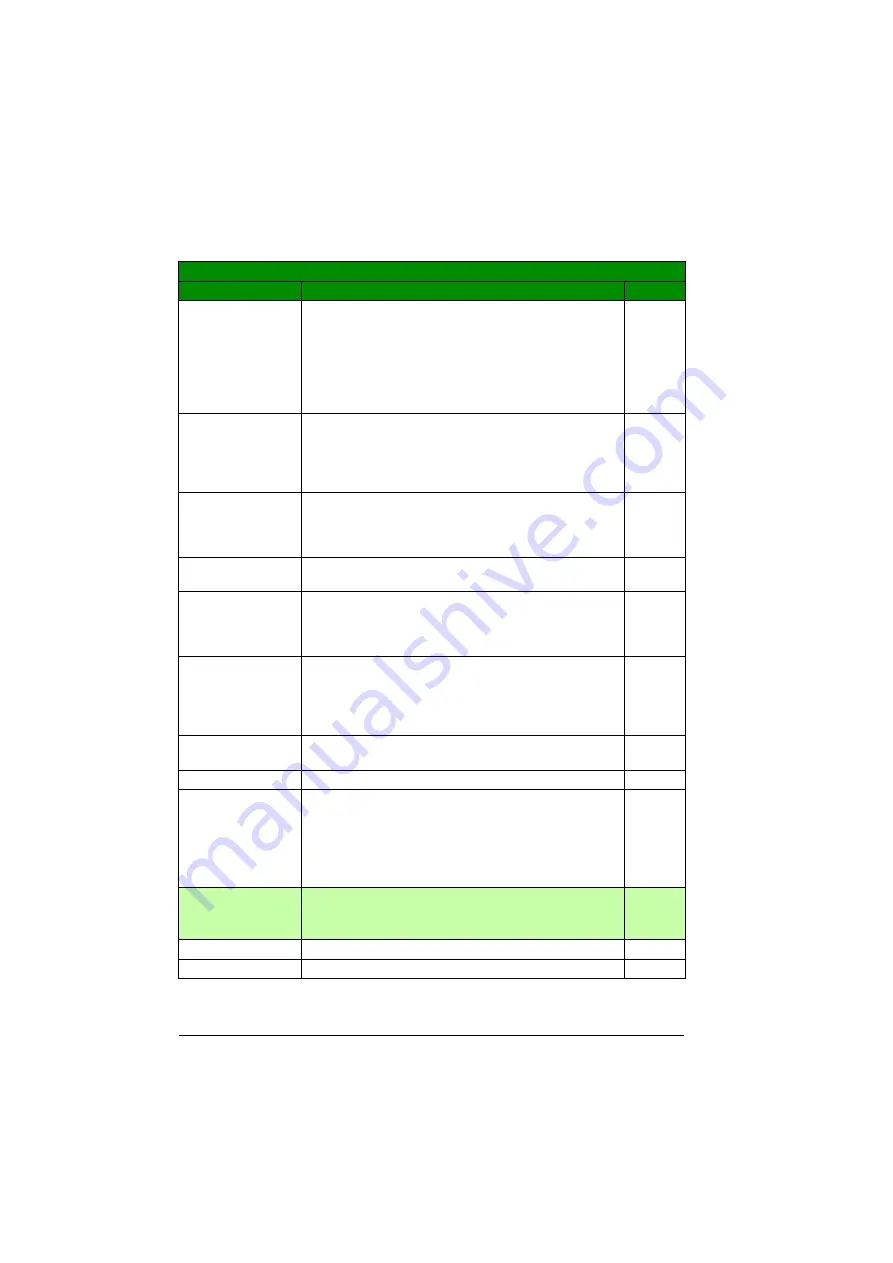
286 Actual signals and parameters
4304 FORCED
OPEN LVL
Defines the speed at brake release. Parameter setting
overrides parameter
setting. After
start, the drive speed is frozen to the set value, until the
motor is magnetized.
The purpose of this parameter is to generate enough start
torque to prevent the motor rotating into the wrong direction
because of the motor load.
0.0 = NOT SEL
0.0…100.0%
Value as a percentage of the maximum frequency (in scalar
control) or the maximum speed (in vector control). If
parameter value is set to zero, the function is disabled. The
control mode is selected by parameter
1 = 0.1%
4305 BRAKE MAGN
DELAY
Defines motor magnetizing time. After start drive
current/torque/speed is frozen to the value defined by
parameter
for the set time.
0 = NOT SEL
0…10000 ms
magnetizing time. If parameter value is set to zero, the
function is disabled.
1 = 1 ms
4306 RUNTIME
FREQ LVL
Defines the brake close speed. When frequency falls below
the set level during run, the brake is closed. The brake is re-
opened when the requirements set by parameters
are met.
0.0 = NOT SEL
0.0…100.0%
Value as a percentage of the maximum frequency (in scalar
control) or the maximum speed (in vector control). If
parameter value is set to zero, the function is disabled. The
control mode is selected by parameter
1 = 0.1%
4307 BRK OPEN
LVL SEL
Selects the torque (in vector control) or current (in scalar
control) applied at brake release.
PAR 4302
used.
1
MEMORY
Torque value (in vector control) or current value (in scalar
control) saved in parameter
used.
Useful in applications where initial torque is needed to
prevent unintended movement when the mechanical brake
is released.
2
50 ENCODER
Encoder connection.
For more information, see
MTAC-01 pulse encoder interface
module user’s manual
(3AFE68591091 [English]).
5001 PULSE NR
States the number of encoder pulses per one revolution.
1024 ppr
32…16384 ppr Pulse number in pulses per round (ppr)
1 = 1 ppr
All parameters
No.
Name/Value
Description
Def/FbEq
Summary of Contents for ACS355 series
Page 1: ...ABB machinery drives User s manual ACS355 drives ...
Page 4: ......
Page 16: ...16 ...
Page 32: ...32 Operation principle and hardware description ...
Page 58: ...58 Electrical installation ...
Page 74: ...74 Start up control with I O and ID run ...
Page 106: ...106 Control panels ...
Page 120: ...120 Application macros ...
Page 178: ...178 Program features ...
Page 338: ...338 Fieldbus control with embedded fieldbus ...
Page 368: ...368 Fault tracing ...
Page 404: ...404 Dimension drawings ...
Page 410: ...410 Appendix Resistor braking ...
Page 434: ...434 Appendix Permanent magnet synchronous motors PMSMs ...