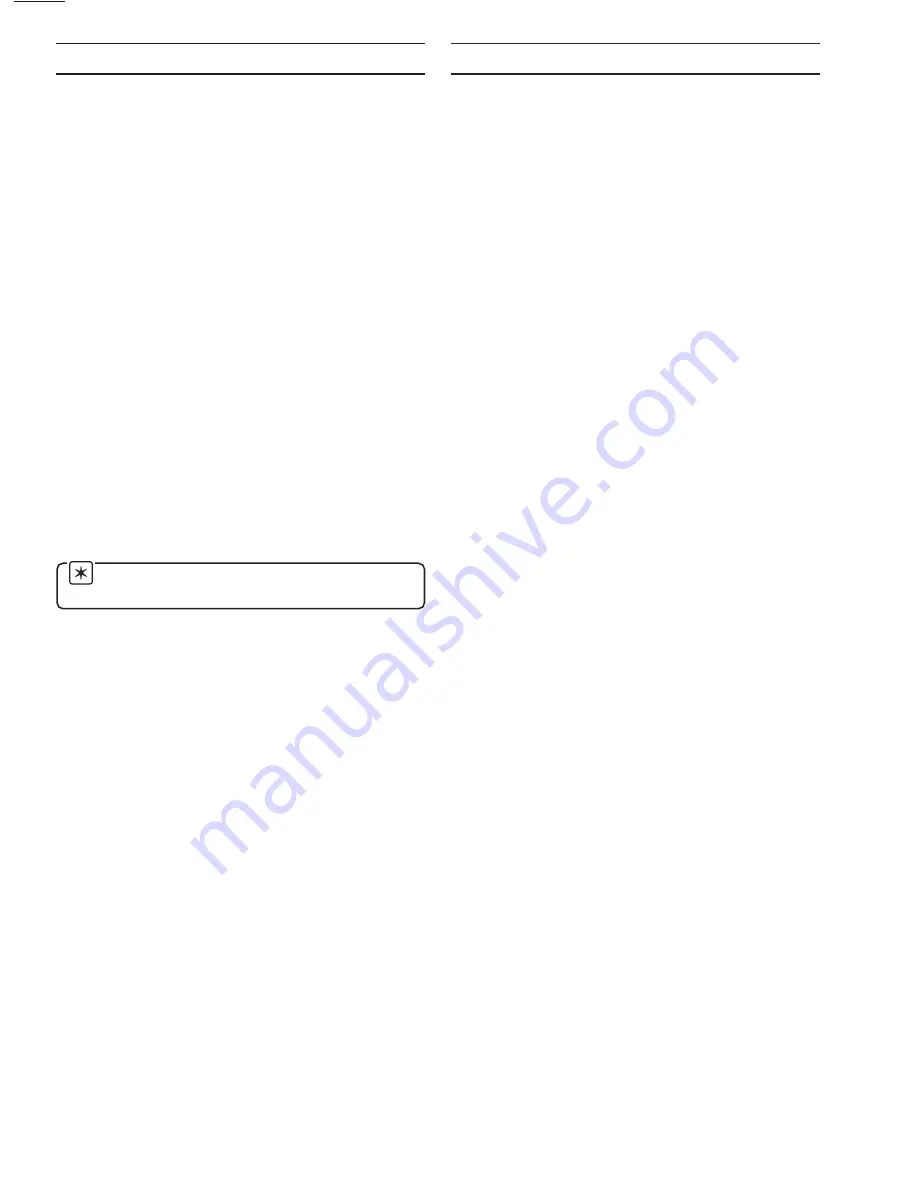
2
1
INTRODUCTION
2
PREPARATION
This Supplement must be read in conjunction with the
Instruction Manual supplied with the instrument:
Instrument
Manual Reference
• Model 8241
Colorimetric Silica Monitor
–
IM/8241
• Model 8242
Colorimetric Phosphate Monitor
–
IM/8242
For repeatable and reliable serial communication to take place
between a master (host computer) and slaves (instruments) it
is essential that the two conditions detailed in this section are met.
1.1
Electrical Connection
A standard method of electrical connection is used between
the master and the slaves, with defined voltage levels and
characteristics. The transmitter and receiver integrated
circuits within the instrument meet the requirements of the EIA
(Electronic Industries Association, American) RS485 and
RS422 Serial Interface Standards.
The RS422/485 communication standard is used with the
following logic levels:
a) for logic ‘1’ (MARK condition or IDLE state) the ‘A’
terminal of the transmitter is negative (0V) with
respect to the ‘B’ terminal (+5V)
b) for logic ‘0’ (SPACE condition or ACTIVE state) the ‘A’
terminal of the transmitter is positive (+5V) with
respect to the ‘B’ terminal (0V).
Note.
The ‘A’ terminal is Tx + or Rx + and the ‘B’
terminal is Tx – or Rx –.
1.2
Protocol
A standard language or protocol must be used in both the
master and the slaves for messages (commands and data) to
be interpreted and acted upon. To achieve this second
condition, MODBUS Protocol is utilized on the 8240 Monitor
using the Remote Terminal Unit (RTU) mode only.
Two methods of message error checking are used. Parity
checking is used, if selected, to detect transmission errors in
individual characters.
Parity is used for simple error checking. The parity bit is a one-
bit code which is transmitted in addition to the ASCII character.
It can detect only one error per character, since two errors may
cancel out. Parity is calculated by finding the sum of logic ‘1’s
in the character and either:
a) setting the parity bit to logic ‘1’ if the sum is odd, or
logic ‘0’ if the sum is even, when using even parity.
or
b) setting the parity bit to logic ‘0’ if the sum is odd, or
logic ‘1’ if the sum is even, when using odd parity.
Cyclic Redundancy Checking (CRC-16) is used to detect
errors in the Master messages and Slave responses. This
therefore detects errors in the complete message sent and
also the replies.
Preparation of the instrument is detailed in the relevant
Instruction Manual, with additions as detailed in this Section.
2.1
Company Standard Settings
Only those parameters detailed on the customer order are
programmed at the factory. If any parameters are unsuitable
for the application they can be reprogrammed –
see Section 6
of the relevant Instruction Manual
. Serial data programming
details are given in Section 7 of this manual.
Standard settings for the serial data parameters are as
follows:
Instrument Identity
01
Parity
None
Transmission Rate
9600 baud
Summary of Contents for 8241
Page 26: ...24 NOTES ...