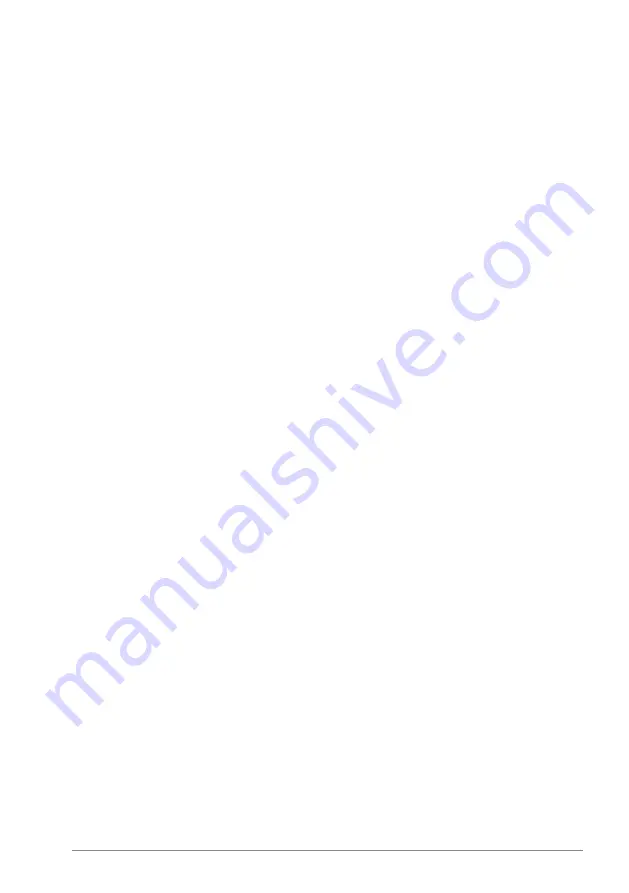
■
North America
Installations must be compliant with NFPA 70 (NEC)
1)
and/or Canadian Electrical
Code (CE) along with state and local codes for your location and application.
1)
National Fire Protection Association 70 (National Electric Code).
■
Other regions
The disconnecting device must conform to the applicable local safety regulations.
Examining the compatibility of the motor and drive
Use asynchronous AC induction motors, permanent magnet synchronous motors
or ABB synchronous reluctance motors (SynRM motors) with the drive.
Select the motor size and drive type from the rating table on basis of the AC line
voltage and motor load. You can find the rating table in the appropriate hardware
manual. You can also use the DriveSize PC tool.
Make sure that the motor can be used with an AC drive. See
. For basics of protecting the motor insulation and bearings in
drive systems, see
Protecting the motor insulation and bearings (page 59)
.
Note:
•
Consult the motor manufacturer before using a motor with nominal voltage
that differs from the AC line voltage connected to the drive input.
•
The voltage peaks at the motor terminals are relative to the supply voltage of
the drive, not to the drive output voltage.
■
Protecting the motor insulation and bearings
The drive employs modern IGBT inverter technology. Regardless of frequency, the
drive output comprises pulses of approximately the drive DC bus voltage with a
very short rise time. The pulse voltage can almost double at the motor terminals,
depending on the attenuation and reflection properties of the motor cable and
the terminals. This can cause additional stress on the motor and motor cable
insulation.
Modern variable speed drives with their fast rising voltage pulses and high
switching frequencies can generate current pulses that flow through the motor
bearings. This can gradually erode the bearing races and rolling elements.
d
u/dt filters protect motor insulation system and reduce bearing currents. Common
mode filters mainly reduce bearing currents. Insulated N-end (non-drive end)
bearings protect the motor bearings.
Guidelines for planning the electrical installation 59
Summary of Contents for ACH580-31
Page 1: ... ABB INDUSTRIAL DRIVES ACH580 31 drives Hardware manual ...
Page 2: ......
Page 4: ......
Page 16: ...16 ...
Page 30: ...30 ...
Page 39: ...Operation principle 39 ...
Page 56: ...56 ...
Page 90: ...90 ...
Page 112: ...R3 1 7 N m 112 Electrical installation IEC ...
Page 113: ...R6 1 7 N m Electrical installation IEC 113 ...
Page 114: ...R8 1 7 N m 114 Electrical installation IEC ...
Page 130: ...R3 Max 250 mA 130 Electrical installation North America NEC ...
Page 131: ...R6 Electrical installation North America NEC 131 ...
Page 150: ...150 ...
Page 152: ...152 ...
Page 166: ... Fan arrow must point up 166 Maintenance ...
Page 212: ...212 ...
Page 214: ...R3 IP21 UL Type 1 3AXD50000028643 214 Dimension drawings ...
Page 215: ...R3 Option B056 IP55 UL Type 12 3AXD50000045321 Dimension drawings 215 ...
Page 216: ...R6 IP21 UL Type 1 3AXD50000037446 216 Dimension drawings ...
Page 217: ...R6 Option B056 IP55 UL Type 12 3AXD50000045351 Dimension drawings 217 ...
Page 218: ...R8 IP21 UL Type 1 3AXD50000147052 218 Dimension drawings ...
Page 219: ...R8 Option B056 IP55 UL Type 12 3AXD50000147052 Dimension drawings 219 ...
Page 220: ...220 ...
Page 242: ...242 ...
Page 250: ...250 ...
Page 254: ...254 ...
Page 262: ...262 ...
Page 268: ...268 ...
Page 275: ...CMOD 01 multifunction extension module external 24 V AC DC and digital I O 275 ...
Page 276: ...276 ...
Page 282: ...282 CMOD 02 multifunction extension module external 24 V AC DC and isolated PTC interface ...