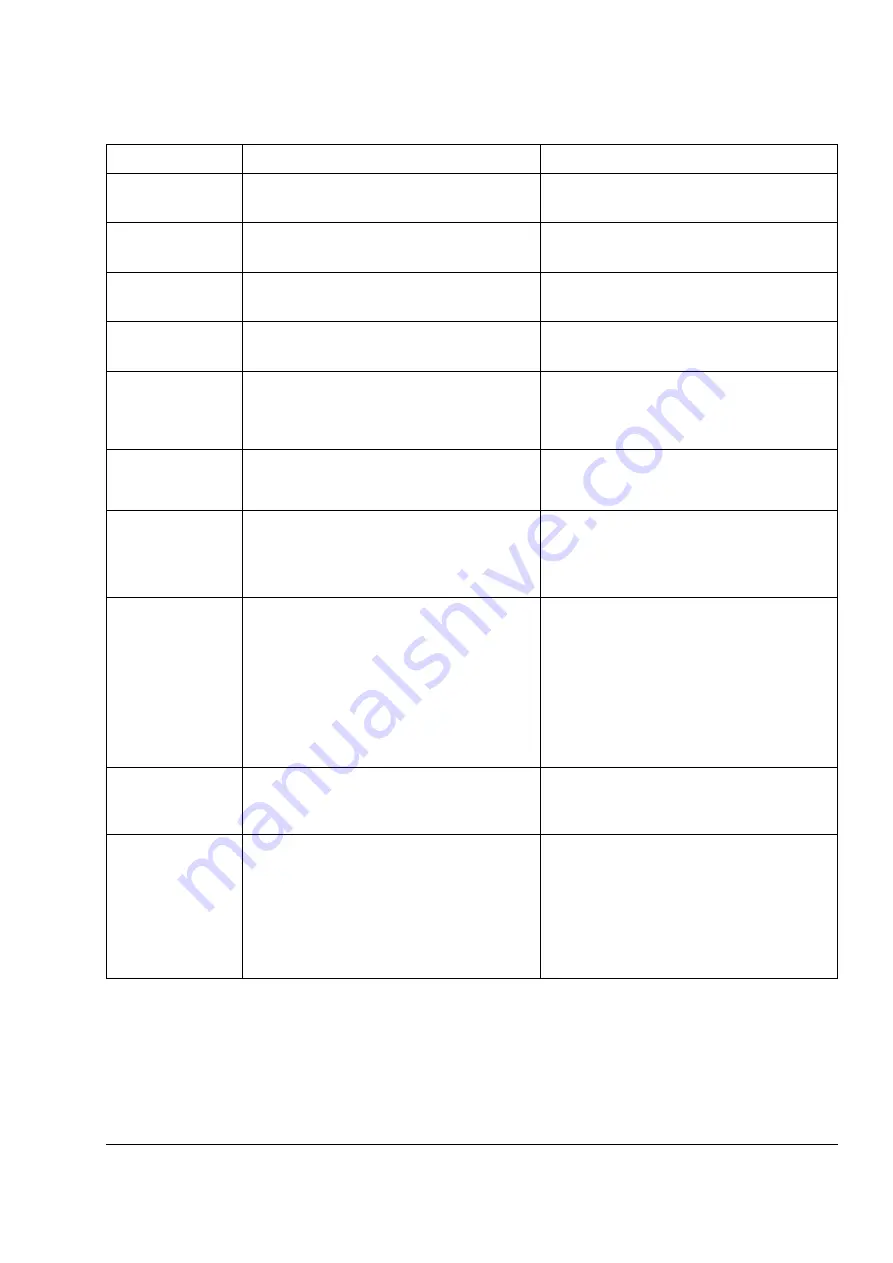
Fault tracing
291
FLWR1 COM FLT
(FFBA)
Follower 1 Communication error .
Check CH2 communication, communication
settings.
FLWR2 COM FLT
(FFBB)
Follower 2 Communication error .
Check CH2 communication, communication
meetings.
FLWR3 COM FLT
(FFBC)
Follower 3 Communication error .
Check CH2 communication, communication
meetings.
FLWR4 COM FLT
(FFBD)
Follower 4 Communication error .
Check CH2 communication, communication
meetings.
GD DISABLED X
AGPS power supply of parallel connected R8i
inverter module has been switched off during
run. X (1...12) refers to inverter module
number.
Check Safe Torque Off circuit.
Replace AGPS board of R8i inverter module.
ID RUN FAIL
(FF84)
Motor ID run is not completed successfully.
Check maximum speed (parameter
should be at least 80% of motor nominal speed
(parameter
).
IN CHOKE TEMP
(FF81)
3.17 FW 5 bit 5
Excessive input choke temperature
Stop drive. Let it cool down.
Check ambient temperature.
Check that fan rotates in correct direction and
air flows freely.
INT CONFIG
(5410)
03.17 FW 5 bit 10
Number of inverter modules is not equal to
original number of inverters.
Check status of inverters. See signal
.
Check fibre optic cables between APBU and
inverter modules.
If Reduced run function is used, remove
faulted inverter module from main circuit and
write number of remaining inverter modules
into parameter
INT CONFIG USER.
Reset drive.
INV DISABLED
03.17 FW 5 bit 7
(3200)
Optional DC switch has opened while unit was
running or Start command was given.
Close DC switch.
Check AFSC-0x Fuse Switch Controller unit.
INV LIMIT
(FFBF)
3.33 CraneFW bit 5
The fault is generated when the drive has hit
TORQUE INVERTER CURRENT LIMIT or IPP
OVERTEMP ALM is active and a period of 200
ms has elapsed. The fault condition is only
checked when the generating power is more
than 10% of motor nominal power and the
speed is greater than 5% of the maximum
speed.
Check the Speed controller torque settings.
Check torque, speed, power limit settings.
FAULT
CAUSE
WHAT TO DO
Summary of Contents for ACS 800 Series
Page 1: ...ACS800 Firmware Manual Crane Control Program N697 ...
Page 4: ......
Page 26: ...Start up and control through the I O interface 26 ...
Page 36: ...Quick start up guide 36 ...
Page 52: ...Control panel 52 ...
Page 105: ...Program features 105 Figure Control diagram for Shaft synchronisation executed in 20 ms ...
Page 128: ...Program features 128 ...
Page 150: ...Application macros control location EXT1 EXT2 150 ...
Page 228: ...Actual signals and parameters 228 ...
Page 299: ...Adaptive Programming examples for crane control 299 ...
Page 305: ...Adaptive Programming examples for crane control 305 ...
Page 318: ...Analogue Extension Module 318 ...
Page 332: ...Additional data actual signals and parameters 332 ...
Page 334: ...DriveWindow 334 ...
Page 335: ...Control block diagrams 335 Control block diagrams ...
Page 336: ...Control block diagrams 336 ...
Page 337: ...Control block diagrams 337 ...
Page 338: ...Control block diagrams 338 ...
Page 340: ...www abb com drives www abb com drivespartners Contact us 3AFE68775230 Rev E EN 2012 09 25 ...