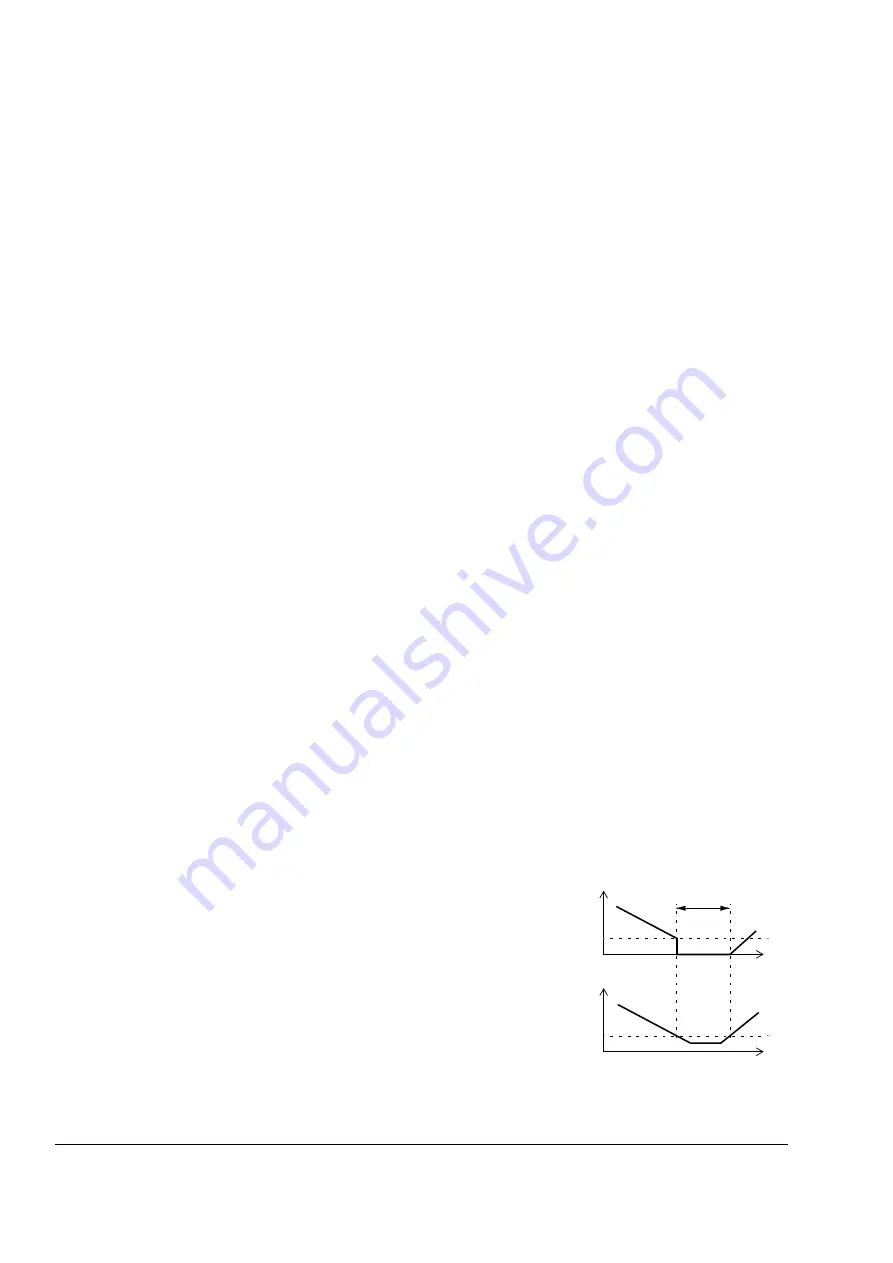
Program features
66
Motor identification
The performance of Direct torque control is based on an accurate motor model
determined during the motor start-up.
A motor identification magnetisation is automatically done the first time the start
command is given. During this first start-up, the motor is magnetised at zero speed
for several seconds to allow the motor model to be created. This identification
method is suitable for most applications.
In demanding applications a separate identification run can be performed.
Settings
Parameter
MOTOR ID RUN MODE
• ID MAGN: Identification with the motor at a standstill and the mechanical brake
closed.
• STANDARD: Identification with a rotating motor and the mechanical brake open.
Diagnostics
Actual signal
.
• Bit 6: First start not done.
• Bit 7: STANDARD ID run done.
Start function: Constant DC magnetising
When DC magnetising is activated, the drive automatically magnetises the motor
before starting. This feature guarantees the highest possible breakaway torque, up
to 200% of motor nominal torque. In crane applications, this parameter is fixed to
constant DC magnetising (CNST DC MAGN).
Settings
Parameters
and
.
DC hold
By activating the motor DC hold feature, you can lock the
rotor at zero speed. When both the reference and the
motor speed fall below the preset DC hold speed, the
drive stops the motor and starts to inject DC into the
motor. When the reference speed again exceeds the DC
hold speed, the normal drive operation resumes.
Settings
Parameters
.
DC hold
t
Motor
DC hold
speed
DC hold
speed
t
Speed
Reference
Speed
Summary of Contents for ACS 800 Series
Page 1: ...ACS800 Firmware Manual Crane Control Program N697 ...
Page 4: ......
Page 26: ...Start up and control through the I O interface 26 ...
Page 36: ...Quick start up guide 36 ...
Page 52: ...Control panel 52 ...
Page 105: ...Program features 105 Figure Control diagram for Shaft synchronisation executed in 20 ms ...
Page 128: ...Program features 128 ...
Page 150: ...Application macros control location EXT1 EXT2 150 ...
Page 228: ...Actual signals and parameters 228 ...
Page 299: ...Adaptive Programming examples for crane control 299 ...
Page 305: ...Adaptive Programming examples for crane control 305 ...
Page 318: ...Analogue Extension Module 318 ...
Page 332: ...Additional data actual signals and parameters 332 ...
Page 334: ...DriveWindow 334 ...
Page 335: ...Control block diagrams 335 Control block diagrams ...
Page 336: ...Control block diagrams 336 ...
Page 337: ...Control block diagrams 337 ...
Page 338: ...Control block diagrams 338 ...
Page 340: ...www abb com drives www abb com drivespartners Contact us 3AFE68775230 Rev E EN 2012 09 25 ...