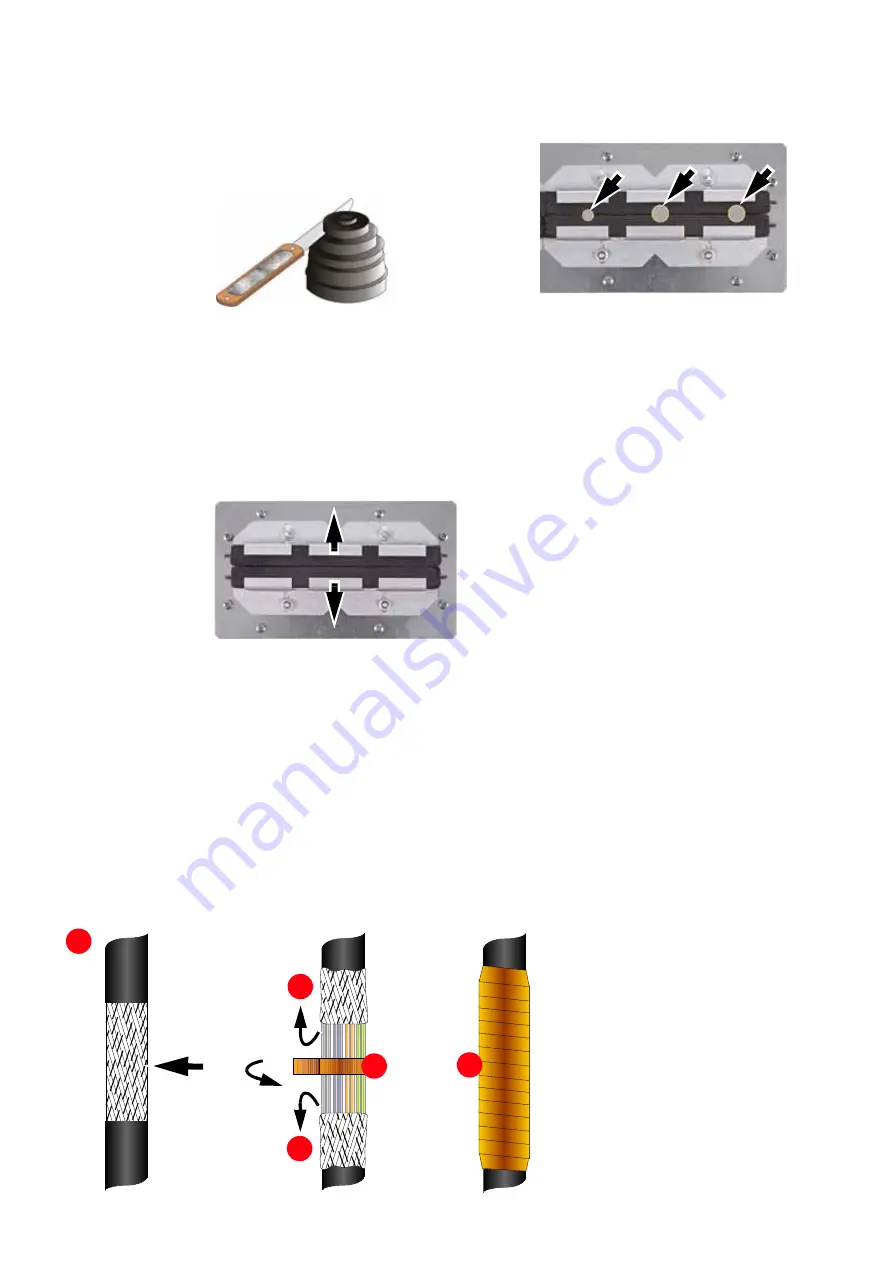
CHAPTER 6 – ELECTRICAL INSTALLATION
104
Preparing cables for EMC plates
Top or bottom cable entry
1. Remove the grommets.
2. To ensure proper sealing, cut along the marking
that corresponds to the cable diameter.
3. Slide the grommet onto the cable. The grom-
met must fit tightly to prevent water entering
the cabinet.
The grommets can be discarded if cables are
entered through the cabinet floor.
4. If necessary, remove the entry plate and pull the
cable through the entry holes.
5. Loosen the screws of the EMC cushion brackets
and push the cushions apart.
6. Remove the cable insulation at the point of
entry
.
If the outer cable screen is non-conductive, cut
open the cable screen in the middle of the
stripped area
. To turn the conductive
side inside out, pull the cable screen ends over
the cable insulation
. Connect the
screens ends with a continuous conducting foil
.
7. Pull the cables through the EMC cushions.
8. Push the cushions together so they fit tightly
around the bare screen and tighten the screws.
—
1
2
2
3
3
—
References
—
6-10 Preparing control
cables for EMC plates
Summary of Contents for ACS2000 AFE 1MVA
Page 6: ...170 Replacing filter mats 171 Phase modules location 171 Phase module Dimensions and weight ...
Page 8: ...Terms trademarks related documentation ...
Page 13: ...13 ACS2000 AFE 1MVA UM 3BHS297030 ZAB E01 REV J ...
Page 14: ...General information on manual and drive ...
Page 19: ...19 ACS2000 AFE 1MVA UM 3BHS297030 ZAB E01 REV J ...
Page 20: ...Important note on main circuit breaker ...
Page 48: ...Chapter 3 Control system 49 Overview 50 Main components 54 I O interfaces ...
Page 67: ...67 ACS2000 AFE 1MVA UM 3BHS297030 ZAB E01 REV J ...
Page 77: ...77 ACS2000 AFE 1MVA UM 3BHS297030 ZAB E01 REV J ...
Page 83: ...83 ACS2000 AFE 1MVA UM 3BHS297030 ZAB E01 REV J 5 1 3 2 1 4 A B C E D ...
Page 85: ...85 ACS2000 AFE 1MVA UM 3BHS297030 ZAB E01 REV J ...
Page 113: ...113 ACS2000 AFE 1MVA UM 3BHS297030 ZAB E01 REV J ...
Page 114: ...Commissioning check list ...
Page 149: ...149 ACS2000 AFE 1MVA UM 3BHS297030 ZAB E01 REV J ...
Page 176: ......