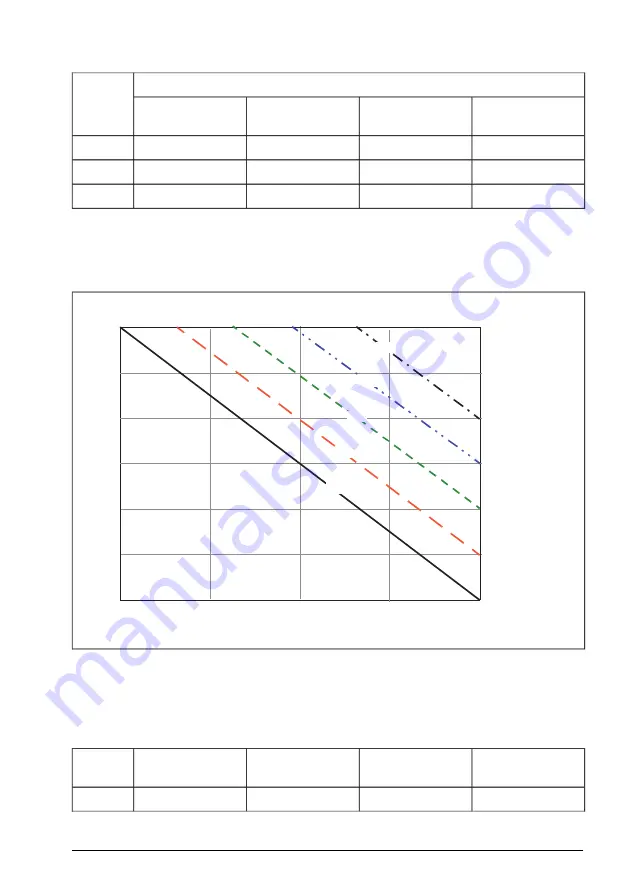
Coeffficient
Frame
4000 m
13123 ft
3000 m
9842 ft
2000 m
6562
1000 m
3281 ft
0.70
0.80
0.90
1.00
R9
0.70
0.80
0.90
1.00
R10
0.70
0.80
0.90
1.00
R11
If ambient temperature is below +40 °C (+104 .°F), the derating can be reduced by 1.5%
for every 1 °C reduction in temperature. Curves with derating factors from 1.00 to 0.80
are shown below. For a more accurate derating, use the DriveSize PC tool. A few altitude
derating curves are shown below.
Installation site altitude
1500 m
1000 m
+25 °C
+30 °C
+77 °F
+86 °F
+40 °C
+104 °F
+35 °C
+95 °F
+20 °C
+68 °F
3300 ft
4921 ft
2000 m
6562 ft
2500 m
8202 ft
3000 m
9842 ft
3500 m
11429 ft
4000 m
13123 ft
1.00
0.95
0.85
0.90
0.80
Ambient temperature
■
Deratings for special settings in the drive control program
If you change the minimum switching frequency with parameter
97.02 Minimum switching
frequency
, multiply the output current given in
by the coefficient value
given in this table.
8 kHz
4kHz
2 kHz
1.5 kHz
Frame
size
0.66
0.84
0.97
1.00
R6
Technical data 201
Summary of Contents for ACQ580-07
Page 1: ... ABB DRIVES FOR WATER ACQ580 07 Hardware manual ...
Page 2: ......
Page 4: ......
Page 8: ...4 Update notice ...
Page 20: ...16 ...
Page 26: ...Measuring points of frames R6 to R9 are shown below PE L1 L2 L3 22 Safety instructions ...
Page 32: ...28 ...
Page 38: ...34 ...
Page 66: ...62 ...
Page 69: ...Mechanical installation 65 ...
Page 73: ... Mechanical installation 69 ...
Page 75: ...Declaration of Conformity Mechanical installation 71 ...
Page 108: ...104 ...
Page 133: ...Electrical installation 129 ...
Page 142: ...138 ...
Page 156: ...152 ...
Page 162: ...158 ...
Page 171: ...Maintenance 167 ...
Page 177: ...3 4 Maintenance 173 ...
Page 184: ...14 13 15 16 17 Remove the flange 180 Maintenance ...
Page 187: ...3 4 5 6 Remove the mounting plate Maintenance 183 ...
Page 189: ...8 Disconnect the drive module output busbars M12 70 N m 52 lbf ft 7 8 Maintenance 185 ...
Page 193: ...4 5 3 6 Remove the mounting plate Maintenance 189 ...
Page 195: ...8 Disconnect the drive module output busbars M12 70 N m 52 lbf ft 7 8 Maintenance 191 ...
Page 218: ...Frame R6 Input and motor cable terminal dimensions option F289 DET A 214 Technical data ...
Page 233: ...Frame R9 Input and motor cable terminal dimensions option F289 Technical data 229 ...
Page 257: ...13 Dimension drawings Example dimension drawings are shown below Dimension drawings 253 ...
Page 258: ...Frames R6 and R7 IP21 UL Type 1 254 Dimension drawings ...
Page 259: ...Frames R6 and R7 B054 IP42 UL Type 1 Filtered Dimension drawings 255 ...
Page 260: ...Frames R6 and R7 B055 IP54 UL Type 12 256 Dimension drawings ...
Page 261: ...Frames R6 and R7 H351 and H353 top entry and exit Dimension drawings 257 ...
Page 262: ...Frames R6 and R7 F289 258 Dimension drawings ...
Page 263: ...Frames R6 and R7 F289 H351 H353 Dimension drawings 259 ...
Page 264: ...Frames R8 and R9 IP21 UL Type 1 260 Dimension drawings ...
Page 265: ...Frames R8 and R9 B054 IP42 UL Type 1 Filtered Dimension drawings 261 ...
Page 266: ...Frames R8 and R9 B055 IP54 UL Type 12 262 Dimension drawings ...
Page 267: ...Frames R8 and R9 H351 and H353 top entry and exit Dimension drawings 263 ...
Page 268: ...Frames R8 and R9 F289 264 Dimension drawings ...
Page 269: ...Frames R8 and R9 F289 H351 H353 Dimension drawings 265 ...
Page 295: ... Declaration of conformity The Safe torque off function 291 ...
Page 296: ...292 ...
Page 302: ...298 ...
Page 309: ...CMOD 01 multifunction extension module external 24 V AC DC and digital I O 305 ...
Page 310: ...306 ...
Page 316: ...312 CMOD 02 multifunction extension module external 24 V AC DC and isolated PTC interface ...
Page 322: ...318 ...