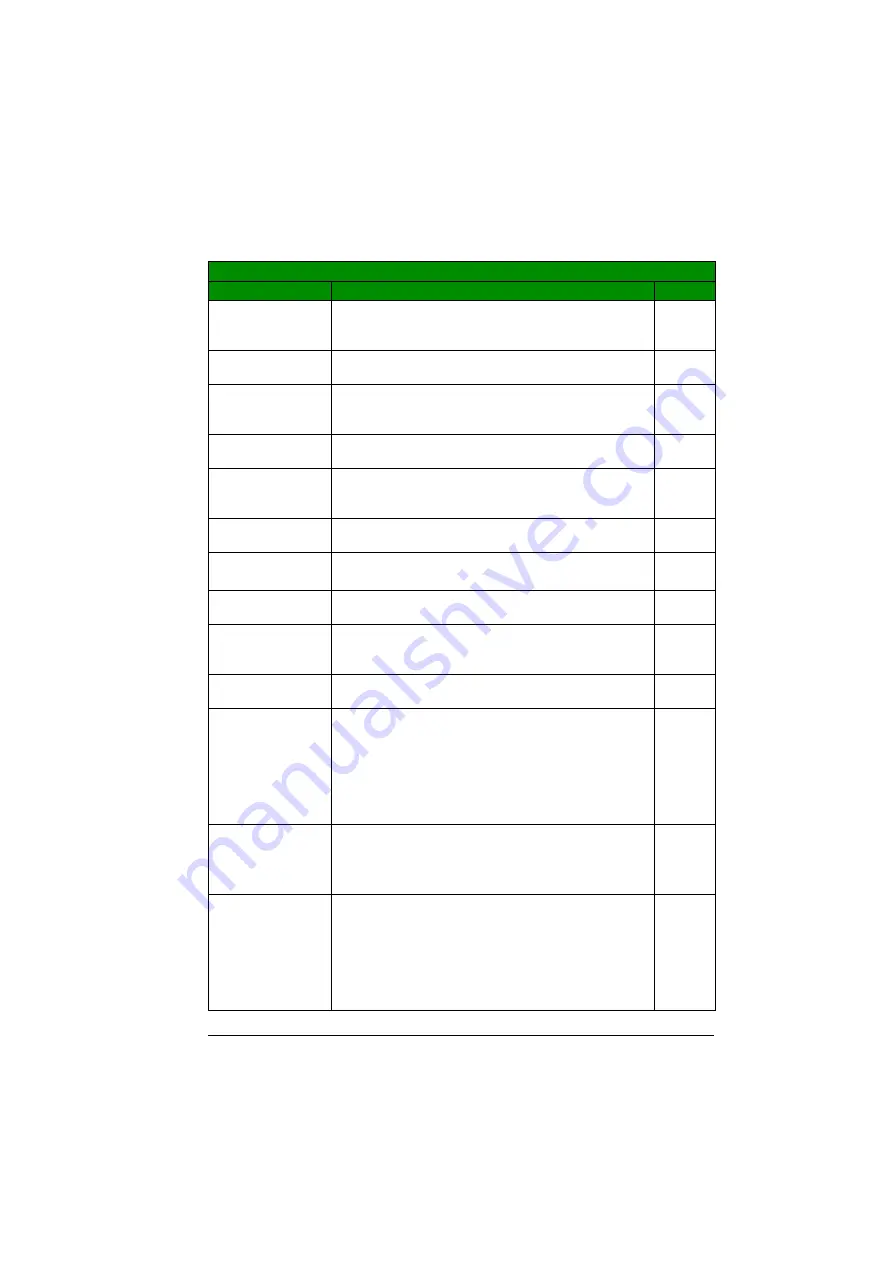
Actual signals and parameters 309
USER S1
LOAD
User 1 macro loaded into use. Before loading, check that
the saved parameter settings and the motor model are
suitable for the application.
0
USER S1
SAVE
Save User 1 macro. Stores the current parameter settings
and the motor model.
-1
USER S2
LOAD
User 2 macro loaded into use. Before loading, check that
the saved parameter settings and the motor model are
suitable for the application.
-2
USER S2
SAVE
Save User 2 macro. Stores the current parameter settings
and the motor model.
-3
USER S3
LOAD
User 3 macro loaded into use. Before loading, check that
the saved parameter settings and the motor model are
suitable for the application.
-4
USER S3
SAVE
Save User 3 macro. Stores the current parameter settings
and the motor model.
-5
9903 MOTOR TYPE Selects the motor type.
Cannot be changed while the drive is running.
AM
Asynchronous motor. Three-phase AC voltage-supplied
induction motor with squirrel cage rotor.
1
PMSM
Permanent magnet synchronous motor. Three-phase AC
voltage-supplied synchronous motor with permanent
magnet rotor and sinusoidal back emf voltage.
2
9904 MOTOR CTRL
MODE
Selects the motor control mode.
VECTOR:
SPEED
Sensorless vector control mode.
Reference 1 = speed reference in rpm.
Reference 2 = speed reference as a percentage. 100% is
the absolute maximum speed, equal to the value of
parameter
(or
if the absolute value of the minimum speed is
greater than the maximum speed value).
1
VECTOR:
TORQ
Vector control mode.
Reference 1 = speed reference in rpm.
Reference 2 = torque reference as a percentage. 100%
equals nominal torque.
2
SCALAR:
FREQ
Scalar control mode.
Reference 1 = frequency reference in Hz.
Reference 2 = frequency reference as a percentage. 100%
is the absolute maximum frequency, equal to the value of
parameter
if the absolute value of the minimum speed is greater
than the maximum speed value).
3
All parameters
No.
Name/Value
Description
Def/FbEq
Summary of Contents for ACS355 series
Page 1: ...ABB machinery drives User s manual ACS355 drives ...
Page 4: ......
Page 16: ...16 ...
Page 32: ...32 Operation principle and hardware description ...
Page 58: ...58 Electrical installation ...
Page 74: ...74 Start up control with I O and ID run ...
Page 106: ...106 Control panels ...
Page 120: ...120 Application macros ...
Page 178: ...178 Program features ...
Page 338: ...338 Fieldbus control with embedded fieldbus ...
Page 368: ...368 Fault tracing ...
Page 404: ...404 Dimension drawings ...
Page 410: ...410 Appendix Resistor braking ...
Page 434: ...434 Appendix Permanent magnet synchronous motors PMSMs ...